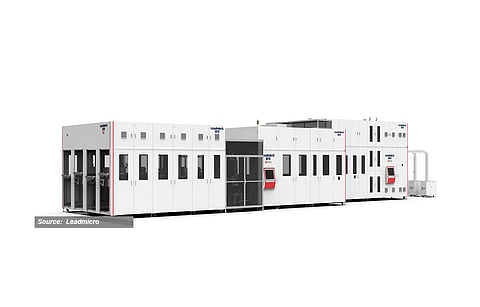
ALD systems were the first to facilitate aluminum oxide deposition for PV. The fundamentals of ALD can be found in our earlier PERC reports, e.g., PERC Solar Cell Technology 2017 Edition. The ALD reactors function on the principle that alternate dosing of the precursor, which is trimethylaluminum (TMA) and water vapor serving as oxidant, is accomplished in the same reactor chamber. While a few companies did tweak this fundamental principle by making them spatial and truly inline, they are currently commercially inactive. We have ALD system data from 3 companies for this survey – Leadmicro, Ideal Deposition and Semco.
Leadmicro has played a pivotal role in facilitating PERC's entry into high-volume production. Its ALD solution is both low cost and high throughput. One of the main obstacles for batch ALD was wraparound on the front, similar to LPCVD in TOPCon. In our previous article we discuused about LPCVD and PECVD depositon tools from various equipment suppliers (see Deposition Tools For TOPCon Solar Cell Production). However, depositing ALD on top of the front SiNx layer has alleviated any risk of forming inversion layers. Leadmicro has switched to ozone, replacing water as oxidant, making the process more effective as a result. The industry has received the technology very well. For this survey, we have received data for Leadmicro's latest model, KF20000S, a thermal and time-based ALD system. The tool is a tube reactor, and 4 tubes are integrated into the reactor shell. Each tube can be loaded with 2,880 M10 wafers. The company, however, has not provided several details of its system, including the wafer size at which it delivers its rated throughput of 23,000 wafers per hour.
Ideal Deposition has developed a hybrid platform that combines the best of all deposition techniques, specifically spatial ALD and inline PECVD. The system closely resembles the remote plasma inline PECVD tools. Unlike the erstwhile spatial ALD tools, which operate at atmospheric pressure, Ideal Energy's ALD system works in vacuum. While vacuum pumps make the tool relatively more expensive, this low-pressure deposition not only improves the reliability in mass production, but also eases the integration. The wafers are processed in a carrier that moves through different reaction zones to achieve the deposition on a single side, similar to spatial ALD systems. According to the company, this hybrid platform combines the high efficiency potential of ALD with PECVD's operational benefits. The approach of placing wafers in carriers reduces possible breakage. When compared to batch tools, which have a better price proposition and smaller footprint, the technology department of Ideal Deposition claims that its hybrid platform results in better thickness uniformity and quality of the aluminum oxide film. As a result, both the yield and efficiency are better. Ideal Deposition's inline tool platform is flexible in terms of the ability to add further process chambers depending on the required throughput. In fact, the iALD-IV, the lone model the company has provided data for in this current survey, can be opted for with up to 3 chambers. It can process wafers with edge lengths from a lowly 156 mm up to 230 mm. It is quite easy for the inline batch systems like Ideal Deposition's to process different wafer sizes as this mainly involves changing the carrier. The carrier of the tool has 88 pockets to accommodate G12 wafers, while the slots increase to 108 with M10. The ALD tool has a rated throughput of 12,800 wafers per hour for the G12 format, while it increases to 15,500 with M10. These throughput figures are assuming a film thickness of up to 5 to 8 nm.
Semco has provided data for the ALDOR 5000 series, its spatial ALD system used for depositing aluminum oxide. The system has been available since 2021 in both M10 and G12 versions. It has 2 process chambers and has a maximum throughput of 14,500 (M10) and 10,500 (G12) wafers per hour. The ideal film thickness of 6-8 nm is recommended to achieve good passivation quality.
The article is an excerpt from the TaiyangNews Market Survey on Solar Cell Production Equipment 2023, which also includes detailed product specs and can be downloaded for free here.