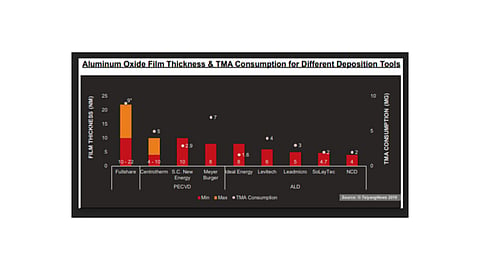
The two mainstream manufacturing technologies that are currently available for application of the rear passivation stack of PERC cells are ALD and PECVD. In fact, the method of deposition affects the thickness of the deposition. This in turn also determines the consumption of the precursor, TMA.
There is no set standard when it comes to film thickness. A common approach is to keep the aluminum oxide rather thin, while silicon nitride fills the gap to qualify for the minimum thickness requirement of about 100 to 120 µm for the rear passivation stack to safeguard the rear internal reflection. The required thickness of aluminum oxide does change according to the method of deposition, and it also varies from manufacturer to manufacturer.
Relatively thinner films deposited with ALD are sufficient to provide superior passivation compared to PECVD. In fact, deposition tool suppliers have been very successful in reducing film thickness. During the early days of aluminum oxide development, around 2008-09, a film thickness of 30 nm was common. Now, a single-digit film thickness is possible with nearly every system and technology.
The thickness also depends on the degree of rear polishing. The smoother the surface, the thinner the layer. Then, if aluminum oxide is also applied on both sides, the film has to be thin. Whether the processed cell is going to be bifacial or not also influences the film thickness. The industrial practice for film thickness is 5 to 10 nm with ALD and 15 to 20 nm with PECVD.
The film thickness also influences another important attribute of aluminum oxide deposition systems – the precursor TMA consumption, which is one of the key cost drivers in this process step. The precursor consumption not only depends on the thickness of the film, but also the reactor design and TMA utilization rate. The graph provides the spec for film thickness and corresponding TMA consumption given by suppliers of different deposition tools. On the other hand, TMA consumption has become less important as the precursor material has become way cheaper compared to the early days of PERC development.
For details on important aspects of PERC technology, check our TaiyangNews Report on High Efficiency Cell Technologies 2019, which can be downloaded for free.