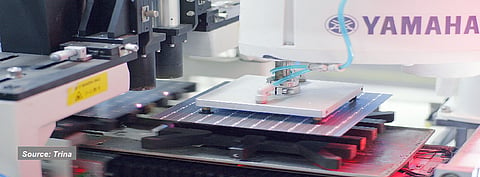
At TaiyangNews Virtual Conference on High Efficiency Solar Technologies, JA Solar presented its evaluation of M10 cell production benchmarked against M6. The company identified 3 aspects as part of the risk assessment:
The Chinese PV company found that the yield for 182 mm cells is basically the same as for 166 mm cells after the production process was stabilized, and efficiency is also expected to be the same soon. The qualification rate at 98.2% is very close to 98.8% with M6 size. JA Solar collected data for 9 days on the cell reverse leakage distribution parameter, something that influences module reliability. The reverse leakage data from the company's production showed that more than 99% of the cells fall into a band of 0 to 0.5 A, the accepted spec in production.
On the other hand, Risen emphasized at TaiyangNews Virtual Conference on Advanced Solar Modules that CapEx spending for the 210 mm production line at a GW scale is about 20% lower than the equipment spending required for 182 mm. This view was also shared by LONGi; according to the company's presentation in the 182 mm section of our High Efficiency Solar Technologies Conference in Dec. 2020, G12 wafers do have a cost advantage over M10 at the cell level. The economies of scale associated with G12 afford a relatively high throughput per tool (in MW metrics). When the stage is all set, the additional costs incurred in wafering can be made up at the cell lines in processing 210 mm wafers with nearly the same benefit of about 0.15 to 0.3 US cents/W.
For pure cell makers, like Tongwei and Aiko, who do not have any direct up or downstream capacities attached and just care about cells, G12 is naturally the preferred wafer format from a productivity point of view. Tongwei, as it is evident from its online price quote (see the graph), started offering G12 cell sizes as mainstream product since the end of 2020. However the production facilities of pure cell makers are flexible, able to process M10 and smaller wafer sizes according to orders.
Increasing the wafer size also brings performance benefits for solar cells. Although it sounds counterintuitive, increasing the wafer size is actually helping to improve efficiency. One of the main reasons is that all larger wafers are made using the latest tools based on advanced technologies at all levels of the process chain – from wafers to modules. This results in high-quality raw material for cell lines, which are processed using brand-new machines at the cell level as well. Process uniformity and control are at their peak, and the end product is of superior quality. These larger wafers are also compatible with advanced metallization layouts, such as multi busbars (MBB). For example, a 5-busbar layout has been the mainstay for M2 and G1 formats, while MBB with 9 wires are most compatible with M6. With more space available on the larger wafer formats, a higher number of busbars can be utilized – up to 12.
The text is an excerpt from the TaiyangNews Report on Very High Power Solar Modules: Summarizes Most Notable Developments Along Manufacturing And PV Value Chain for Panels Based on Large Wafers & Provides Overview on Latest Products of Leading Module Suppliers – The TaiyangNews Market Survey Report can be downloaded for free here.
TaiyangNews Reliable PV Module Conference 2021: While the leading cell and module manufacturers continue expansion of the latest technologies using larger wafers, TaiyangNews will organize its Reliable PV Module Conference, bringing together key stakeholders active in the various parts of module manufacturing to discuss reliability of the solar module as the heart of a solar system. We have speakers and panelists from module makers Trina Solar, Chint/Astronergy, Risen Energy, encapsulation and backsheet makers Jolywood, Cybrid, and R&D, testing and quality control experts TÜV Rheinland, CEA, Polymer Competence Center Leoben.
TaiyangNews will also presenting an overview of our upcoming TaiyangNews Backsheet & Module Encapsulation Market Survey 2021 during the event.
For Free Registration and Agenda, please click here: