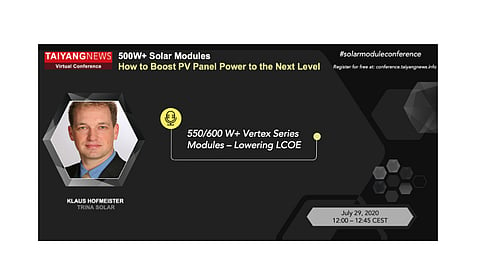
In the last few months, leading module makers have been in a race to offer higher power modules raising the bar for utility-scale panel power to 500 W and more. Acknowledging the trend, TaiyangNews organized a first virtual conference on the topic: 500W+ Solar Modules - How to Boost PV Panel Power to the Next Level (see TaiyangNews Virtual Conference on 500W+ Solar Modules). All leading module producers that had announced 500W+ modules in H1/2020 took part in the event and presented details of their technologies. We are summarizing the company presentations at the event and include also the Q&A parts – here, for Trina Solar.
The leading modules manufacturers are split into two camps when it comes to the approaches leading to module powers beyond 500 W. One group is currently adapting the 182 mm (M10) wafer format; and then there are the followers of 210 mm (G12) wafer sizes, such as Trina Solar. The Chinese solar company is one of the earliest adaptors of the 500 W+ modules design. After launching its first 500 W+ product at the end of February, Trina Solar has recently introduced a next generation Vertex module series with rated power of 550 W and 600 W (see Trina Launches 600 W Vertex Modules). Klaus Hofmeister, the product marketing manager for Europe at Trina, has presented design intricacies of this module series and discussed the optimization required at the system level along with the benefits of high power modules at TaiyangNews virtual conference on 500W+ Solar Module end of July. While the 600 W level is currently the highest power level for solar modules, Hofmeister anticipates module powers to increase further.
Module design
As with the previous Vertex series with up to 500 W output power, the latest generation of Vertex modules is also based on the 210 mm (G12) wafer platform. However, unlike the earlier Vertex series, which was based on solar cells cut in three parts, the new product series employs a half-cut cell design. The 550 W module series comes with a matrix divided into two parts at the top and bottom half of the module, and each with 5 x 11 cells (1/3rd cells). The 600 W product is built with the same setup, however, the matrix configuration changes slightly to 6 x 10 cells (half cells). Due to the changes for the number of cells and their arrangement in the matrix, the module dimensions have changed as well; the latter is slightly shorter and wider compared to the 550 W variant. The 600 W module reaches a somewhat higher efficiency of 21.2% compared to 21% efficiency for the 550 W panel. The other technology elements, such as MBB, non-destructive cutting of cells, high density layout are essentially the same across all variants of the Vertex series.
While Trina introduced MBB with its products a year ago, it has now adapted the technology also for larger wafer-based modules. The benefits of MBB are well known – improved light capturing, better heat distribution in the module, reducing the series resistance and improved reliability.
Non-destructive cutting, which was originally developed for 1/3 cells technology, is now also implemented for half cells of the new Vertex modules. The conventional laser abrasion technology uses laser melting; that means the cells are heated up from the backside to more than 1,500 oC in order to melt the silicon, and the cell pieces are separated mechanically. The process leaves a rough cutting edge, which can be the source of mechanical or micromechanical damages within the cell at the point of cutting. Trina has developed inhouse a non-destructive cutting technology based on low temperature processing. "We are not going to the melting point of silicon," said Hofmeister during his presentation, adding, "There are no structural micro damages in this cutting edge." The next important feature of this module series is high density interconnection technology. The traditional inactive gap between cells in a module is 2 mm large, while Trina has reduced this gap down to 0.5 mm or even below with the help of conventional solar joints.
The latest generation with Trina's Vertex module design is also offering flexibility in terms of mounting configuration. In addition to providing the maximum loading in different clamping position, Trina is currently evaluating the compatibility of its modules with leading trackers leading suppliers. At the same time, the company is also offering its own tracking solutions.
Benefits of big wafers
A key advantage of the new version Vertex modules is the low voltage, which offers higher system design flexibility – the possibility to design systems with very long strings, more power per string, less string cabling. With Trina's Vertex 600 W modules, the string power could be close to 20 kW, while the 585 W module based on 182 mm can reach a string power of 14 kW, based on a 1,500 V maximum system voltage. The higher number per string also reduces the required mounting rails on a MW basis, emphasized Trina. Considering the amount of steel needed for mounting structures per MW, installations using the Vertex top module can save 7 tons of steel versus a reference 585 W module. Moreoer, fewer strings save on cables costs.
For example, the 550 W series has a voltage of 38.1 V, which according to Hofmeister is an important benefit for system designers enabling installations with long module strings. Keeping the maximum voltage at 1,500 V, installers can connect more modules while the power of string increases. A slight disadvantage of these modules with larger wafers is its high module current of above 18 A, which is a constraint but not a showstopper, according to Hofmeister. He said because of the high module current, system components such as inverters, combiner need to be adapted to work with high power and high current modules – but work is in progress. "By the time the new modules hit the market, the compatible components will also be ready," said Hofmeister. Another consideration for system design with high current modules would be thicker cables. However, Hofmeister said that 4 mm2 or at the max 6 mm2 cables are sufficient to handle high currents. Although the higher currents also cause losses in cabling, Hofmeister said that this is within the acceptable range of most system designers.
