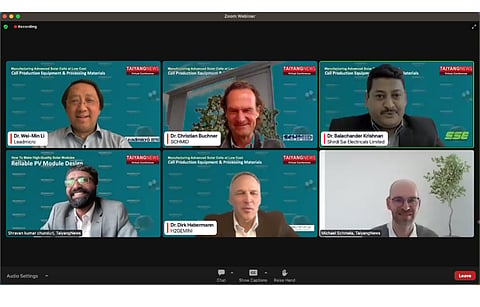
As the global solar PV industry brings in new trends every now and then, be it high efficiency modules or large format ones with different permutations and combinations to bring down total module cost, solar PV cell production equipment makers have been quick to keep pace with the changing times.
At our 1st solar Cell Production Equipment and Processing Materials Conference on February 28, 2023, TaiyangNews brought together various stakeholders from the solar cell production space to understand the processes behind manufacturing advanced solar cells at low cost. The subject becomes all the more pertinent as cell makers adapt to emerging technologies as heterojunction (HJT) and TOPCon, among others.
As the keynote speaker for the conference, the Chief Operating Officer (COO) of Indosol Solar, the special purpose vehicle (SPV) of one of India's Production Linked Incentive (PLI) tranche-I winners, Shirdi Sai Electricals (SSE), Dr Balachander Krishnan shed light on the selection criteria for key cell production equipment.
He mainly considered tunneling oxide, polysilicon application and subsequent doping providing a deep analysis of available approaches – thermal oxidation, PECVD, ALD and wet-oxide – for tunneling oxide and LPCVD, PECVD, APCVD and PVD for postdeposition along with the doping option of in-situ and ex-situ.
According to Krishnan, thermal oxide tool passivation is excellent with lower COO compared to PECVD. Though the jury is still out on deposition technologies, LPCVD and PECVD being the main contestants, both having their own set of merits and limitations. As for doping, especially when the choice of deposition technology is LPCVD, in-situ has lower COO over the extremal doping, he explained.
Giving example of SSE's own strategy of going in for all levels of PV production, including 2,000 ton per day or 10 GW (TPD) solar glass capacity, Krishnan said India needs to learn from China to go in for production for the entire value chain to have the ecosystem in place and be successful, instead of just focusing on module manufacturing like Germany did in the past.
A startup in the PV manufacturing space, SSE targets 80,000 ton per annum (TPA) or 20 GW production for metallurgical silica, 60,000 TPA or 20 GW polysilicon, 15 GW ingots/wafers, and 10 GW cells and module capacity each (see 4 GW Integrated PV Manufacturing For India).
On the lines of the PLI, Krishnan suggested the Indian government to expand manufacturing support to equipment production and bring in Equipment Linked Incentive (ELI).
Chinese solar cell equipment producer Leadmicro's Chief Scientist Prof Boachen Liao spoke about realizing reliable passivation mechanism for p- and n-type silicon substrates while presenting the company's PERC/TOPCon turnkey solutions with key deposition tools ALD/PEALD/PECVD.
Liao shared details of the company's own turnkey solutions as well as the development progress of the key deposition equipment from the house of Leadmicro. The latest one is 3rd Gen ZR5000 PECVD/PEALD system used for rear passivation stack in the TOPCon process flow. What's unique about this tool is that it features a patented integration technology that integrates both PECVD and PEALD into one reactor tube.
For TOPCon the company is mainly providing two different solutions; applying the tunneling oxide either by PECVD or PEALD, while the polysilicon deposited and doped in-situ with PECVD in both the cases. The solutions are backed with GW scale real time production data from Tongwei and Suntech, the respective buyers of these technologies from Leadmicro. Both the solutions have attained 25% average mass production efficiency of 25%, claims Liao.
GM Vacuum Coating Product Line at Chinese laser solutions company Hans PV, Wang Zhenhua discussed the role of thermal processes and use of laser technology in solar cell production. The company offers wide range of production tools – diffusion furnaces supporting boron as well as phosphorus diffusion, PECVD, LPCVD and last systems for various applications. The diffusion furnaces and PECVD tools of the company feature active air cooling that reduce the cooling rate and improve temperature uniformity.
While Zhenhua presented the unique features of each type of deposition and thermal processing tools, most interesting is the laser-based boron selective emitter for TOPCon cells, which is also a hot topic now. The process results in sheet resistance delta of 30 ohm/sq and a reflectivity change of above 1.5%. the tool uses four lasers and eight stages in a single line to maintain a high throughput of 8,200 wafers per hour, referring the 132 lines per a M10 wafer.
Vice President, BU Photovoltaics Schmid Group, Dr. Christian Buchner threw light on innovations in wet-chemical solutions for the state-of-the-art and advanced cell architectures. He batted for in-line processing of silicon wafers versus batch process claiming that in the latter process, breakage is 2 times higher.
Schmid has been using alkaline texturing process sequence since 2017 which it says provides up to 10.000 wph M12 throughput and uses no metal. It is suited for ultra-thin wafers, using full PVDF-PVC design with sophisticated thermal expansion management. The company offers wide variety of production tool platforms for various applications and most of these are integrated with a special feature.
