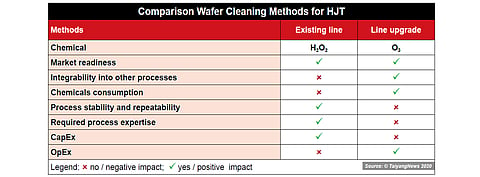
As with standard cell making, the heterojunction (HJT) solar cell process also starts with saw damage etching, followed by texturization. However, the process itself needs some fine tuning, requiring optimization of all the three process steps of saw damage removal, texturing and cleaning.
In wet chemical treatment, cleaning is perhaps the most important change required for HJT processing. HJT demands a specific cleaning regime involving several surface cleaning steps to remove organic and metallic impurities. The quality of the deposition—and thus the ultimate passivation—strongly depends on the cleanliness of the wafers, especially since the HJT process is carried out at low temperatures. With standard technologies, any contamination due to small metallic particles is eliminated via gettering, a high temperature process; this is not the case with HJT.
Optimized cleaning is required after the texturing stage and before removal of saw damage. According to an old technical paper from RENA, the oxidative cleaning process in pre-clean, meaning before the saw damage removal, circumvents any influence of organic contaminations taking place in the saw damage removal step. This is a precautionary step to maintain homogeneity of the surface that plays a more important role for HJT cells. The post-clean step, i.e. after the texturization, deals with the high requirements of surface morphology. It reduces the sharpness of edges and micro-roughness of the pyramids generated on the nano-scale, leading to better susceptibility for the deposition and passivation quality.
There are two cleaning methods that are largely followed—an ozone based process and a so-called RCA process using hydrogen peroxide.
RCA stands for Radio Corporation of America's cleaning method, pioneered by RCA laboratory chemist Werner Kern. The process employs a highly concentrated mixture of sulfuric acid and hydrogen peroxide. It is a two-step process—SC1 and SC2. The former focuses on the removal of particles and organic contamination by means of a heated alkaline mixture of hydrogen peroxide and ammonium hydroxide. And SC2 treats the silicon substrate with a mixture of hydrochloric acid and hydrogen peroxide at higher temperatures to remove metals. The SC1 typically is employed in the pre-clean step, while in the post-clean step SC1 is accomplished first, then the wafers are treated with a mixture of hydrofluoric acid and nitric acid before being subjected to SC2 cleaning. The final cleaning and conditioning step is done by HF treatment to generate a clean hydrogen-passivated surface prior to drying, which is common for both the cleaning approaches. RCA processing is kind of a standard in the microelectronics industry for cleaning. While the process, no doubt, is effective as well as robust, it is also expensive. In addition to hydrogen peroxide being very expensive as a chemical, the ensuing effluent treatment is also expensive.
Thus, the industry is seriously developing alternative cleaning mechanisms using ozone. As with RCA, the ozone-based cleaning regime is employed in both the pre-clean and post-clean stages of the wet-chemical treatment. The pre-clean process is typically accomplished with ozonized deionized (DI) water treatment. Post-clean is accomplished in two stages—cleaning the wafers with a mixture of hydrofluoric acid and ozonized DI water, followed by treatment with only ozonized DI water. The ozone-based cleaning process has a few advantages over RCA. While RCA uses strong acids and expensive hydrogen peroxide, the ozone solution poses no threat to the environment. Plus, according to a presentation by Xuemei Chen from Singulus at FZ Juelich's 3rd SHJ Workshop, the ozone-based process is also faster by 30 minutes compared to an hour for the typical RCA solution. Moreover, the cleaning performance is also better with ozone as it has a higher oxidation rate compared to hydrogen peroxide. Chen also showed the results of a research paper published by HZB Berlin, which compared cleaning processes based on RCA and ozone, showing good cleaning performance can be achieved. It demonstrated comparable to better values of lifetime and implied voltage attained with ozone solution compared to RCA. In fact, leading wet-chemical tool suppliers are promoting the ozone-based process.
For detailed information on wetchemical process and wafer cleaning methods in HJT cell production, please download and read TaiyangNews report on Heterojunction Solar Technology 2020, which can be downloaded for free here.
A comprehensive overview on "Wet Chemical Boost for High Efficiency Passivated Contact Cells" was provided by RENA Head of Technology Holger Kuehnlein during the TaiyangNews High Efficiency Solar Conference – the recording can be viewed here.