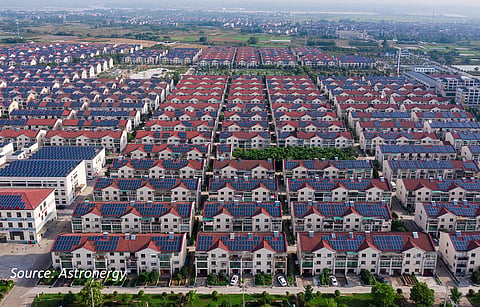
When it comes to PV modules, the solar industry has made quite some progress over the past year — and it continues the highly dynamic trend we have seen over the last 3 years as it strives to reduce costs, a result of higher cell and module efficiencies.
For many years, it was mostly higher cell efficiencies that drove module efficiencies. That changed with the PERC cell technology's arrival in and around 2015, which took over the industry almost in a coup and quickly established itself to become the new cell standard used in almost all solar modules by 2019. The move to PERC required little investment in new technology — just a few additional machines are all that's needed. The same cannot be said about the next step up to higher efficient solar cell technologies. To start with, a cell technology choice must be made. TOPCon is one of the two choices, which builds on PERC production equipment. The other is HJT, which means a completely different manufacturing design setup, and much higher investment. Given this dilemma, even as PERC cell optimization was limited, companies have shied away as long as possible from choosing one, instead doing everything they can to improve module design while also looking much deeper into the wafering technology.
The mission to quickly increase the wafer size had increased module power as its primary target, reducing BOS costs in turn. This goal has been very well achieved. The industry and the entire value chain seem to have bought into the larger wafer concept. M10/G12 wafers are the most dominant now, and expected to replace all other formats in the near future. According to our research, a G12 based 700 W TOPCon module from Jolywood is the top module among those commercially available. Among the M10-based products, JinkoSolar's TOPCon module with a rated power of 615 W claims the top spot.
On the module technologies front, being the key technology enablers of larger wafers, MBB and half cell have almost become the baseline design. Bifacial technology, given that it costs the same at the cell level, especially with PERC, has also become an important partner in the technology mix. Zero-gap is perhaps one technology that is yet to be explored to its full potential. Shingling triggered a lot of interest and several companies have also developed indigenous technologies; however, with the IP backing this technology owned by two companies, it remains to be seen to what extent it can be applied by others. Tiling Ribbon, a technology that has been commercialized by JinkoSolar, is a nice legitimate workaround for shingling in the zero-gap space. Many companies, however, are taking a rather progressive approach where they are reducing the cell spacing instead of eliminating the gap completely. While 2 mm has been the cell spacing traditionally, companies are now settling at different levels ranging from 0.6 to 0.9 mm.
With more technologies being blended into one product, categorization of modules based on technologies is becoming obsolete. What is still valid and increasingly becoming apparent is that the application of a module is what dictates its design. There is now a clear differentiation between the products offered for residential, C&I and utility. While larger and very high power modules, increasingly bifacial, are preferred for utility-scale projects, higher power from a smaller area and lighter weight are the requisites for residential. Aesthetic considerations, even at a slight cost of performance and higher price, are becoming important here. C&I, being an intermediate segment, covers the tail of utility and the top of residential. Some of the product specs we have received indicate that companies are offering their modules under blended application labels such as Utility and C&I and Residential and C&I.
We find PV being increasingly integrated into other applications. BIPV, floating PV, VIPV and Agri-PV are a few examples where module makers have started to put some serious focus. While only few products have been successfully commercialized for these applications, many companies are working on these. What's interesting is that the first of the world's leading module manufacturers are now seriously developing BIPV products, a hopeful sign that the huge dormant potential of this segment is finally being activated.
With so many developments taking place already, what's next? The focus of vertically integrated module manufacturers returns to basics — cell technologies.
A fact check: last year's report included modules with efficiencies above 21% — and 21 products belonging to different technology streams met this criterion. Maintaining the same benchmark for this edition would have, in our opinion, overcrowded this report. So, we set the minimum threshold at 21.5% this year, and include only the commercially available products. Still, a total of 17 products from 16 different companies made it to our list from the hundreds of products we scanned. Zooming in, we see that, unlike last year when high-efficiency cell technology was not a prerequisite to be part of the top group, this higher benchmark brings the cell technology front and center. It's also becoming evident that PERC has lost steam, no longer being able to support efficiencies above 21.6% (with one exception at 21.7%). As we can see in this report, most of the top-efficiency-rated modules — i.e., 21.8% upwards — are based on high efficiency cell architectures such as TOPCon, HJT or IBC. The highest commercial module efficiency now reaches 22.8%, which is linked to a high-efficiency back-contact silicon solar cell, and is slightly higher than last year.
Overall, we can also see more module products based on higher efficiency cell technologies have entered the market, and there will soon be many more. In this context, a primary goal would be to cost effectively scale up advanced cell architectures to larger wafers, while solar module products are further segmented and specialized to address the markets' needs. In other words, the highly dynamic phase in the solar module segment will continue.
This is the updated conclusion part from TaiyangNews report on Solar Module Innovations 2022, which is available for free download here