For single side alkaline inline texturing system for example, Buchner claims the company's Rainbox pressure-less spray system uses 30% less water compared to batch process and ensures no shadowing and carrier marks like in cassette. The textured wafers out of the system have reflection of 12%. He added that the company's wet process solutions are equipped to meet process requirements for all advanced cell architectures – TOPCon, HJT and IBC. He also emphasized the importance of cleaning regime for all advanced cell architectures.
The CTO and Founder of H2GEMINI, a European PECVD supplier with a focus on HJT technology, Dr Dirk Habermann talked about HJT specific production solutions designed in Europe in the field.
Listing some of the challenges that HJT cell production faces technologically as surface damage, mechanical stress, problems related to wafer size flexibility, Habermann said his company uses tray-less deposition method of PECVD to ensure surface touch free automation. H2GEMINI too opts for inline automation concept along with smart automation.
Yet, he said, H2GEMINI has 60% less handling steps and automation which means less damage and less complexity hence significantly lower capex. Its HJT cluster line design has 50% less production area and needs only 9% of production area to have clean room environment.
Due to these factors, Habermann added that this European turnkey high efficiency heterojunction cell manufacturing technology comes at competitive price, at par with Chinese counterparts.
Chinese HJT solar cell equipment producer Gold Stone (Fujian) Energy Company Limited's (GS-Solar) GM HDT R&D Department Jinyan Zhang's presentation revolved around the development of microcrystalline HJT solar cells using 13.56MHz RF mass production equipment.
Zhang said 13.56 MHz is 'perfect' for large chamber PECVD equipment used for mass production of microcrystalline HJT cells. He also shared that the champion efficiency of microcrystalline HJT cells from mass production line is 26% for the company while that of bifacial microcrystalline HJT module is 24.46%.
The average efficiency of bifacial microcrystalline HJT cells made by one of its customers has reached 25.2%, Zhang added. Now it aims to increase its HJT cell efficiency for production line to 25.4% in 2023, eventually reaching 26.2% in 2026.
Listing the key developments in metallization paste solutions for TOPCon, silver paste maker DKEM's VP Technology and Marketing Kevin Nan called metallization innovation a key enabler for industrialization of TOPCon technology. To be specific, while the metallization on emitter is the efficiency accelerator, the rear is the cost controller.
DKEM uses p+ SE Emitter as a front side metallization that helps achieve lower contact resistance with a >0.3% efficiency gain combined with metallization paste modifications. The metallization of TOPCon's rear is complex, as the rear surface engineering varies significantly with choice of the deposition methods used for forming the tunneling oxide and poly as well as for the front side passivation. Nevertheless, the latest DK96T silver paste from DKEM with its wide process window supports all types rear surfaces.
According to him, with the integrated metallization solutions, the company is confident to lead the TOPCon efficiency progress to 26% by of this year, or early next year.
The 'world's largest' producer of LED-based solar simulator for solar cells, Wavelabs's Director Product Development Dr Sascha Esfelder discussed the high throughput IV-classification of high efficiency silicon solar cells.
Esfelder explained that measurement times < 50 ms for individual steps are necessary to achieve high throughput for high efficiency solar cell technologies as PERC/TOPCon/HJT. He suggested the company's LED based solar simulator RapidWave enables 'ultrafast measurements' faster than 30 ms.
Executive Panel
Moderated by TaiyangNews Head of Technology Shravan Chunduri, executive panel during the conference deliberated on solutions for setting up solar cell manufacturing globally.
SSE's Dr Balachander Krishnan stressed that while India is flooded with local solar PV manufacturing plans, the market is still taking baby steps towards a full-blown production market since here most module manufacturers are still in the process of switching from multicrystalline to PERC.
Indians would still like to work with PERC for a year or 2, according to Krishnan before switching over to TOPCon. However, the decision to go for TOPCon or HJT directly depends on the business model of the company.
However, Leadmicro CTO Dr. Wei-Min Li pointed out that going forward there will be more manufacturing capacity coming up locally in various regions as the basic cell structure can be modified easily by any manufacturer. However, what's significant is that Chinese companies are accelerating their shift towards TOPCon solar cell technology. Since China is the world's major supplier of PV production equipment, the window for the world to make the most of PERC is fast 'shrinking'.
Nonetheless, Schmid Group's Dr Christian Buchner argued that PERC and TOPCon basically complement each other, and both will have their significance for various markets in the near future as well. As technology improves further, over the next few years, PERC may just become even more competitive than it is now.
H2GEMINI's Dr Dirk Habermann believes while TOPCon is already evolving in various markets building on the advantages PERC offers, HJT will be the next big thing. It is an advanced technology and offers higher potential for a solar power system. Both offer a competitive advantage, but PERC will definitely disappear from the market as future unfolds.
All the panelists were unanimous in their opinion about China continuing its strong dominance as the world's largest supplier of solar PV products even in 2030, despite the fact that there will be diversification with various regions building their own manufacturing centers locally.