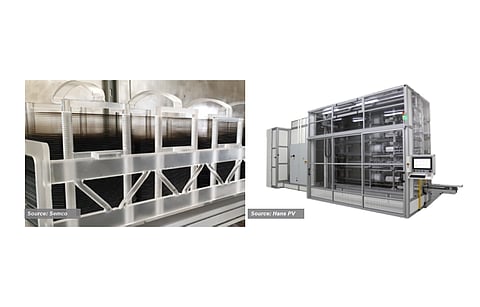
Diffusion is the step that comes after the surface conditioning process in solar cell production (see Solar Cell Surface Preparation). From a physics point of view, a solar cell is essentially a p-n junction diode, and the wafers entering the cell lines are base doped (p or n-type). In order to realize a solar cell from these incoming wafers, the emitter is formed by doping the silicon substrate with opposite polarity to the base. Diffusion is the most predominant technology employed for the solar cell's emitter formation, typically in diffusion furnaces. Fundamentally, there are 2 variants of diffusion furnaces – conveyor based inline tools and batch type tube furnaces. While the former has now completely vanished from the commercial space, tube-type furnaces are the unanimous choice for the application. Another technology shift that has taken place in this segment is that the traditional diffusion furnaces were typically operated at atmospheric pressure. However, to facilitate the formation of high sheet resistance emitters and reap the full benefits from the developments in metallization pastes, the industry moved to low-pressure diffusion, which assumed the role of the state of the art several years ago. French company Semco was the one that developed low pressure diffusion furnaces and eventually, along with the uptake of the technology, every equipment supplier started offering such low-pressure diffusion furnaces.
Since TOPCon technology is mainly adopted on n-type wafers, the emitter is formed through boron diffusion. It is not just a change of the precursor. Boron diffusion is often accomplished at a higher temperature – above 1,000 °C – and requires higher cycle times, resulting in lower throughput.
One interesting development with respect to boron diffusion furnaces is regarding the choice of the precursor. Boron tribromide was the most extensively used precursor in the past, but it has one inherent side effect: the byproduct of the process acts as a glue to quartz, which may reduce uptime. While equipment makers have significantly optimized the process, Semco switched to boron trichloride (BCl3) a long time ago as it believes that it delivers better results, as the presence of chlorine keeps the tube cleaner. It also helps in gettering. Boron trichloride is supplied in a gaseous form in bottles, eradicating the need for bubblers. BSG, with a chlorine-based precursor, is easy to remove compared to its counterpart. The flip side of using boron trichloride is its corrosive nature and the safety concerns associated with it. Nevertheless, it has now become the mainstream.
The most important developments in the emitter formation segment are related to TOPCon. Formation of high sheet resistance emitter is one topic of optimization in emitter formation, where 160 to 170 ohm/sq represents the typical range. In parallel, the leading TOPCon manufacturers have already started working on laser-based selective emitters. At a recent TaiyangNews conference, Wang Zhenhua, GM vacuum coating product line at leading laser tool supplier Hans PV, has presented the details of laser-based boron selective emitters for TOPCon cells, which is also a hot topic now (see Wang Zhenhua's presentation: Thermal Processes & Lasers in Solar Cell Production).
The process results in sheet resistance delta of 30 ohm/sq and a reflectivity change of above 1.5%. The tool uses 4 lasers and 8 stages in a single line to maintain a high throughput of 8,200 wafers per hour, referring the 132 lines per a M10 wafer.
The article is an excerpt from the TaiyangNews Market Survey on Solar Cell Production Equipment 2023, which also includes detailed product specs and can be downloaded for free here.