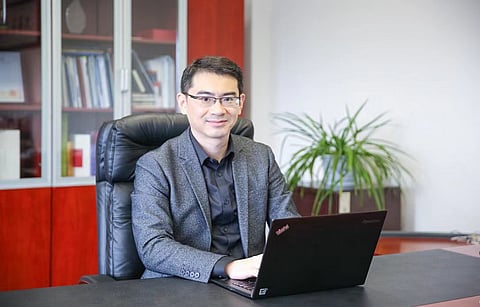
Metallization is a crucial process that affects both the cost and performance of solar cells. This step is particularly significant in the case of TOPCon, where the cell architecture necessitates silver pastes on both sides, resulting in almost twice the amount of consumption compared to PERC. Therefore, finding ways to reduce the usage of silver pastes is essential in cutting down the costs of TOPCon. In light of recent developments in the silver pastes segment related to TOPCon, TaiyangNews had the pleasure of speaking with Weili Shi, the Chairman of the Board and CEO of DKEM, a leading paste supplier, to gain insights on this topic Weili Shi is the chairman of the board & CEO of DKEM. As an electronic materials scientist, he founded the company in 2010 and led the company to rapidly grow into a global leading supplier and the first listed Chinese company in the silver paste sector. Now Dr. Shi and his team are driving the transformation of solar cell technology from p-type PERC to n-type TOPCon with integrated metallization paste solutions.
TaiyangNews: To reflect on the metallization market, how is the paste business in general?
Weili Shi: In 2023, we see very strong demand for silver paste, driven by more than 350 GW of PV installations globally and the rapid transition from p-type PERC to n-type TOPCon, which is exceeding expectations. DKEM delivered a very strong performance in 2022 with 46% shipment growth in shipments and 130% shipment growth in Q1 2023, and we foresee even stronger results in the coming quarters.
TaiyangNews: What is your market share in the paste segment?
Weili Shi: DKEM is a global leading supplier of photovoltaic metallization pastes. We are among the Top 3 in the p-PERC silver paste sector, and we are leading the wave in TOPCon with more than 50% market share in the n-TOPCon silver paste sector right now.
TaiyangNews: What are the most important trends in the metallization segment?
Weili Shi: The most obvious trend is fine-line printing. With the improvements in screen technology and silver paste, most high-temperature firing silver pastes can print with 10-15 μm finger openings, which significantly increases solar cell efficiency and reduces silver consumption. The other one is that contact performance becomes more and more important with the continuous efforts on high sheet resistance emitter, regardless of p-PERC or n-TOPCon, and with ever lowering silver consumption. In parallel, silver pastes need to help customers improve module reliability with different encapsulating materials.
TaiyangNews: As this report's focus is on TOPCon production, what is the status of the metallization solutions for TOPCon?
Weili Shi: Metallization pastes are playing a critical role in the success of TOPCon solar cells. We started to develop n-type silver pastes back in 2017, and to develop TOPCon-specific silver pastes with JinkoSolar back in 2019. Right now, we are offering an integrated metallization solution to TOPCon cell makers at a mass production scale, including the DK71A silver/aluminum paste to contact the front-side boron-doped emitter, the DK93T silver paste to contact the rear-side phosphorousdoped Poly-Si layer, and the DK81A floating busbar paste for both the front-/rear-sides.
TaiyangNews: Unlike PERC, TOPCon has silver paste on both sides. What are the main differences with the paste system for TOPCon?
Weili Shi: The n-type silicon base and bifacial characteristic make the difference for TOPCon metallization pastes. For p-PERC, silver paste is designed to fire through SiNx ARC layer to contact the phosphorous-doped silicon emitter. However, the conventional silver paste cannot make ohmic contact with the TOPCon front-side boron-doped silicon emitter. So an all-new silver paste is needed which has a very small amount of aluminum incorporated to help reduce the contact resistivity to the boron-doped emitter. For TOPCon rear-side metallization, the phosphorousdoped Poly-Si layer is much easier to be damaged than phosphorous-doped crystalline silicon during firing. The glass frits system of the silver paste, based on deep understanding from p-PERC silver pastes, needs to be tailored into a proper window to achieve good contact while preserving the passivation quality of the TOPCon.
TaiyangNews: Which paste is more crucial for TOPCon – front or rear?
Weili Shi: From an efficiency perspective, I have to say the front-side silver/aluminum paste is more crucial. Whereas, the rear-side silver paste is more critical from a cost and yield perspective. That's because rearside silver consumption is higher with the current finger openings and pattern designs. However, further reducing the silver paste laydown at the rear-side can be rather sensitive to the contact window and overall EL yield.
TaiyangNews: What is the mainstream printing technology for TOPCon – fine-line, dual or double printing?
Weili Shi: Almost all TOPCon customers are using dual printing for both the front-side and rear-side. Fine-line is definitely the focus for the purposes of higher efficiency and lower silver consumption.
