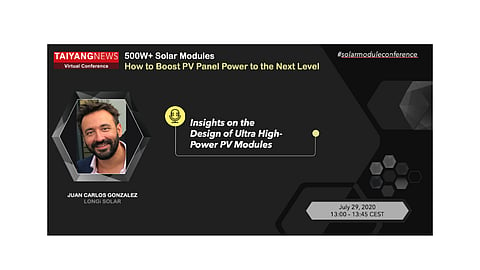
Over the past few months, leading module makers have been in a race to bring higher power modules to the market, raising the bar for utility-scale panel power to 500 W and more. Acknowledging the trend, TaiyangNews organized a virtual conference on the topic: 500W+ Solar Modules - How to Boost PV Panel Power to the Next Level (see TaiyangNews Virtual Conference on 500W+ Solar Modules). All leading module producers that had announced 500W+ modules in H1/2020 took part in the event and presented details of their technologies. We are summarizing the company presentations at the event and also include the Q&A parts—here, for LONGi Solar.
Reducing BOS costs not only helps in reducing the CapEx of the PV installation, but also OpEx, and module power plays a major role in BOS costs. Increasing the power by 2% can reduce BOS costs by 0.14 US cents per watt, according to LONGi Solar's senior sales manager Juan Carlos Gonzalez. Presenting at TaiyangNews Virtual Conference on 500W+ Modules, Gonzalez provided the background information and discussed the design aspects of Hi-MO5, the latest module series from LONGi, the Chinese vertically integrated module manufacturer's solution for 500 W+ modules, it launched end of June (see LONGi Officially Enters 500W+ Club). Besides power, there are several other important aspects that can help reduce BOS costs such as the module size, the current handled by the inverter, the voltage of the module, efficiency and compatibility of the module with the mainstream BOS components. LONGi said it has taken all these aspects into consideration when designing its Hi-MO5 module series.
Technologies used for making Hi-MO5
LONGi is the key initiator among the companies that proposed M10 as the new wafer standard, an approach they've carried into designing the new Hi-MO5 series (see Group Proposes M10 As New Silicon Wafer Standard Size). According to Gonzalez, the reason for pinning down on the 182 mm wafer size is production feasibility, low production costs – as this requires a minimum in modifications of the processing tools, compatibility of electrical parameters with the mainstream BOS and panel dimensions and, therefore, logistics. LONGi is employing gallium-doping technology to reduce PID related degradation. Banking on this doping technology, LONGi promises to keep the first year degradation below 2%, while the actual value is about 1%, says Gonzalez.
Hi-MO5 uses PERC as the cell level technology platform. The other technologies the module features are: half cut and MBB using 9-busbars. The interconnection process is done using LONGi's proprietary Smart Soldering technology. The solution employs a segmented triangular ribbon, which is a special ribbon with triangular and flat sections. While the triangular ribbon maximizes the reflection of sunlight compared to flat or round wires, the flat section allows low stress soldering and helps in reducing the cell gap to 0.6 mm. Gonzalez presented a comparison of LONGi's segmented ribbon with flat and circular ribbon in terms of stress during the thermal cycling. "Our technology reduces the stress on the cell by 20%," said Gonzalez. All these approaches collectively enable the modules to attain an efficiency of 21.1%.
Layouts & variants
From a layout perspective, the Hi-MO5 series comes in two options—72 (eq.) half cut cells with up to 540 W power and 66 (eq.) half cut cells with a power range of 485 to 500 W. Both the module types are offered in monofacial and bifacial variants. The latter always comes with a framed 2 mm dual glass configuration. The bifacial module with frame attains a mechanical load of 5,400 Pa, and the frame not only offers additional protection during the handling and installation, it also makes the module compatible with different clamping solutions.
Advantages for end customers
One of the interesting aspects of the Hi-MO5 series, according to Gonzalez, is its dimensions. The 66-cell variant has a height of less than 2.1 m, which is close to products based on G1 wafer format, while the width is about 1.13 m, and still the panel can reach close to 500 W. The 540 W module, on the other hand, has the same width as the 500 W module, but its height is slightly more at 2.25 m. The most important attributes of the Hi-MO5 series are the current and voltage. The module current of about 13 A can be managed by any inverter in the market, even considering the bifacial gain, explained Gonzalez with an example. For a site with albedo of 35 to 45%, the bifacial gain is about 10 to 15% corresponding to a current of about 15 A, which stays within the threshold of the leading string inverter brands. However, modules based on 210 mm wafers in half cell configuration have a typical rated current of 18 A, which the mainstream string inverters can hardly handle, said Gonzalez. In terms of voltage the 72-cell (eq.) module has a Voc of less than 50 V, which enables connecting about 28 panels in a string, that helps in reducing BOS costs compared to modules based on 210 mm, especially when using mainstream inverters, according to Gonzalez. Both the models of the series are suitable for both 1P and 2P single axis trackers. However, Gonzalez underscores that the compatibility of the 72-cell variant with the 2P tracker has to be evaluated based on the mechanical load requirement of the specific site. Circling back to the mainly promoted advantage of BOS cost savings, based on a simulated installation in China, Hi-MO5 can save up to $1.2/W compared to a 410 W module on BOS costs, he said.
