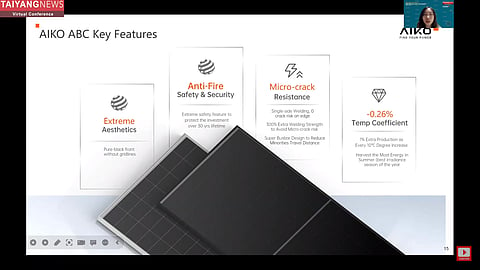
AIKO Solar, a well-known cell maker that has branched out into the supply of modules, has been introducing a series of high-efficiency modules based on its ABC module series, which stands for All-Back Contact.
AIKO boasts an overall 61 GW of annual cell production capacity and its entire 25 GW of module production capacity is marked for ABC. At the TaiyangNews annual flagship event, High-Efficiency Solar Technologies 2023 – Today, Tomorrow And Beyond, MA Jiayu, Product Manager of AIKO Solar, presented the key features and benefits of the ABC product range.
Low cost, high performance
AIKO began with the development of its back contact cell architecture called ABC in 2021 and attained an efficiency of 26.5% and commercialized the technology with a module efficiency of up to 24% during 2022–2023. Indeed, the company has held the #1 rank for the past year (since March 2023) in the TaiyangNews Top Modules list, which catalogs technically advanced and high-efficiency commercially available solar modules from leading suppliers.
The key features of the ABC technology, according to Jiayu, are enhanced optical absorption, unique rear side passivation and low-cost silver-free metallization. Due to the absence of any metal grid or busbars on the front side, which is inherent to any back contact cell architecture, the ABC cell has a very low visible light band reflectance of 0.6%. This value is 90% for areas covered with silver electrodes for the cell architectures of traditional art. However, the coverage of standard cells with silver electrodes and busbars also represents only a fraction. Thus, although not significant, ABC boasts of better light absorption, which is reflected as an increase in short-circuit current.
The next aspect is the metallization based on copper plating. The patented rear side copper plating design lowers resistive losses of the cell by 60% compared to the traditional front metal grid finger and busbar design. Thus, ABC technology can virtually eliminate resistive losses without impairing the optics of the solar cell, according to Jiayu. He further emphasizes that apart from the savings on silver, plating-based metallization also enhances reliability as silver-based metallization involves high-temperature processing.
Passivation engineering is an equally critical aspect. While the ABC cell architecture has a passivation scheme on both sides, the rear surface passivation is key, as contacts of both polarities are present on the rear side. Jiayu characterizes it as a unique Bi-Pole passivation, resulting in a low surface recombination of about 2 fA/cm2, resulting in "industry leading" open-circuit voltage of 746 mV.
Beyond power
In addition to the above cell-level advantages, the ABC product series features superior module attributes including pleasing aesthetics, fire safety, micro-crack resistance, and a low temperature coefficient. The design, characterized by an all-black color due to the metal grid-free front surface resulting in pleasing aesthetics, is well suited for residential rooftop installations. Its temperature coefficient of 0.26% results in better power yield; for example, about 4% more than PERC and 2% more compared to TOPCon products at a high NOCT of 75°C.
With regard to hotspot benefits, Jiayu presented TUV's hotspot testing results for its ABC modules in comparison to TOPCon and PERC. The results indicate that ABC modules demonstrate a lower hotspot temperature range of 90°C to 110°C, compared to higher hotspot temperatures observed in TOPCon at 150°C and 160°C for PERC. This lower hotspot temperature contributes to the modules' reliability, reducing the risk of issues such as backsheet yellowing, power degradation, and potential fire hazards.
In addition to these features, Jiayu elaborated on 3 specific process improvements designed to bolster the micro-crack resistance of ABC modules. First, the inherent single-side soldering of the ABC modules mitigates stress at the cell edges. This stress is typically inherent in the conventional cell stringing process, which routes the ribbon in a Z-pattern from the top of one cell to the bottom of the next, increasing the risk of micro-cracks. Jiayu claims that the soldering process used by AIKO for its ABC modules results in 300% higher soldering strength than traditional methods, further enhancing their resistance to micro-cracks.
The last significant enhancement is the adoption of a super busbar (SMBB) layout that includes 20 busbars on the back side. This layout is engineered to reduce the travel distance for minority carriers within the wafer, thereby minimizing energy yield loss in the event of micro-crack occurrence. Collectively, these process improvements are aimed at improving the durability and performance of the ABC modules.
Also bifacial
AIKO Solar currently has a total of 9 products in its product portfolio – 4 each for residential and C&I applications, and one product for utility.
Its Neostar series residential products are available in dual–glass and single–glass configurations, and are offered in 2 variants: the Black series with superior aesthetics and the White series with higher output power. These modules, with power outputs ranging between 440 W and 465 W, have an efficiency of up to 23.8%.
Its product class promoted for C&I applications is named Comet. This product has a power rating of up to 620 W, with up to 24% efficiency.
AIKO recently unveiled its latest utility-scale bifacial product series, the Stellar series, with a rated efficiency of up to 23.9% and 645 W power. This series features bifacial double-glass modules that achieve a bifaciality factor of 70%. Jiayu highlighted that the bifaciality of these modules is competitive with the standard TOPCon modules, which have an 80% bifaciality. He further emphasizes that the ABC module's capability to generate additional power from the front surface, AIKO's double-glass Stellar series can potentially outperform TOPCon modules in power generation. AIKO has successfully distributed its ABC modules to international customers across the Netherlands, China, and Germany.