TaiyangNews: Now the industry is talking about implementing the selective emitter on TOPCon; does this make your job easy?
Weili Shi: Selective emitter is not just in talks; it is already the reality. The leading TOPCon cell makers have already upgraded or are upgrading their production lines to selective emitter. As to the newcomers, selective emitter has become the benchmark process for the frontside boron emitter. Indeed, selective emitter affects metallization a lot. However, we have to realize that the selective boron emitter is quite different from p-PERC's selective phosphorous emitter. The boron concentration at the laser treated region is actually lower than the conventional process, but with a deeper junction. Thus, formation of contacts, which is typically impacted by the surface concentration,remains challenging or becomes even more challenging in this case. The paste system has to be optimized to take advantage of deeper junction at laser treated region to achieve better contact and lower recombination.
TaiyangNews: Are you offering any special pastes for selective emitter-based TOPCon cell structures?
Weili Shi: As the leading metallization paste supplier for TOPCon solar cells, we are offering the upgraded DK71A silver/aluminum paste for the selective emitter process, achieving even lower passivation damage to the sensitive laser-treated area without compromising contact performance or with even stronger contact capability. We actually started working closely with the leading players to develop such a paste in 2022. We have already demonstrated >0.3% higher efficiency based on the selective emitter process supported by the upgraded DK71A paste and fine-line printing. We are actually expecting even higher efficiency benefits in the coming months.
TaiyangNews: What is the finger screen opening and corresponding finger width on the front and rear with TOPCon?
Weili Shi: Right now, the mainstream finger opening is ≤15 μm and ≤20 μm for the front- and rear-side respectively, with the corresponding fired finger width at ≤25um and around 30-35um, respectively.
TaiyangNews: What is the silver paste consumption on the front and rear side of TOPCon cell in mass production?
Weili Shi: As to the leading TOPCon cell makers with M10 wafer size, the front-side finger laydown is <40mg, the rear-side finger laydown is < 45mg, with about 8mg busbar paste laydown on each side.
TaiyangNews: Pastes are the key enablers for increasing efficiency as well as reducing costs; can you please talk about the avenues for TOPCon pastes to improve efficiency and reduce costs?
Weili Shi: With the industrialization of TOPCon solar cells, the supply chain sees more value in the crucial role that metallization pastes play in increasing efficiency and reducing cost. Regarding the front-side metallization, we need to focus on significantly reducing the J0,mteal and contact resistivity, and enabling 10 to13 μm fine-line printing by organic modification – to be comparable to the fine-line capability of p-PERC silver paste, and further lowering of gridline resistivity. Regarding the rear-side metallization, we need to design new glass chemistry to advance <100 nm Poly-Si adoption, and to further improve contact performance to enable even lower laydown by < 15um fine-line printing.
TaiyangNews: When we talk to the deposition tool vendors, they often point out that the reduction in the poly film thickness is dependent on the paste, which in turn governs several other factors; what is the typical poly film thickness that your paste product can support right now?
Weili Shi: In general, 110 to120 nm Poly-Si thickness is applied in the current phase of TOPCon industrialization. We all see the advantages of the thinner Poly-Si layer, like higher production capacity, lower parasitic absorption loss and better bifaciality, etc. But we have to understand that the thinner Poly-Si layer needs other improvements further enhance or maintain passivation quality. Here approaches to make the surface flatter and protecting the doped region of polysilicon and tunneling oxide from any damages becomes more critical. Actually, it's quite challenging for the metallization paste to contact < 100 nm Poly-Si layer, as such a thin polysilicon film is more prone to severe microstructure damage during the cofiring process to form rear-side electrodes. But it's still possible for <100nm Poly-Si design by developing new glass chemistry and/or using barrier layer at rear-side ARC layer. As to DKEM, our customized DK93T silver paste has successfully demonstrated the feasibility of <100nm PolySi layer in mass production scale at one leading cell maker. As far as I know, DK93T is the first ever silver paste to achieve this at a mass production level. We are making more efforts to advance <80nm Poly-Si layer in the long term.
TaiyangNews: What kind of paste solutions can be expected from DKEM for TOPCon in the near future?
Weili Shi: We are rigorously upgrading our TOPCon pastes to further enhance our leadership position in TOPCon metallization. In the coming SNEC show, we will launch the new version of DK71A silver/aluminum paste focusing on selective boron emitter with more balanced contact and recombination design, plus ultrafine- line printing supporting ≤13um fingers to further reduce shading and recombination, and the new version of DK93T silver paste compatible with LPCVD process involving two wafer per slot configuration to significantly improve the manufacturing capacity with featured ≤15um fine-line printing. Also, we will have an all-new DK93TL low-solids rear-side silver paste to further reduce metallization cost of TOPCon solar cells.
TaiyangNews: Thank you for the interview.
The interview is an excerpt of TaiyangNews' Cell Production Equipment Survey 2023, which is available for free download here.