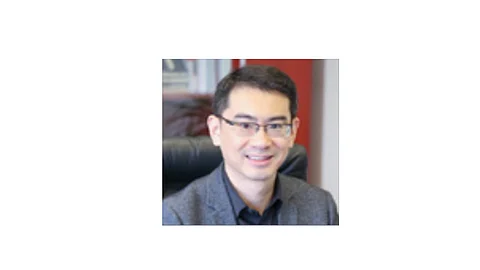
It took only 3 years for DKEM to become the leading Chinese metallization paste supplier to the PV industry and part of the world's top 5 players in this field. Although very new, DKEM doesn't want to win market shares through price, but primarly through quality – it's branding them is: "When Performance Matters." TaiyangNews talked to DKEM founder and CEO Dr. Weili Shi before SNEC 2018 about the start, evolution and plans of his company.
TaiyangNews: DKEM is a relative newcomer to the metallization paste segment.
Weili Shi: Yes, DKEM is relatively new to the metallization paste business. DKEM officially started operating in early 2013, but we saw significant growth from 2015. In the first 3 years we mainly did a lot of R&D work. Even though we are young, we are a very innovative start-up company and our brand and products are highly recognized in this market. And so far, we keep continuing to grow from our start.
TaiyangNews: What made you join the solar sector?
Weili Shi: Joining solar is related to my PhD study and working experience in the United States. At the early stage, I was working on research and development of sub-micro materials, and I have accumulated some experience in PV applications. At that time, the PV market was booming globally, and one of the key materials in photovoltaics was front-side silver paste, which was dominated by American and European companies. As we knew that cost-reduction is very important for continuous growth of the PV industry, I identified the strong need for a local supplier to provide cost effective products. So combining my background and experience in R&D as well as judgement of this industry, we decided to get involved in the silver paste supply business of the PV sector.
TaiyangNews: Can you share any experience on how you started?
Weili Shi: We set up a R&D lab with some difficulties at DKEM. For the first two years – 2013 and 2014, even early 2015, we did a lot of research in the lab. When the samples were ready, I took it to the customers and joined online testing to validate and improve our product step by step. Getting the first customers was really difficult. We started with tier 3 customers, who are small and are looking for cost effective materials. They have been supporting us a lot from then on. We started testing with the small customers and then gradually moved to tier 2 customers.
TaiyangNews: Talking about markets, how do you see demand for pastes at the moment?
Weili Shi: As for global market demand in 2018, the numbers we received from different sources are relatively conservative. But until now, our customers' capacity utilization is still in good condition. It rather looks like paste demand will be strong for the following quarters, especially from some of our strategic partners, whose new high efficiency capacities are starting soon. This is another good news for us.
TaiyangNews: Q1 was surprisingly strong in China, but some market participants say that Q2 is not so strong. Do you see that a well?
Weili Shi: The market in China is pretty good. This is my impression based on the operation of our customers. And we are optimistic about the market for the rest of the year. One reason is that the installed capacity is still large, and for us as DKEM, we are happy to see that the market technology roadmap is moving towards the products where we have stronger competencies. Since we are still a new player in PV, there is plenty of rooms for us to explore and to co-operate with more customers.
TaiyangNews: And how is competition these days?
Weili Shi: In the solar market competition is always fierce and there is always a high price pressure. However, we see different competition levels. The multi sector is more cost-driven, while mono and PERC is more performance- driven.
TaiyangNews: The paste segment was once ruled by a handful of companies. How were you able to enter that group?
Weili Shi: Let's first talk about Chinese paste manufacturing. It has been a rough road for Chinese pastes makers, especially for those active in front silver paste. The most difficult step is the first – and that's to win customers' trust. This is more difficult for a local company, especially a start-up like DKEM, compared to leading foreign suppliers, since we started from zero. But this was also a great opportunity for us to prove ourselves, because all trust and partnerships are based on stable, reliable and high efficiency products. After we established this strong base, we have continuously shown our R&D capability and adaptability with fast development activities with tier 1 customers addressing their specific needs such as DWS, black silicon and PERC technology. We stand firm on each step and have faster response than our competitors. This is how we entered the tier 1 customers and also why we are now recognized by our customers.
TaiyangNews: What are the advantages of being a local supplier in China?
Weili Shi: In the early stages, Chinese suppliers were very much focused on cost and price advantages. For DKEM, our target and focus are to provide more cost- effective products with great performance, because we could offer even higher efficiency products than foreign suppliers. Besides, fast response to customers we do have another weapon at our disposal. We could provide product improvement and on-site support within 3 days. Another major benefit for customers who adopt local silver pastes could improve their cash flow because of low inventory.
