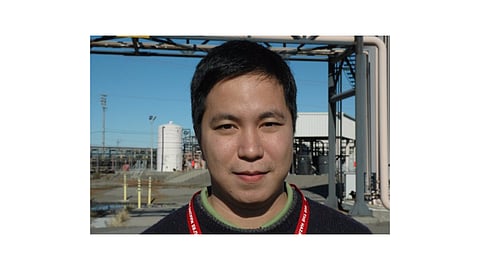
About LONGi
LONGi is the world's largest mono wafer manufacturer. At the end of 2016, LONGi had 7.5 GW mono ingot/wafer capacity, 2.5 GW mono cell capacity and 5 GW module capacity, which it plans to expand to 12 GW ingots/wafers, 5 GW cells and 6.5 GW modules by the end of 2017. By 2019, LONGi wants to increase its ingot/wafer capacities to 25 GW. The current production facilities are in China and Malaysia. LONGI is also active in solar power plants, targeting 800 to 900 MW in 2017. In 2018, a LONGI-Tongwei JV plans to bring online the first phase (25,000 tons) of a poly plant in Yunnan Province, China, which is targeted to have a full capacity of 50,000 metric tons. LONGI is a global leader in solar technology development - it "reinvests about 7 to 8% of our revenue into R&D, which is unmatched by any of our peers," said Archie Flores, LONGi Solar's VP for Corporate Strategy and GM of LONGi Solar US in the interview with TaiyangNews.
TaiyangNews: When looking at LONGi's strategy of pushing high-efficiency solutions, how does bifacial technology fit into the equation?
Archie Flores: Before I get into bifacial or our company's technology differentiation, I would like to highlight LONGi's core business, which is mono wafers. Our solid position in the solar wafer market serves as the anchor to our downstream integration efforts which occurs through strategic partnerships, channel acquisitions and also through organic and inorganic technology advancements. We are always on the lookout for the leading-edge approaches which we can implement in large-scale manufacturing. Bifacial modules may not be a mainstream industry product for now, but at LONGi we have already brought on meaningful capacity. We have a 300 MW bifacial production line in China and output so far is fully allocated. We will scale it up as the market allows.
TaiyangNews: How important is it for LONGI to go bifacial?
Archie Flores: We have a comprehensive technology approach. We always look at technology as the driving force towards an ever improving levelized cost of electricity for solar. The business focus for most industry participants have been on project cost or its gross margin. We improve gross margins by lowering modules and BOS costs, but we can also improve margins by increasing project revenues.
At this point, we have to shift our thinking from a "per-watt" cost basis towards a "dollar-per-kWh" mentality. Many technical people have talked about better energy yield through improvements in NOCT, temperature coefficients and degradation. But improved energy yield from the same nameplate capacity could also be realized through trackers and bifacial technology. LONGi is very active in pursuing both approaches.
TaiyangNews: While trackers have seen a strong upward trend as of recently, we saw double-axis trackers being frequently used about a decade ago in Spain, but it was only doable in this high feed-in scheme. Now we are seeing the return of low-cost and simple single-axis solutions. Bifacial is also a pretty old technology, but it looks like its time is just coming now. Why?
Archie Flores: With every new technology, and that is true for every industry, there are always inherent risks in implementing something new. As part of LONGI's maturation process – expanding its presence from upstream silicon materials to modules – we have also established our own solar farm business. We have implemented some of these new approaches in some of our projects, therefore we expand our learning through better data and control our risks by communicating results to our technology and manufacturing teams.
There is still some skepticism, especially with the lack of meaningful data to-date, that backside energy harvest from bifacial products can provide a 10-25% boost in module output. By having our own reference projects, combined with the work we are currently doing with labs – that are testing various things like reflection, albedo, mounting conditions -, we can come to the market with quantified proof that better energy harvests does in fact occur from bifacial offerings.
TaiyangNews: Talking high output and high efficiencies. As the world's largest mono wafer manufacturer, LONGI is the key driver behind the recent mono trend. Currently, you focus is on p-type PERC technology, but n-type offers higher efficiencies – so when will you expand into n-type silicon cells?
Archie Flores: Indeed, our mainstream offering to the market is P-PERC. We have achieved very good results in production. We are at 21.2 to 21.3% cell efficiency, targeting the 22.0% level. I believe we still have some legs on our P-PERC technology. Our n-type technology is of course under development. The near-term challenge with n-type is balancing better performance attributes with the increase in cost. For now, we see P-PERC as our mainstream product, I think this should be true for the next 12 to 24 months.
