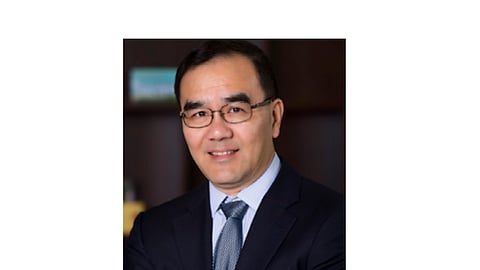
China's state-owned PV manufacturer Jinergy was founded in 2013 by the Jinneng Group, a merger between Shanxi Coal and the Shanxi International Electricity Group.
Jinergy had a PV cell and module production capacity of 1.2 GW multicrystalline and 1 GW monocrystalline at the end of 2018. It is one of the first manufacturers seriously aiming also at heterojunction technology, running a 100 MW pilot plant since 2016. Based on the experience gathered with the first HJT pilot line, Jinergy is exploring a next generation pilot line, before it will decide to move towards the GW-level for HJT technology. In March, after our interview, Jinergy announced a 24.73% R&D cell on its pilot line – while not independently certified, that's the highest reported HJT commercial size cell efficiency so far.
Jinergy is headed by Dr. Liyou Yang, a solar veteran, active in the sector for over 30 Years. He was appointed general manager of Jinergy in 2013. Before joining Jinergy, Dr. Yang was founder and president of Chinese vertically integrated solar module manufacturer Astronergy, a subsidiary of Chint Group. He was counselor of thin-film solar cell research to the US Department of Energy and member of the IEEE PV committee. He also worked in BP Solar's R&D Department and Sarnoff Corporation's New Material R&D Department. At BP Solar, Dr. Yang had a key role in establishing the world's first production line of thin-film solar cells.
TaiyangNews: Your solar cell development focus today is on heterojunction technology, but Jinergy first started with multi and then PERC. Why that?
Liyou Yang: When Jinergy first started in 2013, we obviously had to establish ourselves in the market with something that was going to get us our fair share of the market. And obviously multicrystalline was the dominant product back then. Monocrystalline was much more expensive and not well accepted in China. But then the wind shifted. The mono transition started becoming very successful in 2017 driven by diamond wire-based sawing and PERC technology.
TaiyangNews: What does that mean for you – it looks like the trend towards mono became even stronger. Are you still going to continue with multi?
Liyou Yang: Yes, because we can convert it to monocrystalline at any time by adding a few pieces of equipment, such as a new texturing process. We still see lot of demand for multicrystalline. As long as we have good orders, we are going to continue to run it to meet market demand.
TaiyangNews: But not multi PERC?
Liyou Yang: I still have some doubts about the multicrystalline PERC stability. Monocrystalline PERC has a higher efficiency. Multi PERC requires extra investment. If we're going to convert, we are going to convert to monocrystalline PERC. I think there is a real chance that is going to happen.
TaiyangNews: So why did you decide to invest in a pilot line for heterojunction?
Liyou Yang: The factors that led us to choose heterojunction technology in 2016 is that the
product is quite unique in its performance. For one, there is the inherent high conversion efficiency. Heterojunction has high bifaciality, a low-temperature coefficient, no PID, it has less light-induced degradation. And heterojunction has a longer lifetime for generating electricity, and hence a higher yield compared to any other high-efficiency technologies. Also, heterojunction production is simpler. It only has four major steps. That gives us the opportunity to lower the cost. In addition, we have a lot of experience in thin film as well as in crystalline silicon. That is how Panasonic first got into heterojunction – by doing thin film and combining it with crystalline silicon. In the end, there is nothing more convincing than heterojunction.
TaiyangNews: If you look at the cost reduction potential of heterojunction versus other high efficiency cell technology candidates, do you think HJT is the most attractive?
Liyou Yang: Yes. Some of our theoretical thinking has been validated in actual production capability. We are now more confident that heterojunction technology can be cost competitive in a relatively short time. Especially due to the reduced number of process steps. But if we didn't have a mature flat- panel display industry, I think it would take the solar industry much longer to develop production-proven equipment, materials or processes.
TaiyangNews: What's are your HJT expansion plans?
Liyou Yang: Our plan is to continue to develop our know-how at a scale of 100 MW for R&D, then start up a second 100 MW line at a lower cost. By doing this, I hope to reach the ultimate level of competitiveness – a GW-scale of mass production capacity. We are not there yet, but maybe in 1.5 to 2.5 years.
TaiyangNews: Aren't you worried that PERC is being developed faster than heterojunction – and with a higher efficiency than most people thought. Is there a danger that the window for heterojunction is closing?
Liyou Yang: No, there is a limit for what PERC can do. I am not really scared by the extremely
high numbers announced by PERC followers. It involves lot of non-manufacturing steps. Reaching an efficiency of 25% or above in the laboratory using fancy technologies is easy. But we are talking about true mass production at low cost. Any expert in the field of PERC would probably tell you that its mass- production efficiency limit is probably going to be in the 23% range. More than that is not too likely to happen. For heterojunction, attaining 25% is not really beyond our reach. Maintaining a gap of 2% points between the two technologies is realistic.
TaiyangNews: What is your opinion about the passivated contact cell concept?
Liyou Yang: It's too early in the game. Passivated contact is still a laboratory concept, and the high efficiency attained in the lab is done with what I consider non-production, unworthy techniques. Heterojunction already has a lot of existing and proven production, while the passivated contact technology has yet to demonstrate its capability as a full-scale production process.
TaiyangNews: So you believe that heterojunction will be able to maintain an efficiency lead also over passivated contacts?
