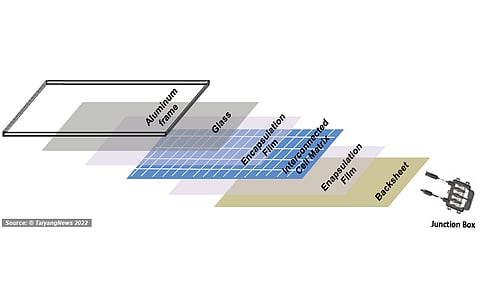
For beginners, a solar cell is the basic unit of a fully functional PV system. And multiple solar cells are interconnected electrically in series to form a matrix in order to reach a meaningful output power level. This interconnected matrix is encapsulated to protect the electrical circuit from physical damage and weather. The laminate is usually framed and provided with a junction box to collect the power from the cell strings. There are many different types of solar module technologies, but the most predominant one is crystalline silicon based, which is also the focus of this report.
Module manufacturing includes two key processing steps — interconnection and lamination. The process of establishing a series connection between the cells is what is called interconnection. The number of cells present in a module, however, can vary. Traditionally, modules typically consisted of 60 or 72 cells. Today, however, there are several additional varieties available in the market — 50, 54, 55, 57, 66 and 78-cell products — to make the modules suitable to specific applications and yield higher power. And with the emergence of the half-cell configuration, the cell counts have doubled.
Depending on the number of cells in a module, 10 or 12 cells are connected with copper strips, known as solar ribbons, into a string by running them from the front side of the cell to the rear of the adjacent cells. Typically, six of such strings are connected to form an interconnected cell matrix. This method also applies to half-cell modules, but the difference is two such matrices are built occupying the top and bottom portion of the module, connected in parallel. The interconnection process is very important as it governs the electrical properties of the module. Since a PV device is covered with a lot of metal, and being an outdoor device, the electrical circuitry has to be protected from environmental impacts.
A solar module is a rare commodity that comes with a typical performance warranty of 25 years or 30 years (in case of glass-glass), which is why it contains several protective layers. After the stringing process, the cell string matrix is placed in a lay-up station, together with the encapsulation layers and the front and rear-side cover.
The front layer is typically glass, which has to fulfill several criteria, one of which is protection against weather, serving as a barrier to moisture and water ingression and providing mechanical stability. Moreover, the glass has to exhibit very high transparency so that maximum sunlight reaches the solar cells embedded in the module. The glass is attached to the cell matrix by means of an equally transparent encapsulant, which provides cushion to the brittle silicon cells from any mechanical stress while also serving as an additional moisture barrier (see: Solar Is Everywhere).
EVA is still the most common encapsulant today, while other materials, like polyolefins, are also preferred, at least on the rear side of the glass-glass bifacial modules.
For most modules, a backsheet serves as the rear protection layer, mimicking the role of glass with none of the optical features required at least in the classical sense. However, glass is also evolving as a strong substitute. The backsheet provides electrical insulation and offers protection from moisture ingression and UV stability. The cell matrix with glass, EVA and backsheet is 'baked' together in a laminator. Finally, an aluminum frame is usually added in a framing station to protect the module from mechanical damages during transportation, handling and installation. The rear of the solar module is fixed with a junction box to extract the generated power. The last production step takes place in a solar simulator that measures the power rating of the PV module.