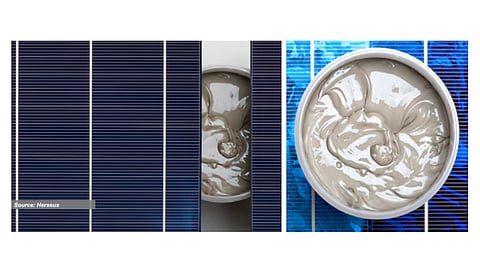
Metallization pastes have been always playing a vital role in improving a solar cell's performance as well as its cost structure. However, its significance has been increasing even more after PV manufacturers have left the decade old back-surface field cell structure behind. Moving to PERC has brought new innovations, which is even more important for high efficiency cell concepts that require very special paste systems.
5/31 – the date in 2018 when the Chinese government announced a restructuring of the solar sector – was a watershed also for the paste segment that was one of the few in the solar value chain offering very high margins until that point. But the sudden demand shock led to dramatic price pressure, which emerging Chinese paste manufacturers were able to use in order to capture market shares from the incumbents from Germany, US, Korea and from the region of Taiwan. These developments led the latest western metallization paste market leader Heraeus from Germany to close down its solar operations at home and fully consolidate in China to stay cost competitive. Today, Chinese paste manufacturers are competing head to head with the top companies of the former incumbents also on product performance and quality – and are supplying their products to several Tier 1 cell manufacturers.
The cell manufacturers' strong interest in developing high efficiency products is creating plenty of space for technically advanced metallization solutions. Whoever offers the best solution will get the order – it is about the ratio of price and performance, with the latter now having more weight.
With PERC becoming the new standard solar cell technology, paste suppliers' focus also shifted to PERC and its variants. As for PERC's dominant variant – monocrystalline, cell manufacturers are increasingly opting for selective emitters. For paste suppliers that means developing a paste formulation suitable for every emitter (selective) profile realized by its different cell making customers. On the other hand, there is multicrystalline silicon cell technology, even though its share is decreasing compared to the total. Multicrystalline wafers – now all basically sawn with diamond wire technology and treated with superior black silicon texturing – are also mostly processed into PERC cells and have special needs when it comes to metallization. Such pastes not only have to deal with a fairly different surface, but also have to be compatible with different doping profile – typically high – compared to pastes used for monocrystalline substrates.
Although its bifaciality is not very high, making a PERC cell bifacial to increase yield even only somewhat makes a lot of sense. The increasing bifacial PERC capacities being produced need a local BSF in the form of fingers instead of the traditional full area metallization coverage. This development alone has decreased paste consumption to 200 to 300 mg from 800 mg from the full area PERC cell. Such pastes for fingers on the rear are generally not capable for fire-through processing, which means the rear passivation stack needs to be opened physically with lasers, but fire- through variants are under development, eliminating the need of lasers. Toyo is already offering such fire- through aluminum pastes.
As PERC is expected to reach its efficiency limits soon, cell companies are looking into higher- efficient n-type cell architectures. The leading paste companies are all working on n-type product solutions, for which aluminum-doped silver pastes are used on the front side and silver composites for rear contact. However, aluminum pastes are now promoted for contacting the p-type front surface of n-type cell structures.
Passivated contacts (often called TOPCon) implemented on n-type cell architectures is another emerging hot technology variant that is providing opportunities for paste manufacturers to develop suitable products. The technology requires a paste system that can support a low firing temperature window – lower than required by PERC.
Finally, there is heterojunction, the most efficient of the emerging high-efficiency cell variants, that needs
the lowest temperature processing. Here, the contact pastes are not fired, but cured. While only few cell manufacturers have decided to invest in mass production of promising HJT so far, it is impressive by how much paste suppliers were able to improve their products – today an HJT cell needs only less than 400 mg and as little as 60 mg with busbar-less Smart Wire technology, compared to 1,000 mg few years ago.
In general, paste manufacturers have made significant progress in several areas of their special polymer silver composite products, such as ease of operation by improving the storage conditions and eliminated the limitation of one time use, lower processing time, increased printing speed up to 250 to 300 mm/s and improved conductivity by reducing the bulk resistivity down to 4 to 4.5 μΩ.– all features that contributing to cost reduction in cell processing.
There is still some room for improvement and a lot of work in progress.
Irrespective of cell technology, paste manufacturers are focusing on two topics – improving aspect ratio and reducing paste laydown.
In addition to improving paste formulations that helps in building finger height, dual printing coupled with knotless screen or stencil as well as double printing enables improving finger height. Reducing the finger width by printing through narrow screen openings is the key path to reduce paste consumption.
Knotless screens and low mesh screens are helping to attain low finger width and better printing quality.
The screen technologies are getting segmented as of now; knotless screens are widely used for multicrystalline, while monocrystalline PERC cell processing, especially with selective emitter, is mainly employing high mesh screens. However, the recent developments in knotless screens may spread their application to monocrystalline substrates as well. Another interesting development in the field of screens is polyimide-based screens that supports laser opening, thereby enabling ultra- narrow openings of less than 20 μm.
Finger opening down to 20 μm are already in use with knotless screens and about 26 μm with high mesh screens. These levels are already touching the limits; the scope for further aggressive reduction is rather limited and might require new screen technologies – that's why there is the huge interest int polyimide-based screens.
While material optimization is one part to cut cost, the other complementary part is the production machines. The advanced technologies haven't changed – it is still double and dual printing process solutions, which require one more printer each. However, both have only a combined market share of about 30% despite their advantages. Dual printing (where fingers and busbars are printed separately) can considerably reduce paste consumption, especially with a higher number of busbars, which is why more and more cell manufacturers are showing interest in it. On the other hand, advanced module technologies such as shingling require a uniform finger cross-section – and that speaks in favor of double printing (a print on print solution). That means, the more advanced cell/module technologies we see, the more advanced printing solutions will be used.
However, at some point all methods to further reduce silver and paste consumption will be exploited. While not on the agenda for a while, a recent upward trend for silver prices (suddenly interrupted by the Coronavirus) could bring at a certain point something back in the limelight that was once considered an alternative to silver pastes and screen printing but never made it into a mass production technology – and that is plating. Again, it's not there yet – but we have talked to one proponent of this technology, RENA, to better understand how plating has developed over recent years (see interview p. 46).
This article is the conclusions part of our Metallization Pastes Market Survey 2019/20, which was released in March 2020 and can be downloaded for free here.