As a technology leader, LONGi is always pushing the limits of what can be mass produced with the least risks and cost profile. If we think certain technologies are ready to be scaled up, then we want to be ahead of the implementation curve. One thing unique about LONGi is our strong R&D focus. We reinvest about 7 to 8% of our revenue into R&D, which is unmatched by any of our peers. We are always deep into the next technology node in solar and we want to ensure we are a step ahead of the competition.
TaiyangNews: Do you believe that the mono momentum will continue and even have a higher share than multi or will we see multi comeback once black-silicon and diamond wire saws are implemented on a large scale?
Archie Flores: The challenge for mono modules has never been about its performance attributes, it is mostly about its cost compared to multi. If we look at the recent announcements of the major solar companies, you can see that they are also bringing on a lot of new mono capacity. It is that shift that many expected, wherein mono's market share gains accelerate. I have seen forecasts which predict an even split by 2019 or so.
LONGi has been a 100% mono wafer supplier since its inception and we plan to continue to march on this path. We can sell half of the wafers to the market and half of it we are able to use internally.
Even if multi technology improves, we think mono will not regress. It should even get better because of cost improvements and the increasing know-how in crystal processes. One of the prior challenges for mono makers has been the limited talent pool for crystal operators compared to those doing casting. Casting multi ingots perhaps might be simpler but pulling mono crystal ingots is almost like a science and an art. Again, with better process know-how, lower equipment cost and the proliferation of talent, mono can continue to gain versus multi.
TaiyangNews: Can you give us concrete numbers?
Archie Flores: Let's look at what happened last year, when mono had about 15% market share out of the 75 GW global demand. In China, where LONGi drove the mono business, mono had an even bigger market share of 25%. A lot of mono capacity has been recently built. So we think that a global mono share of 50% is indeed not too far off. We are heading in that direction.
TaiyangNews: We are already seeing signs of decreasing module prices for the second half of 2017, several experts fear a strong consolidation in the coming months. How does LONGi prepare for such a scenario?
Archie Flores: LONGi is a fairly new module manufacturer. We acquired LERRI only in 2014. We sell a lot in China and are classified a 'top runner' (which is the 5.5 GW high-efficiency power plant program of the Chinese government), but we are not yet well known outside of China.
Over the past 12 months, our objective for LONGi has been to establish our overseas business. We are educating the market about our technology attributes and we are building channels and customers outside of China. We expect to gain overseas market share – in Europe, Asia Pacific, India and the United States. We are active in negotiations to lock several deals, especially in the US, where we are looking to execute various strategic partnerships.
We have our new 600 MW Malaysia plant – and we would like that fab to be able to at least supply the US; or in case there will be restrictions on imports, sell it to other major markets.
TaiyangNews: Regional diversification is one thing; what about vertical integration?
Archie Flores: First, we want to make sure we protect our core competence – which is wafers. So this area remains a priority in future investments, the other is projects. Last year in China, we installed about 200 MW, which we currently own and operate. This year, we expect to build about 800 to 900 MW of our own projects. In terms of midstream production – cells and modules – we handle it in a flexible way, where we use about half and aim to sell half of it. We sell wafers to some cell makers who are also suppliers for our module line. We like to support a healthy industry ecosystem.
TaiyangNews: You mentioned strategic partners. Some of your latest expansion plans will take place with partners, for example the new 5 GW ingot factory with Trina and Tongwei in Yunnan province. Why that?
Archie Flores: It is a partnership in wafers, and for Trina is its captive demand. Again, it is about controlling risks through partnerships, versus doing it solo. This also strengthens our relationship with Trina.
TaiyangNews: You even go upstream now – again with a partner. What about the 50,000-ton silicon factory you recently announced to build with Tongwei in Sichuan?
Archie Flores: LONGi uses a lot of polysilicon, but that's not our core expertise. Our interest here is to secure our raw material requirement. We want to control our risks, that is why we have teamed up with Tongwei, an experienced polysilicon manufacturer. Our general approach is to keep a very healthy ecosystem with our partners in the industry. There is plenty of opportunity in solar and we can build off each other's strength.
TaiyangNews: Thank you for the interview.
The interview was originally published in TaiyangNews Bifacial Module Technology 2017 Report, which can be downloaded free of charge here.