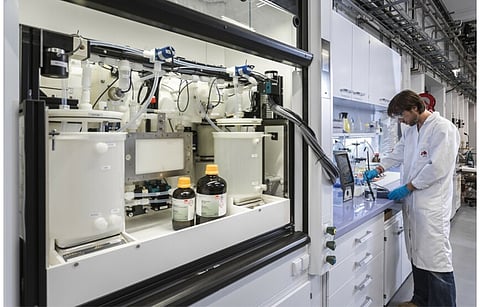
A consortium of industry players and researchers believe it is possible to reduce water consumption by up to 79% and up to 84% for wastewater using circular water strategies for solar cell manufacturing. This means that solar cell production is feasible in areas with less water availability, according to the group.
This is the crux of a study conducted by researchers from the Technical University of Berlin, Rena Technologies GmbH, and the Fraunhofer Institutes for Building Physics IBP and for Solar Energy Systems ISE.
The team introduced 2 different strategies, namely reuse of low contaminated wastewater (LCR) and the so-called Minimal Liquid Discharge (MLD) approach, in which certain residual materials are recycled and used elsewhere. For instance, etching solutions left over from solar cell production can be used in cement production.
These strategies were used in a comprehensive model of water flows created for a PERC solar cell factory with an annual production capacity of 5 GW. Their analysis covered water consumption, wastewater, and material flows to reach the conclusion.
"The results of the MLD scenario show that savings of up to 80 percent in the freshwater demand and in the wastewater can be achieved in the solar cell production factory modeled," said Jascha Reich, second lead author of the study and researcher at the Technical University of Berlin. "With the LCR approach, savings of up to 40 percent can be achieved."
According to them, these results are also interesting for factories with heterojunction (HJT) or TOPCon cell production, or even those that are to be converted to produce these technologies.
The team claims this would lead to slight savings in overall costs while reducing the risk of a factory shutdown due to water shortages. The latter can lead to weekly costs of around €1.9 million.
Nevertheless, they do cite challenges for the implementation of these 2 approaches, in terms of the need for additional land for the installation of water recycling units, and local availability of buyers of byproducts to minimize their transportation, among others. At the same time, the quality and purity of the byproducts should meet marketability specifications.
The study with the title Circular water strategies in solar cells manufacturing has now been published in the Solar Energy journal.