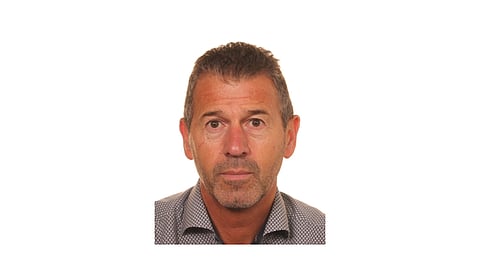
Rudi Peters is the global responsible manager for all value chain activities of Borealis linked to the solar industry. He has defined the Austria headquartered company's strategy for solar applications – from marketing, innovation, IPR portfolio and sales planning in particular for the solar backsheet market.
Borealis is a chemical company with 6,800 employees, that has its head office in Vienna, Austria. Together with its sister company Borouge, which operates the world's largest single chemical plant in UAE, the turnover in 2018 was €9.9 billion.
TaiyangNews: Borealis is a huge chemicals company. What brings you into the solar industry?
Rudi Peters: Renewable energy is important to Borealis, because it is the future. Naturally we want to be a part of it, and indeed we are already active in this field. The high voltage DC cables used in wind energy systems are mostly using Borealis material, the same is true for low voltage cables used in solar parks. Our PP films are also used as capacitor films in inverters. We hold the world record in producing the thinnest capacitor films with Borealis PP material.
The solar industry is growing very quickly and has now reached a level where the volumes are big enough for a company like Borealis to participate. We bring 50 years of experience in polymer chemistry and a strong balance sheet. Borealis is a sizeable company with 6,800 employees and with its head office in Vienna, Austria. We currently operate the world's largest single chemical plant in the Emirates. Together with Borouge, our 2018 turnover was €9,9 billion and our net profit, €906 million. Therefore, we are highly bankable.
TaiyangNews: Polymers are used for encapsulation and backsheets in module manufacturing. What's your targeted segment?
Rudi Peters: We have innovative solutions for both the segments. With our encapsulant material we are targeting segments where quality and long- term performance are important but where module makers were hesitating to switch to PE because of the longer cycle time. With our QuentysTMencapsulant we offer a significantly shorter cycle time than POE or EVA encapsulant. If you use standard EVA as an encapsulant, the degradation in 25 years is around 20%. With our encapsulant, the degradation after sequential testing is around 5%, meaning our product is outperforming the current industry standard by many factors.
However, in fact all polyolefin encapsulants are giving much better resistance to long-term electrical output degradation over EVA. Polyolefin encapsulants can expand the lifetime of a PV module. It also increases the electrical output in kWh. So if you want to optimize your PV modules in terms of kWh, then a polyolefin encapsulant is a much better solution. Unfortunately, today the market is still too focused on watt peak output, which only tells you about the output at the starting point but does not give any information about the long-term performance. However, we are starting to see that markets are drifting to the kWh metric, but there is still a long way to go.
TaiyangNews: And what about your backsheets?
Rudi Peters: For backsheets, we promote our polypropylene compound Quentys PP as an alternative to the PET core layer. Our PP based solution is simply better as a material compared to PET in all specifications for a core layer. Additionally, our Quentys PP solution as a backsheet's core layer also helps in reducing the costs for backsheet makers, which is key in today's PV market.
TaiyangNews: While PO is being offered by a couple of other companies, PP is very uncommon among backsheet products so far. Why is that?
Rudi Peters: One can of course buy standard PP from the open market, but it would not fit the purpose of making a good backsheet. That is because, the requirements for backsheets are quite tough to meet. Reflectance, adhesion to the layers, adhesion to the junction box, thermal cycles and thermal expansions are a few topics on the list of key functionalities a good backsheet has to qualify. For these reasons, special PP compounds have to be designed which increases the cost for the backsheet. This is also true for any other company that is working on a PP based solution for backsheets.
Our product eliminates the compounding effort for the backsheet makers, differentiating it in the market. Using our in-depth know-how in polymer design and in cooperating with backsheet makers, we optimized it in a way that Quentys is available in a "ready to use" form for backsheet makers.
