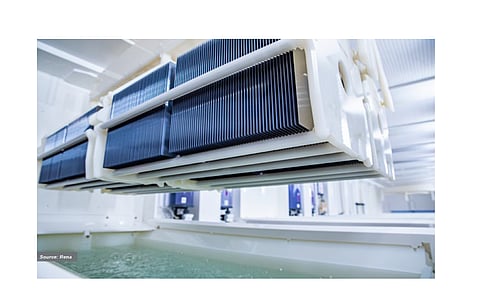
No discussion about solar cells is complete without involving cost and efficiency – the 2 measuring sticks of progress. While cell design and process material are obvious topics of such a conversation, one part of the equation often doesn't get the attention it deserves, and that is production equipment.
At the TaiyangNews Virtual Conference On Pushing PERC Into Limits, one key message that resonated was that there is little room for further efficiency improvements of the incumbent cell technology, but still some cost savings potential, and mainly through production equipment.
At the end of 2021, 23.2% was the average cell efficiency as claimed by leading PERC suppliers, and a number of experts believe that 23.5% remains achievable through process optimization, but anything beyond makes little economic sense. However, any further improvement has to come from elsewhere, which is on the cost side.
PERC's cost advantage is undeniable and is the major reason it enjoys its dominant place in the industry – and is seeing still companies investing in expansions or even new cell factories based on that technology. Most go with lower-cost Chinese production equipment that is dominating the cell space today. However, even current cell fabs had to invest in new PERC cell production equipment.
The most important change that has taken place recently is that PERC production tools now possess the ability to process larger wafers. This has taken some serious effort on the part of equipment vendors to develop tool platforms flexible enough to handle all the mainstream wafer sizes from M6, M10 and G12. And as part of the redesigning process, there also has been a push towards improving the throughput of such tools. The results are visible in much higher production capacities today. In most of the important process stations, only 2 pieces of equipment in their full configuration are more than sufficient for a GW-scale production line.
And not just throughput, the tools have also undergone optimization on the material consumption front. The wet-chemical tools, for example, now consume dramatically less chemicals. Replacing the acidic process with alkaline is another step in this direction. And of most importance, there has been a considerable reduction in the consumption of metallization pastes. All this comes as a result of the optimization of screen printers.
A question still lingers on – how much further cost reduction potential can be tapped? Well, when looking back at what's been achieved, what's in store might look too small, but a CapEx reduction of about 10% doesn't seem too far a target. And again, any major optimization has to come about via enhanced tool throughout and productivity. There is also some scope for improvement on the process consumables side. And several other parameters, such as power and utility consumption, exhaust management and environment protection measures, may also matter at a facility level.
On the technology front, while there is nothing to prove one way or the other whether processing half wafers —and its applicability for PERC — is a trend, the industry is giving it a serious thought for sure. One of the benefits of such a process is the elimination of edge losses. But this does come at the cost of halving the throughput for batch systems; and while it's not a big deal for inline tools, they are not all that common today.
All the pros and cons of PERC weighed and put aside, it can be taken for granted that equipment makers will continue making improvements in production tools for PERC. Such improvements so far have brought the technology to an efficiency and cost level many experts did not believe in. And even given all the talks of PERC having found or being close to reaching a plateau; the recent improvements won't be lost as the natural successor to PERC is TOPCon, which is based on the same production equipment, it just needs a few more steps.
This is the conclusion part from our new TaiyangNews report on PERC Cell Production Equipment 2022, which is available for free download here