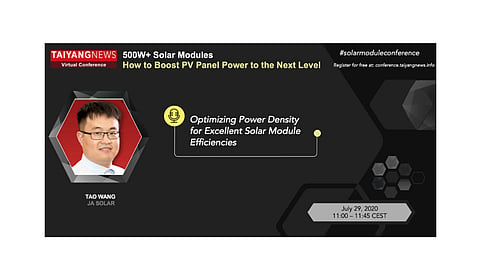
Over the past few months, leading module makers have been in a race to bring higher power modules to the market, raising the bar for utility-scale panel power to 500 W and more. Acknowledging the trend, TaiyangNews organized a virtual conference on the topic: 500W+ Solar Modules - How to Boost PV Panel Power to the Next Level (see TaiyangNews Virtual Conference on 500W+ Solar Modules). All leading module producers that had announced 500W+ modules in H1/2020 took part in the event and presented details of their technologies. We are summarizing the company presentations at the event and also include the Q&A parts—here, for JA Solar.
In the past, the average annual increase in module power was 10 W and improvement in efficiency was about 0.6% per year. However, since 2018, module power has been increasing at a faster pace with larger wafers, high efficiency PERC cells and new module assembly technologies such as half-cell and MBB technologies. This was the opening remark of Tao Wang from JA Solar at the TaiyangNews 500W+ Module Conference. JA Solar is one of the leading companies that started working on large high-power modules that have power ratings of 500 W and above. The integrated module producer introduced its latest DeepBlue 3.0 module series, the top model of which has a power rating of 545 W, in May 2020. In his presentation, Wang provided some background on the DeepBlue 3.0 series modules and the design elements.
The main motivation for a higher module power is the potential to reduce manufacturing costs. For integrated companies, according to Wang, increasing the module power from 400 W to 500 W reduces normalized costs by 2% during wafering, 13% at cell manufacturing and 10% at module assembly lines. New cell technologies and several advanced module assembly approaches such as bifacial, half cut and MBB have been helping to increase the power; however, employing larger wafers is enabling larger jumps.
Determining the optimal wafer size
In today's market, 182 mm and 210 mm are two wafer sizes that are enabling module powers to reach and surpass 500 W. At the time of the conference, JA Solar was one of the four top league module makers that had adopted the 182 mm wafer format. Considering several factors, such as the size gap compared to the current mainstream wafer sizes G1 and M6, complexities in updating production lines, maturity of manufacturing tools, processing technology and materials, and the current production yield, JA Solar found that the 182 mm based module product is the best choice as things stand. Another important consideration behind settling on the 182 mm wafer size is the module size, especially the width. The module width not only restricts the number of modules that can be loaded into a 40-feet container, it is also an important consideration for the supply side of the glass. According to Wang, 2,300 x 1,150 mm glass will be in mass production in the second half of this year. "Taking these two limitations into consideration, 182 mm wafer size with 72 half-cells is the current optimal level for 500 W+ modules."
Upgrades at cell level
JA Solar has also made improvements to the cell technology that are integrated into the DeepBlue 3.0 modules. The so called "PERCIUM+" technology is based on its p-type monocrystalline PERC platform that is superior in three aspects. The passivation on the rear side has been improved for better long wavelength response that improves Voc. These cells also feature selective emitters to reduce contact resistance of the metal and semiconductor on the front and back, improving the fill factor. JA Solar has employed a new printing process on the back to improve the bifaciality and mechanical load performance of the module. This set of improvements enable the cell to realize efficiencies of 23% and above, claimed Wang. Reliability is also of great importance. As a step forward in this direction, JA Solar is implementing gallium doping technology to reduce degradation and improve anti-LID performance.
Module features
DeepBlue 3.0 has four advanced module features—MBB, half-cell, double ARC glass and a slot frame. The advantages of MBB are well known, such as better optical performance, lower cell-to-module (CTM) losses and preventing power loss due to micro-cracks and broken fingers. Wang underscored that the MBB interconnection using 11 circular copper wires boosts the module power by 5 W. JA Solar is employing a special surface structured circular ribbon that enhances the power by 1%. The half-cell design, in addition to reducing losses due to internal resistance and mismatch, also helps in reducing NOCT by 2 to 3 oC lower than a full cell. All these factors boost module power by 8 to 10 W. The company is employing an optimized laser cutting process to reduce laser induced damages. A double ARC glass with a transparency of 94% is used for building the DeepBlue 3.0 series that helps in improving module power by 3 W. DeepBlue 3.0 also features a patented slot frame design, which is not only light weight, but also offers convenience in installations and better mechanical load performance.
Deployment & benefits
DeepBlue 3.0 will officially enter mass production in Q4/2020 with a total planned capacity of 14 GW by end of 2021. The main focus would be the 72-cell 540 W module. While the standard product is a narrow gap based design, the company is also willing to honor special orders for modules based on Tiling Ribbon technology, which has 0.4% higher module efficiency, according to Wang. The module based on Tiling Ribbon technology uses optimized materials and lamination process to reduce power loss and the risk of microcracks.