Liyou Yang: Yes. But you can never be sure, because there are so many smart people in
the industry. I would say, you should never say never [laughs]. But it's a healthy competition. If I commercialize heterojunction by putting in a GW factory, I would be worried about any potential competition. People who make certain decisions now might regret it later. That's not completely uncommon. I mean, who would have imagined that multicrystalline would recede so quickly.
TaiyangNews: What has Jinergy learned by setting up a 100 MW heterojunction pilot line?
Liyou Yang: In the beginning, we thought 22.5% was a reasonable target. Now we have clearly surpassed that. Even though we are not completely there yet in terms of high efficiency and lower costs, we are confident that we have mastered the mass production technology. Just this alone is worth the effort. We have uncovered a lot of unknown factors and gotten them under control. The fact that we can demonstrate an average yield of about 98% is a significant proof of our capability to take this technology into mass production. Lots of people have proven very high efficiency in laboratory scale, but for production what is really important is the average efficiency. When we started it was about 21%; now we are about 23.7%. We think there is still room for improvement. The distribution is still not symmetrical and still has a tail that we can cut. But we are very confident that we will be able to reach the average efficiency of 24% soon.
Even though some of the cost reduction cannot be completed on the first line due to the line design, we have identified the major cost reduction items that will enable us to reach the ultimate goal of having heterojunction in parity in costs with PERC. There are several cost factors specific to heterojunction technology we have identified and are actively developing solutions to each that are already being incorporated into the design of the next line. A few are related to the supply chain for heterojunction, for example, the rotary target used for the deposition of transparent conducting oxide (TCO).
TaiyangNews: And what about the equipment for the new line?
Liyou Yang: We know enough about what we need the equipment to do and are capable of telling a specific equipment company what our requirements are, so that they can develop the equipment meeting our specs. For the first line, we were directly borrowing equipment that is being used in other industries, mainly the flat-panel display. The first line helped us discover what we needed to optimize.
TaiyangNews: If you look at the optimized equipment you have and then compare the capex with a traditional PERC line, what is the factor there?
Liyou Yang: Right now, without the scale, even with optimization, the capex per watt is still going
to be higher compared to PERC. The PERC line is not cheap either. However, it is going to come down further when the scale factor for the equipment company kicks in.
TaiyangNews: Would a new 1 GW line bring down the cost much, because we are talking about 6,000 wafers per hour which is 200 MW – and that means five machines? So the scale is not really big. It is only a little bit higher.
Liyou Yang: Well, with 1 GW, at least you are going to be able to get your market presence. And it's
not the end of the game. It could be even 100 GW, although that could take some time to reach.
TaiyangNews: Let's assume you have the capex on a level with PERC or maybe lower. How would this translate into cost per watt?
Liyou Yang: Right now, with the first line, we are roughly about 150% compared to multi per watt.
We are driving this down with the things we can adopt, but some fixed costs are not going to change. We hope in the near future we will be about 115% compared to mono PERC.
TaiyangNews: At the cell level, do you see any scope for optimization in the design? For example, for a reduction in the use of silver paste?
Liyou Yang: You can really cut a lot by using new module technologies like multi busbars (MBB). Such technologies can help cut the silver used for busbars.
TaiyangNews: Can you say what are you trying to optimize for metallization?
Liyou Yang: Metallization has two primary aspects. Interconnection technology for modules and working with the paste developers to further optimize the special low-temperature cured metallization pastes.
TaiyangNews: Does that mean you are going to stick to the standard and not use any fancy technology like plating?
Liyou Yang: We are not ruling out anything. If it is good, we use it. If not, we won't. We are open for collaboration with anyone.
TaiyangNews: What about your module design?
Liyou Yang: We are developing new module technologies suitable for heterojunction technology. Right now, we are following both the traditional design with five busbars and MBB.
TaiyangNews: That means you are also doing traditional soldering?
Liyou Yang: Not traditional. It's a special soldering.
TaiyangNews: For the next generation, are you also thinking about advanced module technologies?
Liyou Yang: We are already doing that, but we have not yet added it to our commercial production. But we can do them at any time. The module technology is also compatible with the old line. We just need to change the cell layout. The approach can cut at least 50%, if not more, in silver paste consumption. We are planning to introduce these modules in Q2/2019.
TaiyangNews: What do you think about the supply chain specifically for heterojunction technology?
Liyou Yang: Since our volume is really small for the R&D line, I can't really complain. But for real commercial production, a lot has to be done. I think the supply chain industry is starting to see the light.
TaiyangNews: What are the major challenges heterojunction technology is facing today?
Liyou Yang: The biggest challenge is the supply chain. And its development is going to take some time. Our strategy here is we are not trying to co- operate with new companies who start from zero, but to leverage the supply chain that already exists for the solar industry, as well as the other related Industries like flat-panel display. And we need to scale up. In this industry you cannot afford to make a lot of big mistakes. It is relatively easy to make decisions at 100 MW. But the major challenge here is thin margins. So you don't have enough cushion to withstand the aftermath of the mistake made in choosing a direction that may not prove to be so optimal, or to correct when scaling up production.
TaiyangNews: What is the biggest benefit you see on the horizon by going to heterojunction?
Liyou Yang: It has the potential to become a next- generation technology, akin to what PERC or mono is today. Then we could become a very profitable leader. And as such, we would enjoy higher profit margins ahead of any of the competitors and have a very profitable period for a couple of years. That could happen with heterojunction. Since it is a more difficult technology, I don't think average players can do well in this technology. That means we could stand out with a substantial differentiation against competition.
TaiyangNews: Thank you for the interview.