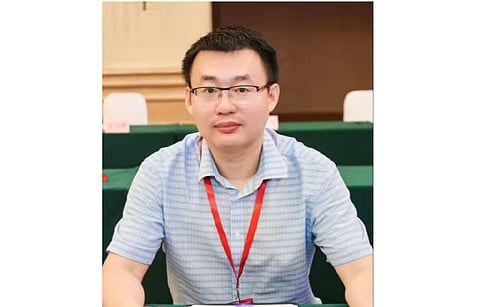
Amid the material shortage and consequent prices hikes, backsheets and encapsulation materials, the key polymer wraps used in module making are increasingly gaining importance. TaiyangNews talked to Xinjun Li, marketing director of Cybrid, one of the two world leading backsheet suppliers. Counting on its strong footprint in the backsheets segment, Cybrid also has ambitious plans to become a key encapsulation materials supplier.
Xinjun Li has a strong academic and research background including a Ph.D in polymer science and prior experience in packing and special plastics at a leading polymer company. He is associated with Cybrid since 2016 in various positions. He was in charge of backsheet and encapsulation materials R&D for 5 years and is now the marketing director at Cybrid.
TaiyangNews: Cybrid is one among few companies that supply all polymer wraps needed for solar module manufacturing. How do you see the market development for these two segments – backsheets and encapsulation?
Xinjun Li: Cybird is a functional polymer material expert. We have strong R&D background in making polymer films based on which we have developed the world's leading backsheet configuration KPf. We also eventually developed an encapsulation solution for PV. But in addition to PV, we also supply our products to various other industries.
As for backsheets, it now has a new competitor in glass. Lower glass prices, coupled with increase in all polymer prices in general, will lead to an increase in the share of glass this year. A significant increase in PVDF prices has increased the price of PVDF-based backsheets more prominently. But we think this is temporary and it will be back to normal as the materials supply situation improves.
The encapsulation segment is more diversifying. More and more white EVA is used in standard modules. And POE is becoming the choice for rear encapsulation of the bifacial modules.
TaiyangNews: What are the most important trends in backsheets?
Xinjun Li: The biggest change this year is the high price of PVDF, which has almost doubled. The price increase is mainly due to the shortage of the resin used for PVDF production. This again is mainly due to the increased demand from electrical vehicles, as PVDF coating is used in lithium-ion batteries. All this has meant that PVDF is in a short supply situation.
TaiyangNews: When do you think the situation would be normal again?
Xinjun Li: We are working in close cooperation with the resin suppliers and feeding them with market intel. If they don't act fast, they may lose the whole PV backsheet market, because there are alternatives available already. One is the CPC structure that is free from PVDF. While the tier 1 module makers are still using the KPf structure, tier 2 companies are already shifting to coating based solutions to save on costs. PET based backsheet is another alternative. The resin makers have acknowledged the situation and are increasing their production capacities. However, our estimate is that the situation will not change much till October 2022.
TaiyangNews: Won't it be too late?
Xinjun Li: What you have to note here is that the price of PVDF has doubled, but not the final backsheet. And the price increase is not just the result of PVDF alone; the prices for all other materials such as PET and glues used in the backsheet have also increased. The final price for PVDF backsheets have gone up by 2 to 3 CNY/m2. It is still affordable. In fact, prices are the same as 3 years ago.
TaiyangNews: Larger modules based on larger wafer formats have been the trend in the industry for some time; what is the impact of this development on backsheets?
Xinjun Li: Such modules require changes to backsheet dimensions and we were equipped to address such demands long back. However, these larger modules are now bringing in a configurational limitation. A few companies, not Cybrid of course, are promoting polyolefin based inner layers. Configurations such as KPO, KPM and KPE fall into this category. These backsheets are failing in hotspot tests for high power modules based on M10 and G12 cells. The reason is simple: the melting point of these films, which is typically between 120 and 165 °C, is lower than the hotspot test temperatures. The fluorine inner coatings based backsheets such as our KPf are able to pass such tests without any issues. Most of the leading companies are refraining from using backsheets with inner polyolefin films in high power modules. I can say it's sort of an unofficial ban.
TaiyangNews: How is the transparent backsheet segment doing?