The presentation was followed by a Q&A with the conference attendees, which we have listed below (selected questions, edited & summarized):
Question: Can you elaborate on your expansion plans; where do you stand especially on the module side and what is LONGi's path heading into the future?
Juan Carlos Gonzalez: The aim is to have a capacity of 35 GW on modules and around 70 GW on wafers, of which 12 GW is planned for Hi-MO5. We want to promote mono PERC half cut technology based on bifacial solutions, which will be the main driver for us to reduce the LCOE.
Question: What was the rationale behind you choosing micro-gaps versus overlapping of cells?
Juan Carlos Gonzalez: In the beginning, I would say in 2018, we did think of developing an overlap solution, but in the end we need to think about reliability. On our part, we think the solution is still not mature, as the overlap solution is not well proven yet. If you make overlapping with shingling for instance, you need to cut the cells many times, like five to six times. So, you are increasing the cost during the production and somehow impacting reliability. The chances of cells cracking are higher with overlapping, a risk we would not like to take since it's a fairly new technology. While you have some advantages with overlapping—lower impact of hotspots or lower currents for instance—, on the other side you have a higher voltage and also compromise on reliability over time due to expansion and contraction of the lamination during the lifetime of the panel. So for the moment, we are still relying on reducing the gap up to 0.6 mm. Below this level would be 0.3 mm, which might lead to touching of cells' poles following current practices.
Question: That takes care of the shingling part. How about Tiling Ribbon?
Juan Carlos Gonzalez: Tiling Ribbon for us does not bring much improvement since we have a better control in production on quality and reliability with the standard solution. We see some risk in terms of long-term reliability with the tiling solution as well, and that is the reason why we are not considering this solution right now.
Question: We have heard from other presenters that they expect much larger modules to hit the market, and they are already using 210 mm wafers. Taking this into account, what are LONGi's plans, given LONGi is the master of wafers?
Juan Carlos Gonzalez: As you can see from the presentation, our plans are to work on M10 solutions, i.e. 182 mm, for all the reasons I mentioned before. From a logistics point of view, it allows you to increase the power density per container. Another important thing is inverter compatibility, because with the larger wafer size, you are increasing the current by default. With the 210 mm wafer, you reach up to 600 W based on half cut, which means you are going up to 18 A. This is somewhat of a difficult task for a typical string inverter. You are somehow reducing the options you have in the market when you talk about the design of the installation. As for 210 mm, we can do it and it may be an option in the future. But for the moment, our solution to the market is based on M10, because increasing the size is not always a way to reduce LCOE. You have more power per panel, but you will install less panels per string. So in the end, you will not have a reduction in BOS reduction from an electrical point of view.
Question: There are also some questions regarding reliability in general for larger modules. So with the larger dimensions, is there any unwanted bending or microcracks? How is the static load? And can you provide any background on certification?
Juan Carlos Gonzalez: Our solution, for example the bifacial, is based on glass-glass technology with frame. This frame, especially with the larger area, will lend consistency to the whole module. From a mechanical point of view, this panel can withstand up to 5,400 Pa. The glass-glass solution is especially helping the 500 W+ modules with a larger area as this solution is well known in the market to have better mechanical behavior than the lamination based on glass and backsheet. This has already been demonstrated by many tests. We have passed all the tests regarding mechanical load according to IEC.
Question: Markets such as India are price sensitive. Hi-MO5 are high quality, high power and high-performance modules. What are, in your view, the destined markets for this product?
Juan Carlos Gonzalez: We are aware there are some specific requirements for markets such as India. Thanks to these new developments, we are reducing BOS; in the event the panel has higher costs compared to other solutions, we have a positive impact on reducing the BOS.
For the moment, the plans are to keep the Hi-MO4 series with powers around 455 W either in monofacial or bifacial and implement the same to Hi-MO5 with monofacial and bifacial and make it available worldwide. There is no restriction on markets. It depends on client requirements rather than us.
TaiyangNews: Thank you for your presentation at the TaiyangNews 500W+ Solar Module Conference.
The LONGi Solar presentation of Juan Carlos Gonzalez can be viewed on the TaiyangNews YouTube Channel here.