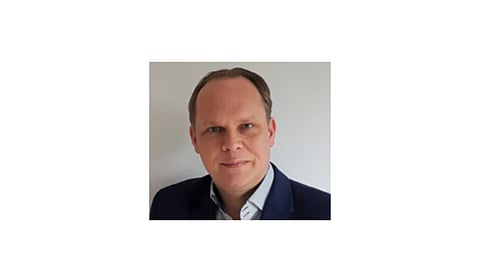
Originally, a French company that is now headquartered in Suzhou, China, Semco Smartech is again first with one of the hottest next generation cell technologies – Passivated Contacts. The first companies that have produced passivated contacts cells used Semco's LPCVD technology. TaiyangNews' Shravan Chunduri talked about passivated contacts cell technology to Raymond de Munnik, CEO of Semco Smartech France. De Munnik has been working in semiconductor and solar for 20 years, of which he spent 8 years at Semco, the pioneer in developing and offering low-pressure diffusion furnaces to solar cell manufacturers.
TaiyangNews: A lot seems to have changed with Semco. You even have a new owner?
Raymond De Munnik: We have spun-off our solar cell business activities into a new entity called Semco Smartech. It's a Sino- French joint venture headquartered in Suzhou-China and is acting as our global solar equipment manufacturing and service hub. In our existing R&D Center in France we continue to develop our solar cell process technology and matching equipment concepts. It's still the same original Semco PV team that's currently rolling out the HORTUS passivated contacts technology to our customers.
TaiyangNews: What's different under the new ownership?
Raymond De Munnik: First of all, we tripled our manufacturing capacity in order to respond to the current GW level orders. Secondly, such efficient, large scale manufacturing has a significant positive impact on lower equipment cost, which is nicely increasing the popularity of our HORTUS and LYDOP equipment. And last but not least, we managed to reduce our lead times drastically, allowing our customers to ramp up their fabs faster.
What has not changed and remains as in past – we are specialized in process and tools for doping and passivation applications. Our main product portfolio for PV still consists of diffusion furnaces, PECVD and LPCVD tools. We were the one that started the mass production low-pressure (LP) process first in 2001, nowadays phosphorous low-pressure diffusion has become a market standard. For boron diffusion we follow the BCl3 process, which is based on our patented LYDOP low pressure technology. All our process solutions are backed by our French Technology Competence Center, which is officially named Semco Smartech France.
TaiyangNews: With cell producers increasingly looking at high efficiency cell technologies, what offers does Semco have in store?
Raymond De Munnik: Passivated contacts! I truly believe that passivated contacts will be the next big thing. I can also explain why. Now everyone agrees that PERC is a success story. If we analyze what has made PERC a success, then it is very easy to identify its successor. There are several factors that are influencing the wide deployment of PERC, but to me the main reason is that it is closer to the mainstream than other technologies. The historic transfer of Al-BSF to PERC added roughly three process steps – aluminum oxide/silicon nitride stack on the rear and laser opening. Upgrading to passivated contacts is quite comparable. Simple cleaning and Semco's HORTUS are required as additional steps.
Passivated contacts technology is solving some of the limitations of PERC, where the production technology and engineering level used is close to the current experience of cell producers. It's a much smaller and therefore safer step to upgrade to passivated contacts. This was exactly where PERC was a few years back.
Not only that, if companies are producing BSF cells, then they can easily go to passivated contacts, they don't even have to do PERC. The engineering effort to upgrade from Al-BSF to PERC is similar compared to AL-BSF to passivated contacts. Semco is supporting both customer paths – intermediate step to PERC or simply go direct to passivated contacts technology – with guaranteed electrical cell performance in mass production. For all these reasons I consider passivated contacts will be the next big thing.
TaiyangNews: What's your solution for manufacturing passivated contacts cells?
Raymond De Munnik: Semco's solution is based on our HORTUS LPCVD technology. We have integrated our LYTOX reduced pressure Oxidation process, which allows in-situ growth of thin SiO2 layers, the base of the passivated contacts structure. This is already qualified in mass production. An ultrathin doped polysilicon layer needs to be stacked on top of it.
Actually, there is plenty of choice among the traditional semiconductor methods, such as APCVD, PECVD, LPCVD and so on. We looked at most of these technologies. From this experience, we selected LPCVD as others have not worked due to complexity and/or costs reasons. The third step is doping of the polysilicon. Our tool platform supports in-situ doping; however, the final choice is typically made by customers based on their existing equipment set. Semco's HORTUS solution accomplishes all these three steps in one combined machine.
TaiyangNews: What is the specialty of your LPCVD tool over others?
Raymond De Munnik: We already do horizontal processing on M6 wafers. Semco historically was also processing the wafers using vertical orientation which used to be common in the PV industry. However, with the wafer size continuously increasing while the thickness is showing a decreasing trend, Semco standardized all of its wafer processing in the horizontal method. For our HORTUS LPCVD platform, the horizontal orientation also prevents wafers sticking after deposition, and parasitic disposition is controlled by nature.
