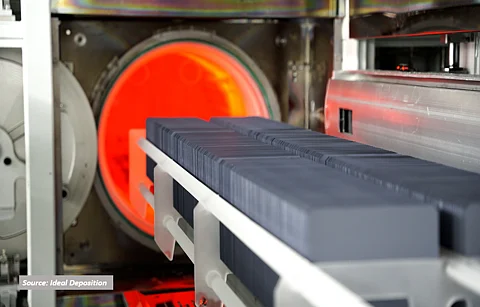
Just in about a year time since TaiyangNews published the market survey on PERC cell production equipment May 2022, the PV manufacturing sector experienced a swift and transformative evolution. The emergence of TOPCon as the new mainstream technology is a pivotal development in the industry and has quickly established the technology as the benchmark for optimizing production equipment, marking a significant shift in the field. In response to the prevailing market trend, TaiyangNews has expanded its production equipment survey to include TOPCon, reflecting its growing importance.
TOPCon and PERC, with their similar process sequences and production equipment, share identical key process steps which include: Surface preparation, Emitter formation, Passivation, Metallization, Testing.
This survey presents the latest developments associated with key production equipment used in the above processes, mainly referring to TOPCon, also covering the updates related to PERC, as and when available. We cover 7 different tool platforms serving 10 applications; a total of 76 products from 17 companies listed in the survey. Within the surface preparation step, mostly accomplished with wet-benches, the survey covers a wide variety of applications including saw damage etching (SDE), texturing, doped glass removal, edge isolation, rear side polishing and polysilicon wraparound etching. However, the first 2 steps are mainly accomplished with texturing tools, while the remaining steps are undertaken with etching systems. We show data for 23 products from 5 companies active in this production step. In the alkaline texturing part, which is typically a batch process, Schmid stands out with an inline solution. The entire production range of the German company supports inline philosophy. The most notable developments in the texturing section related to TOPCon as well as for PERC are reducing reflectivity, by means of exclusively developed additives for each cell technology to optimize the pyramid shape, size, and density. For junction isolation and polysilicon etch as part of the TOPCon process, cluster configurations are popular in China. However, companies like RENA, while offering such cluster solutions, also promote inline solutions. In addition to these wet benches, the survey also includes details of dry atmospheric etching tools that can accomplish all the surface preparation steps.
Diffusion is the state-of-the-art technology for formation of emitter, and batch type tube furnaces are typically used for this application. The working principle of these tools remains the same for PERC and TOPCon, requiring phosphorus and boron diffusion, respectively. Both the processes are accomplished at low pressure. However, the tools are different when looked in detail, especially boron diffusion tools are designed to support a high temperature process above 1,000 oC. The ability to support the formation of high sheet resistance emitters is a common development within this tool set. While the selective emitter is a standard in PERC structure, more and more TOPCon players are including selective boron emitters as part of the cell structure. Though not new, but an interesting development related to emitter formation for TOPCon is that the industry is increasingly preferring BCl3 as the precursor instead of previously used BBr3. We have listed a total of 14 products from 7 companies in this section of the survey.
Passivation is the crux of any advanced cell architecture and especially the rear passivation is what differentiates PERC as well as TOPCon over their respective predecessors. The passivation schemes and required production equipment vary for different cell architectures. TOPCon involves the growth of interfacial silicon oxide and deposition of intrinsic polycrystalline silicon layers, which is subsequently doped. The tunneling oxide can be grown thermally or as part of any other deposition methods used for polysilicon deposition, which is the heart of the TOPCon process. LPCVD and PECVD are the mainstream processing devices and are also in the scope of this survey. LPCVD tools are available with different degree of process integration – with or without tunnelling oxide applications and in-situ or ex-situ doping. All the systems of the survey can accomplish all the 3 steps – tunnelling oxide, polysilicon deposition and in-situ doping. However, to gain on throughput, doping is executed externally. PECVD systems, on the other hand, accomplishes all the steps by default. TOPCon cells also require aluminum oxide deposition tools for front surface passivation, and ALD is becoming primary choice.
As to the passivation needs of PERC, the rear surface is deposited with a stack of aluminum oxide and silicon nitride. Here, aluminum oxide can be applied with either ALD or PECVD, while the silicon nitride capping is typically applied with PECVD tools. On the other hand, 2-in-1 PECVD tools can deposit both aluminum oxide and silicon nitride in one go. The front of the PERC cell is not different from BSF, thus it is passivated with PECVD deposited silicon nitride. As many as 5 different tool platforms are discussed under the passivation section of the survey. A total of 27 products supplied by 6 vendors are featured in this part of the survey.
Developments in metallization are a collective effort from 3 different streams – metallization pastes, screen printers, and screens. Developments in these 3 areas enabled the screen printers to continue to be the workhorses for metallization. While the context of the survey is mainly focused on production tools, meaning screen printers in the metallization section, the survey also provides a brief update on screens and paste consumption. Reducing the silver consumption has always been the topic of focus in metallization. While PERC due to its single side silver consumption and great level of reduction achieved already is not an issue anymore. However, as TOPCon requires silver on both sides, reducing silver consumption is a priority. As to the products listed in the survey, 4 vendors of screen printers have provided data for 6 products.
PV products are tested indoors in simulated sunlight, facilitated by cell testers in cell lines. It is still the only section of the equipment supply wing that is dominated by Western vendors. We have 6 products from 4 companies featured in this survey. A major differentiating factor among the cell testers in the market as well as in the survey is the light engine – either a Xenon lamp or LEDbased. Quick characterization of high capacitance solar cells is a topic for relevance to TOPCon, and all cell testers are offering algorithms to support this measurement. The survey lists 6 tester products from 4 suppliers.
In addition to summarizing the latest developments associated with key production equipment, the survey also tabulates the important specifications of these production tools in the order they are discussed in the survey.
Today's TOPCon technology is governed by 2 steps – realizing the passivated contacts on the rear side and metallization. The 2 mainstream technologies for the former are LPCVD and PECVD and we have included interviews with executives of leading suppliers of these equipment – Laplace and Leadmicro – and also the leading supplier of pastes, DKEM, to provide insights into respective technologies.
This is the executive summary of TaiyangNews latest report on Solar Cell Production Equipment 2023, which can be downloaded for free here.