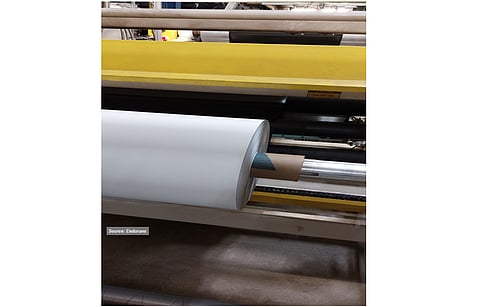
The innovations in the backsheet segment at their core are nothing but a mix and match of different polymer chemistries. This is what we have discussed in earlier stories on that topic (see Technology Trends In Backsheet Segment). As a matter of fact, it also has been the case with development of the backsheet historically. The fundamentals here have not changed. A backsheet typically consists of 3 different polymer layers, each serving a specific purpose, and these layers are laminated together.
However, coextrusion is somewhat disruptive for the backsheet segment as it challenges this traditional approach by bringing innovation in 2 areas – manufacturing and materials. First, it eliminates the lamination process by enabling the production of multi-stack layers directly from resins. In theory, the technology does support forming a multilayer structure using different polymers. In the current context, however, the coextruded backsheet typically employs a single polymer base chemistry (PP) but still consists of 3 layers. Similar to the different layers of a backsheet, each of these layers are tweaked to serve a different purpose, but the process is free from glue. That means the coextruded backsheets are free from inter-layer delamination.
There are 2 kinds of solutions from 2 different companies. The one from Endurans is a final backsheet product, while Borealis' resin helps manufacturers produce the backsheet in-house. However, PP is the basic polymer chemistry for both.
Borealis calls its solution Quentys, as part of which it supplies a polypropylene compound that enables backsheet makers to design their own films in-house using the coextrusion process. While standard polypropylene can be bought on the market in the form of homopolymers or copolymers, these compounds do not meet the requirements in their available form. To make it work, features would have to be added to make the films suitable for the backsheet structure. Borealis offers ready-to use polypropylene compounds specifically made and tested according to the requirements of the backsheets, so that manufacturers can run Quentys directly on their lines. This means that the backsheet maker does not have to go through the tiresome process of testing and trials. The resulting product has passed all of the tests required for backsheets.
As for the properties, PP is intrinsically UV stable, making it eligible for the outer layer of the backsheet. As for the core layer, when compared to the current state of the art (PET), PP's density is low. This means that the same performance attributes can be achieved with the use of less material, and the superior water vapor barrier properties – more than twice – are an added bonus. Apart from the technicalities, Quentys comes with two primary advantages. One is cost savings as a result of the superior performance of the PP and the coextrusion process itself. The other important part is sustainability. PP is highly recyclable, and is so at a very large scale. Quentys, being a mono material, eases the recycling process, resulting in higher yields. While Borealis did not respond to our enquiry on the latest status update of its project, the company's renewable energy program manager Geir Kristian Johnsen did emphasize that the company is strongly committed to solar and would support the development of the solar value chain in Europe. All these product level details are equally applicable to Endurans' backsheet products as well. However, its business model is different in the sense that the company sells the final product directly to module makers and its products have started getting good attention. The start of the journey for Endurans was not easy, as the customers often confused the failure of Isovoltaic's AAA backsheet – which comprised a completely different material stack as that is used by Endurans – with the failure of coextrusion as a process, thus Endurans had to be selective with its clientele (see Endurans Solar's Imco Goudswaard Calls For Using Sustainable Backsheets To Achieve Circularity).
One might remember the huge field failures of modules based on Isovoltaic's polyamide backsheets here. In addition, the company's legacy product – the B series that is still the part of the portfolio – consists of a polyamide layer. Again, since polyamide is regarded as the most disastrous polymer ever used in backsheets, it again reminded some manufacturers of Isovoltaic; "the tyranny continued for a long time," recalls Endurans Business Director Vivek Chaturvedi. "While our B series was born out of the failures of Isovoltaic, it took extreme amounts of effort on our part to explain how this product is fundamentally different," he adds. For its latest D series, the company removed the polyamide from the structure. Based on the test data collected for 5 years from labs and the field, both third party and in-house, the company realized that its B series is an overengineered product and the PP core of the backsheet is strong enough by itself. With a little tweak, it can stand on its own, providing the required UV protection without the need for the polyamide layer. "The irony was, our costs with polyamide were very high and were still answerable for the bad history of the polymer," says Chaturvedi. Thus, by eliminating the polyamide from the D series, not only did it become cost competitive, but the company does not have to defend its product anymore. In the end, the product has attracted the industry's attention and the company is very optimistic about the success of its product.
Coming to the coextrusion process, it has several advantages beyond reliability, cost and recyclability, according to Chaturvedi. It is much easier to set up a coextruded backsheet plant, benefiting from the vast capacities available from the food grade packaging films. However, the crux of the technology lies in the so-called "magic mixture." The polymer recipe is the IP of the company, and Endurans is developing and keeping the recipe an in-house secret. Borealis, on the other hand, is offering its knowhow to interested backsheet makers. In the end, this approach gives an extra dimension of freedom in product development compared to the laminated backsheets where the manufacturers have little control over the composition. "It also gives protection from a me-too product," says Chaturvedi.
The technology has also received support from a few Chinese suppliers as well, such as Lucky Film. The chemistry is not just limited to PP; it can also be applied to PO and PE, according to Cybrid. The benefits of common knowledge are: a certain price advantage, and elimination of cracking and delamination of backsheets. However, RenewSys' GCEO and Managing Director Avinash Hiranandani counters that interlayer delamination is not a common problem. "When there is no problem, then don't solve it," he says.
On the other hand, a common concern expressed by most of the backsheet suppliers (supporters of lamination) is the poor hotspot resistance. The rated power of modules these days is typically high, especially for the utility segment; in the range of 550 W to 600 W, going even up to 700 W. When such larger modules with high power ratings are integrated with these backsheets – PP, PO or PE – they cannot pass the hotspot test. It is really easy for delamination, bubbles and melting to appear, according to Cybrid's international marketing director Eric Yang. Thus, these backsheets are limited to smaller modules of lower power classes; e.g., 400 W. However, Chaturvedi argues that hotspot is not a backsheet issue but a cell issue. While we understand that one would like to avoid operating at high temperatures such as 156 °C, which is the melting point of PP, the backsheet is supposed to endure such undesired effects. To end this topic on a positive note, coextruded PP backsheets seem to have caught the attention of a large integrated PV manufacturer.
The article is an excerpt from the TaiyangNews Market Survey on Backsheets and Encapsulation 2022-23, which can be accessed free of charge here.