In fact, some well-organized customers not even need inventory. This helps them to better manage their cash flow.
TaiyangNews: You said you can provide higher efficiency products. If you look at the large competitors, they are not only bigger in pastes, but they have even material business in several fields and large R&D teams. So what's your secret?
Weili Shi: It was not simple and involved a lot of hard work. We have a relatively small R&D team, but what we can offer is faster turnaround times based on an efficient and focused organization for decision-making. We respond faster to the customer's requirements. The PV industry is very dynamic, thus suppliers have to be quick. We have to catch the voice of the customers very quickly and need to improve or upgrade the products quickly. The western companies are maybe upgrading their products quarterly or monthly, while we can improve products within a 3 days cycle, soon stabilize it and support fast transfer into mass production.
TaiyangNews: Are you working alone or cooperating with institutes or universities?
Weili Shi: Mostly we work in house but collaborate with customers a lot.
TaiyangNews: What is your current market share in China and globally?
Weili Shi: It's difficult to clearly define the exact market share since PV is a very dynamic industry. Based on surveys from customers and research firms, we are now the leading brand of Chinese local suppliers and also a very competitive tier 1 supplier globally.
TaiyangNews: What are your growth plans for the coming years?
Weili Shi: We hope to become one of the top 3 suppliers globally in the next 3 years. Although we have been growing fast so far, we still have some gap compared to the leading suppliers and need to put more efforts on this part.
TaiyangNews: What's the business strategy to get there beyond being more responsive than the competition?
Weili Shi: Frankly speaking, it's a real big challenge to achieve this target, but we are willing to accept and face
it. Continuous investment on research and development is necessary, including recruiting more talent and allocating more facilities. We also plan for next generation metallization technology, have to be aggressive and spontaneous in order to continue to change and innovate. Besides, we closely collaborate with our customers and equipment vendors for developing more demand for metallization projects and technology. We have to make the team growth faster than our market shares will grow, and even more importantly, we need to keep strengthening and upgrading our business system.
TaiyangNews: What have been the major challenges for you to establish your brand?
Weili Shi: Branding is a complex system that reflects the capabilities of a company in the market. To establish a good brand requires a clear strategy, including product and pricing strategy, and also stable quality support. We have a clear product positioning – providing more cost-effective products with great performance to compete with foreign suppliers. Though we are new players in this dynamic and competitive market, we have positioned ourselves as suppliers of high-performance products from the very beginning. We have mastered a lot of challenges during this developing process, but also due to this clear strategy we could keep improving toward to the right direction. Our high efficiency, stable and reliable products also echo our branding image – "When Performance Matters."
TaiyangNews: Tier 2 and tier 3 cell suppliers are completely dominated by Chinese pastes suppliers while the tier 1 group is usually a hard nut to crack. How were you able to enter into the tier 1 supply chain?
Weili Shi: China paste suppliers have grown significantly in the past 2 to 3 years. Currently, tier 2 and 3 customers are mainly dominated by DKEM and other Chinese suppliers. But from my point of view, we should treat all customers with the same positive and aggressive attitude.
Since what we have today is based on collaboration and trust with tier 2 and 3 customers at the early stage, we are sincerely thankful for this support to help us win new opportunities to also work with tier 1 customers. Tier 1 customers are most concerned about stable product quality. So from our past learning experience, we have quickly caught up with their needs by well controlling quality from raw materials to final products. In addition, there is our continuous innovation capability. These are the keys we could enter the tier 1 supply chain.
TaiyangNews: In general, what is the price advantage of your products compared to that of the leading brands?
Weili Shi: Front silver paste is always a technology-driven product, so it's not fair to judge on "price". We think that more cost advantage could be achieved by technology innovation – this is what we are more concerned about than the price fight. Compared to other leading brands in this market, our commitment is to provide quality products with higher efficiency and more competitive price. To be specific price is not the determination for factor. For example, in some formulations we are more expensive than competitors, while we also have more cost effective pastes. This really depends on the technology of the cell maker and the main application stream.
TaiyangNews: PERC technology is important to you. Why?
Weili Shi: The advantages of PERC technology are clear and could be the key factors for us to enter the "grid parity stage." PERC technology is our strategic focus from 2017. We have realized it in our new product DK92 series. From the viewpoint of business and market growth, PERC technology is definitely the key for our continuous growth. This is about DKEM's technology advantages.