I have to be honest here; we needed an experienced partner from the backsheet side in order to develop such a compound that fits nicely into the whole backsheet equation – to be cost effective and reliable.
TaiyangNews: Backsheets are usually a compound of several polymer foils, primers, coatings. Which part are you looking at with your products?
Rudi Peters: What we see is that PET as a core layer has some inherent weaknesses such as low hydrolysis resistance and a rather high-water vapor transmission rate. To protect the shortcomings of PET that is unable to stand against environmental assaults with UV, humidity, typically backsheets require very good outer materials like Kynar or Tedlar. We have considered all these shortcomings of PET when designing our PP based core solution. We also made Quentys with acetic acid permeability, which is important for a backsheet. One of the biggest limitations with the standard PP was the thermal cycle tests. We really had to make a special compounding in order to pass all those tests. Coming back to the question, our primary objective is to replace the PET core layer with our SF700CL core layer.
The PET core layer has some weaknesses – hydrolysis, water vapor transition. You need a good outer layer to protect the core layer. As we have fine- tuned the PP for the core layer, we have taken away the disadvantages but kept the advantages. The biggest challenge for PP was the thermal cycle test.
TaiyangNews: Solar is not only quickly growing but also characterized by quickly decreasing cost, which is a challenge for materials suppliers.
Rudi Peters: The traditional materials used in the solar industry (EVA for encapsulants) and (PET as core layer for backsheet) have reached the bottom of cost optimization. For example, EVA film is almost at the same level as EVA resin in terms of costs.
So there is not much left to squeeze it further. It is the same case with PET, especially for backsheet related applications. The PET supply chain has already been pushed to the limits in terms of cost reduction with not much scope left for further optimization. Therefore, if you really want to go for low cost solutions, you have to look outside the box and in the case of the backsheet, PP, especially for the core layer, is a good alternative. Quentys PP will bring inherent savings that are not possible with PET anymore.
TaiyangNews: How is it that PP has a cost advantage?
Rudi Peters: PP has 3 big advantages compared to PET – lower density of PP versus PET, a better water vapor transmission rate (WVTR), and it allows extrusion by backsheet makers themselves. What we hear from the market is that backsheet suppliers want to start production of their own PP film.
Starting from PET resin and going to PET layers, the cost difference is about 3 RMB per kg. Additionally, making PET requires special equipment, know-how and experience. To go from PP base resin to PP core layer film you should be able to reduce the cost by around 50% and if the backsheet producer co- extrudes his own PP core layer the saving will be significantly higher.
TaiyangNews: You mention co-extrusion: What's the advantage of co-extrusion for laminators?
Rudi Peters: The difference between PET resin and PET core layer film is approximately 3 RMB/kg. To go from a PP based resin to a PP core layer film you should be able to reduce the cost by 50% and if the backsheet producer co-extrudes his own PP core layer the saving will be even more.
TaiyangNews: But you would probably have to invest in new extrusion equipment, right? What would that cost?
Rudi Peters: Yes. In China you can buy a line for $200,000 to $300,000. The ROI is less than 1 year. When the volumes are high, the ROI is even shorter. As I said earlier, in the beginning backsheet makers would probably buy or ask somebody to make the PP core layer for them. That company would be making this additional margin in the beginning, but once they have established the product line and calculated again, the next step would be doing it by themselves. In our discussions with leading backsheet makers, we realized that more and more backsheet suppliers are already thinking about making the core layer for themselves.
TaiyangNews: Can you put the other benefits into numbers? How much material can you save due to the low density of PP versus PET and what is the WVTR?
Rudi Peters: The density of PP is 1.02 g/m2 versus PET of 1.38 g/m2, which means for the same dimensions you need 26% less PP weight. For example, take 1 m2 film with 250 μm thickness as a reference; 360 g of PET is required, while just 260 g is sufficient in case of PP. Then the lower WVTR also allows a reduction of the thickness. The WVTR rate of PP is about 0.8 g/m2.d while PET has a WVTR rate of greater than 2 g/m2.d.
TaiyangNews: How much thickness can be reduced on the account of this low WVTR?