JA Solar provided the results of its simulations considering Dubai as the installation site with a plant size of 360 MW based on a single axis tracker. DeepBlue 540 W bifacial panels enable 8 to 10% reduction in LCOE compared to 405 W modules based on the simulations.
Outlook
Looking forward to development prospects, Wang emphasizes that the current 540 W is just the starting point of super high-power modules. The modules based on 182 mm wafer format have abundant possibilities to enhance the output power further; the 78-cell version with 182 mm is one example. There are also possibilities to increase the wafer size marginally to 185 mm and module power beyond 600 W. "JA Solar will gradually develop products in the near future that best suit our customer requirements," said Wang as a closing note. And indeed, at the SNEC trade show in early August, JA displayed an up to 810 W module with 240 cells (triple cut) and based on 210 mm size wafers, which will be not only the most powerful but also the largest "standard" solar panel once it will be available.
The presentation was followed by a Q&A with the conference attendees, which we have listed below (selected questions, edited & summarized):
Question: It is very impressive that you are planning to go up to 14 GW for DeepBlue, but JA's total capacity was 16 GW at the end of last year. So when you have 14 GW output for the new product, how much will your total capacity be at that point?
Tao Wang: End of this year it would be 20 GW and end of next year 23 GW.
Question: You mentioned 23% cell efficiency, which is very high for PERC. How much of your production output can reach such high efficiencies?
Tao Wang: For cells with 5-busbars, efficiencies are about 22.3%. The 23% is with MBB. The fabs are also new and the process has also been improved in the new fabs. With our latest cell lines, I already see mass production efficiencies reaching as high as 23.1%.
Question: Now you have gallium doping technology; as of when will all cells be gallium doped exactly?
Tao Wang: JA Solar currently has DeepBlue 1.0, 2.0 and 3.0 series. The 1.0 is G1 wafer size, 2.0 is M6 wafer size and 3.0 is M10 size wafers. Starting from Q3, all these wafers will be gallium doped to provide better anti-LID performance across the product spectrum.
Question: You have discussed a couple of design aspects of the 500W+ big size modules. Are there any other factors that one should look beyond what you mentioned in your presentation when designing 500W+ modules?
Tao Wang: We see that other companies are designing 600 W or even 660 W. One should consider the weight of the panels. That's because different countries have different norms for labor; the weight is too high, so one may need to use machines and it may not be possible manually. This could be tricky in some areas. When designing such big panels, we need to pay attention to size that is compatible with the trackers. Such larger module size may affect the stability of single axis trackers. Such a module may reduce module costs but could also increase the tracker costs considerably.
The panels are so big that the current is higher, thus we must consider the safety aspects. For example, with more than 20 A current, one has to pay attention to the cables.
Question: With the MBB and gallium doping, you are able to increase the currents, but how do you increase the Voc beyond 700 mV? Are you also evaluating passivated contacts? And are you discussing n-type solar cells internally?
Tao Wang: We have been working on n-type for quite long. At JA Solar, we call it BICIUM+. The efficiency is 1% point higher than the current p-type PERC at about 24%. The problem with the n-type wafer size development is it is not fast as p-type. So, the final module power is a little lower than p-type and cell conversion costs are a little higher. That's making p-type more advantageous than n-type till now. With gallium doping, LID would also not be an issue with p-type, a USP claimed by n-type thus far.
Question: Does the gallium doping, which you licensed from Shin-Etsu, also increase the costs?
Tao Wang: Yes, but limited. The benefits are higher.
Question: Are the data sheets for DeepBlue 3.0 publicly available?
Tao Wang: We can send them to interested customers.
Question: At JA Solar, what do you think are the most important factors for long-term reliability of high-performance technologies? How do you make sure you can guarantee long warranty periods?
Tao Wang: We do a lot of reliability tests that are part of our design process. Even with DeepBlue 3.0, we do these tests for prolonged time periods, for example three times the IEC test for performance. The new IEC standard is also paying more attention to reliability, and we also actively implement these tests with our new products.
Question: What is the encapsulation you are using? POE, which has better reliability, or EVA?
Tao Wang: For monofacial we mainly use EVA, but for bifacial JA Solar's stand is to use POE. POE has better reliability as we are offering 30 years warranty for glass-glass modules.
Question: How do you ensure that 500 W+ modules meet the IEC standards in the sun simulator and other accelerated testing?
Tao Wang: We conducted those tests and our modules passed those tests.
Question: Why is NOCT lower when you use half cells?
Tao Wang: That's mainly because of the current, which is half compared to full cells. The internal resistance also causes some increase in the module temperature. Half-cell with low internal resistance reduces NOCT to some extent. What we have found in our R&D lab is NOCT reduces by 2 oC on average compared to full cells. We are in the process of collecting more data.
TaiyangNews: Thank you for your presentation at the TaiyangNews 500W+ Solar Module Conference.
The JA Solar presentation of Tao Wang can be viewed on the TaiyangNews YouTube Channel here.