TaiyangNews: Could you please explain your product portfolio for PERC?
Weili Shi: So far all of our front silver product designs are based on PERC requirements, which is also compatible with conventional BSF cells. Currently, our product portfolio for PERC cells are DK92A for PERC/black silicon cells, which is also compatible with DWS black silicon BSF cells. DK92B is for mono PERC and mono BSF cells. Meanwhile, we were the first to come up with a paste suitable for double-sided aluminum oxide passivation PERC cells. The product is called DK92K, was introduced in October 2017, and was the only one of its kind back then.
TaiyangNews: What are the main aspects you are trying to address with your pastes for PERC application?
Weili Shi: The PERC cell structure has bigger challenges than the conventional BSF structure, so it requires a more differentiated design for its corresponding front silver pastes. For instance, a wider firing window at lower peak temperature is needed while maintaining stable adhesion performance. But so far these understandings are not enough to figure out all questions, especially on the low- temperature firing aspect. It will have big impacts on how to solve LID and thin-wafer application. Although the LID issue could partially be solved by post-treatment, it also showed some side effects, which is hard to estimate regarding impacts on cell performance. Moreover, we found that different pastes designs show a corresponding degree on the side effects. This may be helpful for us to solve the issues of PERC technology in field applications.
TaiyangNews: Can you provide the key characteristics of your new pastes that can establish contacts on double sided aluminum oxide passivation film?
Weili Shi: As the leading solution provider on double- sided aluminum oxide passivation PERC technology, we break through the contact limitation between FS silver and the SiNx/AlOx stacked layer with innovative recipe design through collaboration with tier 1 customers and equipment makers. Right now, we are leading in identifying the key characteristics of this passivation technology in the front- side silver sector. Our product design has enlarged the benefits of passivation effect of the AlOx/SiNx stack, since we could provide better Voc while maintaining good contact performance. This is the most direct benefit of our new paste. Meanwhile, we achieve more significant benefits if we combine lower firing temperatures.
TaiyangNews: What is the reason for creating a double sided aluminum oxide passivation layer? What is the benefit?
Weili Shi: Based on our understanding, the main driving force is cost. The machine to deposit passivation film in this configuration has a very good cost performance and throughput. Going to the technology part, in the early stages we see the mismatch between aluminum oxide and the n+ surface. However, there is a thin silicon oxide layer between emitter and aluminum oxide to overcome the mismatch. Besides, you can also put aluminum oxide on top of silicon nitride. Regarding to the enhanced passivation effect of the SiNx/AlOx stack, we are collaborating with customers and equipment makers to explore more. We also see the extendibility of this kind of technology to front-side passivation of n-PERT cells.
TaiyangNews: How many cell makers are moving in this direction?
Weili Shi: More and more. Some tier 1 as well as tier 2 customers.
TaiyangNews: What are the other advanced cell technologies you are focusing on?
Weili Shi: We would like to categorize the advanced cell technologies by operating temperature. At mid to high firing temperature, our focus are PERC and n-PERT plus TOPCON, and for low curing temperatures, we focus more on heterojunction and its derivative technologies. "Operating temperature" is the important index for metallization.
TaiyangNews: What is the cell technologies that will have the greatest impact in the coming years?
Weili Shi: Taking about beyond PERC, we see some good signs in the direction of TOPCON. As you can see in the news, there was a big announcement from Jolywood about activities in n-PERT and TOPCON. They will deliver about 5 GW modules based on this technology in the next coming years. In the short term, TOPCON will be the focus for R&D in the PV industry and its commercialization will depend on its achievements regarding strong performance compared to bifacial p-PERC cells, but in the long term, industry may pay more attention to heterojunction. In summary, advanced passivation technology is the persistent pursuit for cell technology.
TaiyangNews: What is the major difference with TOPCON technology from the paste perspective?
Weili Shi: The challenge is the process window for the metallization part. Every variation during the firing step may damage the polysilicon passivation layer. That means, in manufacturing you need lower firing temperature – much lower than PERC. That is why the operating temperature is the key index for metallization of advanced cell technologies.
TaiyangNews: Talking about silver – how important is silver reduction these days?
Weili Shi: Silver reduction is indeed what cell makers are currently focusing on. Currently, it is realized by fine- line printing on cells and new interconnection of module technology. We are also working with customers on silver reduction through special innovative concepts, but we have to emphasize that long-term reliability is always
the first priority for PV products. Too aggressive silver reduction may have certain impacts and concerns on module reliability.
TaiyangNews: You do not seem to agree with the ITRPV's silver reduction roadmap. What do think is missing in their projection?