Xinjun Li: We spent a lot of time in reducing costs and improving the performance of the transparent backsheet. In fact, they are robust enough, and now it's just a matter of costs. This is also evident from what happened last year with several module makers turning to transparent backsheets when glass prices were high. Most of the leading module makers even finished all the testing procedures. But as glass prices dropped considerably since the start of this year, they again moved back to glass.
Looking at the current situation, transparent backsheets did not reach a big share in 2021 and will not do so in the coming months. As far as Cybrid is concerned, our focus is on overseas module makers. For example, in countries like Turkey, the transport of glass from China is very expensive. Importing glass also attracts additional duties. For such markets, transparent backsheets make a lot of sense in terms of costs.
In the end, our competitors aren't other backsheet suppliers, but it is glass.
TaiyangNews: How do you plan to win over glass?
Xinjun Li: As I said earlier, today's transparent backsheets are robust enough in terms of quality. We have to ensure that the price gap between the transparent backsheet and glass is close enough where it starts making sense for module makers. In the current situation, we cannot do it with PVDF-based structures, and that's not just because of the high PVDF price. The transparent variant of PVDF is more expensive than the standard variant, and on top, we have to pay for the special transparent glues. On the other hand, coatings have good potential for cost reduction. FPf coatings meet the requirements in roof application without high humidity. For modules that have to serve in tough weather conditions, we can apply a 5 µm hard coating on the outer side of the coating, i.e., double coating on the outer side. We call these backsheets as 'Skin Cocktail' backsheets.
TaiyangNews: What would be the additional price for such hard coatings?
Xinjun Li: About 1 CNY/m2.
TaiyangNews:: How is the progress with grid backsheets?
Xinjun Li: The white grid applied transparent backsheets are increasingly preferred. However, there is an interesting development in this area as well. We have a white backsheet with black grid for those modules makers that want to produce black modules.
TaiyangNews: What is the benefit of using such a grid when the backsheet is opaque?
Xinjun Li: Black grid on white backsheet is used to replace a total black backsheet. Using a black grid on a white backsheet gives a module the stunning appearance of a black module. To the question of the purpose of a white backsheet itself, companies are making glass-backsheet modules also with bifacial cells. A portion of IR light that would pass through the cells reflects back when using the white backsheet compared to a black rear cover. This way, you can increase the power output of a black module by at least 4 W compared to using a total black one.
TaiyangNews: What is your opinion about the recyclability of backsheets, especially given the backdrop that a few companies are commercializing backsheets made with recycled PET?
Xinjun Li: We are also working in the direction of green backsheets. We already have a product, which is PPf that is offered in two variants – one comes with a fluorine based inner coating and another one has a fluorine free inner coating.
As for other products in the market, there is a wrong notion in the market that all PET based products are green and fluorine based are not. The leading PET based configuration has a polyolefin-based compound as the inner layer, which is hard to decompose in nature. In case of Cybrid's products, even with the fluorine coating, which are just 4 µm, they decompose easily compared to polyolefin film based backsheets, for example PPE structures. PET needs around 100 years decompose, but coextrusion backsheets are using polyolefins (PP, PE), which need million years to decompose. From this pointed of view, I would recommend PET backsheets with inner layers other than polyolefins.
TaiyangNews: How are you positioned in the encapsulation material segment?
Xinjun Li: By the end of 2021, as the entire capacity of Cybrid comes online, we will take 15% of the market share. We will be among the top 3 in the world. As for POE films, we are the biggest supplier in the market; however, for the coextruded structure, our presence is definitely there, but we are far from claiming leadership.
TaiyangNews: Are you focusing on all encapsulation materials or just POE related?
Xinjun Li: We are among the top 4 encapsulation players in the world since September 2021. We supply EVA, white EVA, EPE and POE in market. We mainly supply EVA + white EVA for glass\backsheet modules, and EVA+ EPE for glass/glass modules. So the key product for us is EVA. As for high efficiency technologies, we recommend EPE+ POE for TOPCon and EPE + EPE for HJT modules.
TaiyangNews: So, what are the most important trends you see in the encapsulation segment?
Xinjun Li: In bifacial double glass modules, the encapsulation material of choice for the front is EVA and coextruded EPE for the rear. For glass-backsheet modules, the front side is transparent EVA and about 70% of the market switched to white EVA for the rear side.
TaiyangNews: Thank you for the interview.
The interview is an excerpt of TaiyangNews' Market Survey on Backsheets & Encapsulation, which is available for free download here