Rudi Peters: This has to be evaluated by every backsheet supplier themselves by doing some tests. There are several possibilities, because the thickness reduction depends on the outer layer you are using and the type of PV module you produce. The core layer thickness also influences the final thickness of the backsheet, which is also a criterion for breakdown voltage class – 1,000 V or 1,500 V. However, for a 1,000 V module where you are typically using at 250 μm PET thickness film for the core layer you can easily reduce the thickness in the case of PP to 200μm. We have done some tests with 200 μm and it works fine without any sign of risk. This already brings in 20% material savings.
TaiyangNews: All that translates into how much of a lower cost for the backsheet laminator?
Rudi Peters: For a backsheet maker that uses at least 30 million m2 core PET film, which most of the backsheet players are doing, by replacing PET with PP, the saving should be between 10 to 20 million RMB on raw material cost only. I am somewhat conservative here; first because the backsheet suppliers have to spend on optimization of the production process and lines, as well as consumables such as adhesives, which are currently adapted for PET as a core. The laminators will have to find their sweet spot for PP, after a year they will be able to reap more benefits.
TaiyangNews: To be able to offer a product at a lower price you usually have to be able to compromise on quality.
Rudi Peters: In this case, the savings are not coming from the product as such, but a cut in volume that is being used. As I explained earlier, you can reduce the amount of raw material for the same thickness. On top, PP has better quality attributes. In contrast, since PET is hydrolysis sensitive, a backsheet using PET as core layer requires highly protective and expensive outer layers. With PP, the importance of the outer layer reduces, thus it enables the use of thinner outer layers. If you use a PP core with Tedlar, then you may have a product that could last much longer. Quality wise PP is just a better product than PET. The same is valid for encapsulants – polyolefin is better than EVA. The problem with encapsulation is that a polyolefin encapsulant is more expensive, while in the case of PP, thanks to better density and water vapor transmission, the sheets of product you need is less to get the same, or an even better, job done. All this speaks for PP to be the product for the core layer in the future.
TaiyangNews: What's the biggest barrier you see for PP to take away shares from incumbent polyester?
Rudi Peters: It is like who is biting the bullet and goes first. The biggest hurdle is that backsheet makers have to step away from what they are used to and they need to try something new, which can be uncomfortable in the beginning. If you are used to Mercedes and change to Ferrari, the Ferrari looks probably awkward in the beginning. You need a few large laminators and module suppliers who are willing to switch over to a PP core layer-based product. All these steps have to be taken one after the other, which will take some time.
TaiyangNews: What about disadvantage of PP compared to PET?
Rudi Peters: The melting temperature of PP is lower than PET, but we don't consider this as an issue. We have talked to leading laminators who said, they don't see this as an issue either. The majority of the leading module producers are laminating below 150°C, which is perfectly OK for our compounds.
TaiyangNews: Module manufacturing mostly takes place in China – and today most materials are often sourced domestically. In fact, the share of non-Chinese backsheet suppliers has decreased dramatically. Can you share your go- to-market strategy?
Rudi Peters: First of all, through our Borouge organization we are already very active in China, where we also have our own sales organization. Secondly, we have hired Chinese solar experts, located in Shanghai, able to rapidly respond to customer requests. We will also have local warehouses to be able to have short lead times in China.
Regarding our long-term strategy, at Borealis we are very committed to put our efforts into promoting new materials for encapsulants and backsheets in the solar sector to contribute our know-how to support further cost reduction of solar. This is a first dedicated solar business line. Borealis is also considering other ways, for example, looking at what we can we do in the area of floating panels. This PV segment also uses high-density polyethylene to make floaters for PV panels, for which we have interesting solutions.
The solar industry is such a dynamic industry, where we as Borealis see huge growth potential. Our deep knowledge in polymer technology will give us the opportunity to come up with new solutions for problems that do not have suitable existing solutions. We plan to keep on coming up with new innovations that will make the solar industry more cost competitive. Borealis wants to be a major player in the solar industry in the long run to make this happen.
TaiyangNews: Thank you for the interview.