Trina presented a simulation with results for a specific project, which indicates that the cost structure is in favor of 600 W modules, enabling reduction in LCOE in the range of 2 to 3%.
Production and capacity plans
While the first products of the earlier 500 W Vertex series are coming out of the new manufacturing lines based on 210 mm, Trina is planning to start mass production of the next generation Vertex modules – 550 W – in Q4/2020. In Q1(2021, the 600 W module series is scheduled to enter commercial production, and the products will be available in mid-2021. Trina also presented aggressive growth plans – it forecasts to have 10 GW module production capacity for the overall 210 mm product technology in 2020, which is expected to increase 21 GW in 2021 and 31 GW in 2022.
The presentation was followed by a Q&A with the conference attendees, which we have listed below (selected questions from TaiyangNews and attendees, edited & summarized):
Question: You said you don't see the end of the module growth phase, although it has been already very steep in the last few weeks; where are we going in terms of module size and power?
Klaus Hofmeister: As for size there are limitations definitely on the production side. Production equipment is one limitation, but availability of the some of the components like glass is something which limits the size. In terms of power development, we will see even higher power modules going up to 650, 660 or even up to 700 W. I am not sure if there will be or where will be the end. It would be very difficult to predict from today's perspective. I am quite confident that we are not at the end of this development. The key focus is also further lowering LCOE. For this reason, all module manufacturers are looking into new module designs, new cell technologies or maybe even larger cells of more than 210 mm. There is some development space for further technological improvements. However, this should not be only seen in terms of growing size, but also increasing efficiency – and not only on the module level, but also at cell level. This is not only about new technologies such as # HJT or n-type, but also about improving p-type PERC technology further. There are few screws which we can finetune and this development will continue.
Question: So, you could imagine cells larger than 210 mm?
Klaus Hofmeister: I think there is a possibility from a technological point to see wafer formats even increase above 210 mm. We are looking already into that and I hope that this could be successful in the long run. Therefore, I expect that we will see modules going up to 700 W. As soon we are able to manufacture that properly it will be started and launched.
Question: What is your commercial production and availability roadmap for these modules?
Klaus Hofmeister: We are starting 500 W module production as we speak right now – we have started volume production in July. The 550 W module series production will be started by the end of this year. I expect 550 W module volume production to start in Q4, probably December. In the beginning of next year, either Q1 or Q2, we will have the 600 W modules in volume production.
Question: In the past module design was about rather high Voc and lower currents, now it is shifting – can you provide some background on that?
Klaus Hofmeister: This is definitely a big change. With half cell technology everyone wants to reduce a module's internal currents, to lower resistive losses. In fact, we had to decide whether to go to even higher module voltages to achieve 550 W panel power, which would have meant shorter string length and less flexibility in terms of system design. This is the road we don't want to go down. For us, the decision was relatively clear: we can cope and handle higher currents, which are coming with this module generation of 18 to 19 A. Therefore, we are going down with the voltage, which increases flexibility and brings more power per string. Engineers prefer this way, so this is the preference from the system design perspective, according to Trina.
Question: When we spoke to tracker makers, they expressed concerns about larger modules as they have to adapt trackers sizes and deal with different wind loads. As you also produce trackers in house, what has been your experience so far with large modules from the tracker perspective?
Klaus Hofmeister: We are currently in the phase of redesigning our tracker solution for this module type. This larger scale modules are really a challenge and I have to admit we have to adapt all our tracking solutions to this size of modules. That's a drawback. Also, for fixed tilt, this probably means new design rules. But in the end, once the solutions are up and running and set up, we can really harvest its cost benefits
Question: Talking system safety, what to you recommend when designing a system with 600 W modules?
Klaus Hofmeister: With a system voltage of 1,500 V it doesn't matter if you use modules with 600 W or 300 W. The higher current are more or less a challenge, thus we need to make sure that we have to use the right cable diameters in order to keep the losses low. However, there is not more risk involved when using those products than with any other currently existing solar module products.
Question: Some of you competitors have shown larger bifacial modules, but you are focusing on monofacial; what is the strategy behind it?
Klaus Hofmeister: I forgot to mention during the presentation that all our Vertex products are available as monofacial glass-backsheet modules with frame. Each of them is also available as a dual glass bifacial product including frame. These are the two products we are offering for all watt classes. We offer bifacial and monofacial products for both generations – 550 W and 600 W.
Question: How do you see the trend towards gallium doping? JA Solar showed that and others are also jumping on it?
Klaus Hofmeister: Trina has jumped on that as well. This is not something new in the industry and nobody is hiding that. We have adapted our warranty conditions, especially for our newer generations of products. We have reduced the first-year degradation warranty to up to 2% for all our products. I think the industry is more or less on one page here. We are all looking at the same technology enablers.
Question: There is one group of 182 mm followers while Trina is part of the other group that support the G12 format?
Klaus Hofmeister: Yes, Trina is one of the initiators of this group. During the official launch of Trina's 550 W and 600 W modules, this group has been sharing its views on stage. In this group, we want to make sure that products using G12 really make their way into the market by providing also the appropriate module materials and BOS equipment, which is needed to be able to design proper systems (see 39 PV Firms Back 600 W+ Solar PV Module)
TaiyangNews: Thank you for your presentation at the TaiyangNews 500W+ Solar Module Conference.
The Trina Solar presentation of Klaus Hofmeister can be viewed on the TaiyangNews YouTube Channel here.