Weili Shi: It's not exactly we disagreed with the ITRPV's silver reduction roadmap, we just look at it from a different angle. ITRPV took it more from technology innovation, while we are looking more from market demand and practical mass production. There is always some time gap from technology innovation to mass production, and this is probably the main reason that we have some disagreement on this topic. For example, ITRPV had more aggressive predictions on multi-busbar market demand in the past few years, but indeed there was a gap between actual usage and the predicted laydown roadmap. We are happy to see that MBB is now finally moving to the mass production stage, which will bring ITRPV's predictions closer to industry practice.
TaiyangNews: What are the most important trends in metallization?
Weili Shi: We are very clear about metallization development trends and what is needed for further improvement. The most important trends are a better aspect ratio, better frit contact to fit in higher wafer sheet resistance, better low-temperature firing capability, and reliable adhesion performance. Besides, another trend is demand on high-speed printing production, and clearly address the importance of paste printability.
TaiyangNews: What is the advanced metallization concept you believe will have the greatest impact in the near future?
Weili Shi: We are strongly promoting an innovative metallization concept based on integrated thinking and collaborative innovation of advanced cell and module technologies, which will have a big impact on the whole PV industry. Affected by the concept of interconnection technology, the boundaries between cell metallization and module interconnection are becoming fuzzy. Independent development on metallization of cells or modules will no longer be suitable for future product development. We have made good progress and collaboration with tier 1 customers, and we believed this will be the trend for further PV developments.
TaiyangNews: If you look at advanced printing concepts and advanced screen concepts, what trends do you see?
Weili Shi: We believe that for multicrystalline DWS wafers with black silicon knotless and high mesh will be the trend; for mono, high mesh based conventional screen design will dominate and we will keep monitoring the progress of continuously upgraded knotless technology on mono surface. As for printing approaches, for PERC double printing will remain key for few cell makers; but for multi cells, if customers use 4 printers, they will prefer dual printing.
TaiyangNews: What are the most important methods in your view that can contribute to metallization costs reduction?
Weili Shi: We strongly believe that silver continues to be the key material in PV metallization for a certain amount of time. Along this line, we need contribution from screen technology and silver paste innovation to realize ultra fineline printing. Meanwhile, low-temperature curing paste combined with stencil printing is another potential opportunity. Currently some of the cell makers have shifted their focus on dual-printing to lower the metallization cost, and from the module development viewpoint, 6BB and MBB are also effective for lowering laydown control.
TaiyangNews: Are we not touching the limits in terms of finger width reduction? Do you seen any new technologies on the horizon to go further down?
Weili Shi: Honestly speaking, we have not yet reached the finger width limit so far, and that's what we are working on very hard. Based on the current screen technology, we still have room to further improve finger width from the paste viewpoint. For a long-term plan, we would still need the support and improvement from screens, printers and other types of metallization systems to achieve the finger width limit. There are new types of technologies that are evaluated right now, but I would say it would be hard to compete with the advantages of current screen-printing metallization method in a short time.
TaiyangNews: So where do you see the finger width in 5 years?
Weili Shi: Many things could change in the PV industry in 5 years. From our discussion and collaboration with screen vendors, it's highly possible to achieve fired finger width at nearly 30 μm when using some new solutions, but we still need to confirm the stability in production.
TaiyangNews: And what about the paste laydown potential?
Weili Shi: Based on our internal studies and results from collaboration with our customers, it's highly possible to realize 60 to 70 mg laydown within 5 years, which will require the support of MBB and module developments.
TaiyangNews: You belong now to the leading group of paste suppliers to the PV industry – how do you want to stay in the top group?
Weili Shi: Front-side silver conductive paste will always be a competitive business in the PV industry. It was dominated by European and American companies at the early stage, and it is now even more competitive with the rise of Chinese local vendors. No matter what has changed, the front silver business is always driven by technology and product performance. The dynamic leadership position of the top players is the direct reflection of their periodical technology and product advantage.
I mentioned it before, but in summary this could echo our branding image, "When Performance Matters." What the new leading comers in the metallization field, like DKEM, have to do first is to stand firm with a "quick response" to market demand and customer requirement. Based on this, continuous collaboration with customers is important to innovate and grow together to help us meet the mid- to long-term roadmap. Besides, to new players like us, we need to pay more efforts on self-growth and organization development.
TaiyangNews: Thank you for the interview.
The interview was originally published in the TaiyangNews PERC Solar Cell Technology Report 2018, which can be downloaded for free here.