TaiyangNews: How do you deal with the wrap-around issue?
Raymond De Munnik: It is not about wrap around "yes or no" we can't beat physics. It is more about whatever the wrap around is there, is it constant or not. That means, there should be a wide process window, then it can be tackled easily in the process flow. Since we are doing horizontal processing, we control the wraparound very effectively along the full reactor load in front-to- front loading configuration.
TaiyangNews: As throughput is an important aspect of these deposition tools, can you give the throughput of a typical mass production configuration of your solution?
Raymond De Munnik: Currently Semco's HORTUS LPCVD platform is processing 7,000 wafers per production cycle using only 5 reactors. Depositing 100 to 160 nm polysilicon after an in-situ grown tunneling oxide is currently executed above 4,000 wafers per hour, where the full integrated process takes place in one reactor without breaking of vacuum.
TaiyangNews: Are you recommending any specific process flow?
Raymond De Munnik: We are truly mastering the thermal budget management of the cell. As a result, we are supporting customers that have both process flows – emitter first and emitter last. Nevertheless, we are especially proud of our 'emitter last' cell process flow, which is already running in mass production using our LYDOP Boron BCl3 technology together with our HORTUS LPCVD. It is displaying our historic expertise of individual layer technology combined with complete cell integration.
TaiyangNews: Are you offering any performance guarantees?
Raymond De Munnik: With our method, we typically display 735 – 740 mV implied Voc of the passivated contacts precursor cell (before metallization). When required, we can adjust our process flow to already existing process equipment of our customers. More or less 20 mV is the difference between al-BSF and PERC, this can be easily repeatable with upgrading from PERC to passivated contacts.
TaiyangNews: We heard rumors that LPCVD tubes are breaking at the cell manufacturers. Is this true and if yes, what are you doing to prevent it?
Raymond De Munnik: Thank you for asking this question. Deposition methods like PECVD and LPCVD are typically depositing not only on the substrate, but also on the tray or carrier, or even on the reactor itself. A typical traditional semiconductor based LPCVD system is also subject to this effect. As a result, the quartz reactor needs regular maintenance, which is not a priority typically in PV. This is also why people suffer from quartz reactor tube breakage. The deposited poly sticks on the tubes, and due to the thermal stress, the tubes break. Semco has anticipated this problem and developed a proprietary full metallic HORTUS LPCVD reactor. As a result, we are not suffering from quartz reactor breakage anymore. It's another good example of Semco's excellence. Combining long process experience with high level equipment designing capability that is tailor made for the harsh and low-cost requirements of the PV industry. However, my message to the industry is irrespective of the process and technology, the manufacturers must stick to the maintenance cycles.
TaiyangNews: Can you name the companies who are using your production tools in production?
Raymond De Munnik: I can't be specific, but what I can tell you is multiple Korean and Taiwanese customers have adapted our technology in mass production. We are now rolling out our HORTUS Passivated Contact Cell Equipment into Mainland China.
TaiyangNews: Can you please specify the cell efficiencies you have attained at your customers?
Raymond De Munnik: Our customers, transferring from PERC, attained 23.4% average cell efficiency in mass production using our diffusion and standard multi busbar printing. For back contact cell technology, we already qualified 2 years ago over 24% cell efficiency.
TaiyangNews: What's your cell efficiency roadmap for commercial passivated contacts?
Raymond De Munnik: We are currently focusing on industrial, simple, robust and cost-effective processes exceeding 24% cell efficiencies. For the long term we expect passivated contacts to be an essential building brick for processes for p- and n-type wafers, applicable for existing and upcoming cell technologies breaking the 26% barrier.
TaiyangNews: ITRPV 2019 forecasts passivated contacts to expand its share from around slightly less than 5% in 2019 to above 15% in 2023 and exceeding 30% in 2029. Where do you see the market share of passivated contacts cells in 5 and 10 years?
Raymond De Munnik: We expect passivated contacts to be mainstream by then, since it's the logical successor of PERC. It's of course difficult to predict which exact cell technology will be dominant, but I'm quite convinced passivated contacts will be an essential element.
TaiyangNews: And what part of these share of passivated contacts are you targeting to be produced on Semco devices?
Raymond De Munnik: We are already providing all essential thermal processes and matching equipment. Our Tools for emitter or field doping, ultra-thin or thick thermal oxides, polysilicon deposition and other advanced passivation layers have all been integrated in mass production. So, we are pretty well aligned to continue to be major technology mainstream trendsetter. Of course, we continue to keep our equipment design modular and therefore flexible in order to continue to meet industry process trend demands.
TaiyangNews: Thank you for the interview.
This interview was published first in our TaiyangNews High Efficiency Solar Cells 2019 Report, which can be downloaded for free here.