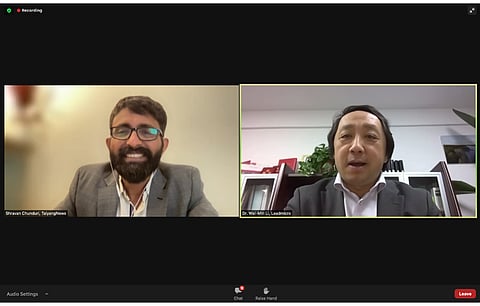
PERC is the workhorse of today's solar industry. While there are serious efforts to commercialize further advanced cell technologies, stakeholders work hard to further improve incumbent PERC to continue solar's cost reduction path. PERC was also the main theme of the TaiyangNews Virtual conference on Pushing PERC to Its Limits – How To Manufacture Highest Efficiency Standard PERC Cells on March 22, 2022. The conference mainly focussed on the manufacturing side of PERC, especially innovative production equipment solutions from leading suppliers to improve the performance of PERC cells and reduce costs. The event also included an executive fire chat with Shravan Chunduri of TaiyangNews and the CTO of Leadmicro Dr Wei-Min Li discussing the further scope to "push PERC to its limits". Below is the Q&A of the fire chat from the conference (edited & summarized).
TaiyangNews: Taking the lead of the conference title "Pushing PERC to Its Limits," in your opinion, has the industry already pushed PERC to its limits, or do you still see room for further improvement?
Wei-Min Li: I have to be very cautious here! And this is purely my personal opinion. Efficiency wise, it's very close to the limit, at this point. However, there is still some space in the area of costs. From the costs perspective, PERC still has a potential in the area of manufacturing costs, CapEx and overall costs that would enable the technology to compete with the latest technologies such as TOPCon, HJT and XBC.
TaiyangNews: As you said, PERC is still the leader in terms of cost performance ratio, so how long you think, PERC can sustain this position?
Wei-Min Li: That's a good question, but it's actually hard to predict. The technologies in PV and the industry have been changing really fast. It may change overnight. What I wish to see is that the higher efficiency technologies are coming to the market sooner rather than later. When the majority of the industry, both technology and market wise, shifts to any high efficiency technologies, for example to TOPCon, it will affect PERC, especially when it cannot keep up its cost performance ratio.
Currently, we are working very hard on TOPCon and already seeing that costs are coming down fast with improvement on the yield and efficiency. The benefit with TOPCon is that we can use almost all of the production tools used in PERC for TOPCon too. Of course, one important message here is that TOPCon has to have ALD to assist this technology and where the low cost is quite critical. And we do see that these are coming down very fast.
TaiyangNews: ITRPV's 12th edition thinks that PERC's share will decrease in the coming years; gradually down to about 35% by 2031. Do you agree with this?
Wei-Min Li: I actually worked with a few contributors to ITRPV and the projections of the roadmap to my knowledge are quite precise and gives a good outlook on where PERC is going to end. To put it simple, yes I completely agree with ITRPV projections.
TaiyangNews: Where do you see further potential to reduce the equipment CapEx and OpEx for PERC?
Wei-Min Li: As for our part, we are definitely working on the lowest cost equipment to meet PERC market demand. I would say, it's not just equipment alone, there are several things that come along and become important at a facility level such as power and utility consumption, exhaust management and environment protection measures. It's then a big project. And this is also why we are actually working on what we call smart ALD enabled PERC. I definitely think there is a scope. It's like a sponge – there are a lot of things to squish when you introduce smart management to PERC lines.
TaiyangNews: What is the potential decrease in CapEx? Can it go down by 10% to 15% in coming 2 years, or even more?
Wei-Min Li: If you just look at the ALD progress; presumably though the price of the tool has not changed a lot or even increased a bit, the throughput went up from 5,000 to 20,000 wafers per hour. This is 4 times in 5 years. So I think 10% can definitely be achieved.
TaiyangNews: How important is PERC CapEx in today's PERC LCOE calculation for a leading manufacturer and also a new player?
Wei-Min Li: The current PERC production technologies favor new players in terms of CapEx and investment, that's clear. I see some encouragement in new markets such as Southeast Asia and even in Europe. I had a few interesting discussions with companies that have plans to venture into cell making and they can clearly see the advantages.
TaiyangNews: Is there any optimization potential left on the process consumables end?
Wei-Min Li: Yes. Even though I previously mentioned the PERC limits in efficiency, I think there is still a chance to gain 0.1 to 0.2%. This is possible with materiel optimization, which not only helps in reducing the costs, but also enable slight improvement in efficiency. I cannot go into details but I can say that we are currently working on some new materials apart from aluminium oxide that can improve overall performance of PERC such as reliability, stability and efficiency without affecting the costs.
TaiyangNews: Do you see any small changes that can be brought onto the p-type platform to continue the PERC legacy?
Wei-Min Li: Oh, yes. The topics was also covered in one of the preseantions at this conference. The majority of the market is p-type and even with technologies such as TOPCon, there are some new technologies that companies are working on to be based on p-type substrates, including Leadmicro. So I think the p-type substrate too will have a significant market share, while the share for n-type would grow much faster.
TaiyangNews: Do you see structures like POLO from ISFH for example can come into the mainstream?
Wei-Min Li: It is difficult for me to comment on POLO specifically, but definitely there are technology routes for advanced cell architectures based on p-type wafers that would come into play. In fact, we are working on such kind of development together with our customers.
TaiyangNews: As a leading equipment maker, if you look into the crystal ball, what would be the significant developments in the cell segment in this decade?
Wei-Min Li: It's a difficult to predict what would happen in 10 years. However, as I have shown in my presentation, we are working on silicon based tandem cells at the research level. This is not only part of Leadmico's technology roadmap, several companies are working on using silicon bottom cell based tandem structures. We, at Leadmicro, are focusing on R&D of tandem cell technology related equipment, processes as well as the cell technology.
TaiyangNews: Thank you for the interview.
To view the recording of the interview with Wei-Min Li or the other presentations of TaiyangNews Virtual conference on Pushing PERC to Its Limits – How To Manufacture Highest Efficiency Standard PERC Cells, please check our YouTube Channel here.