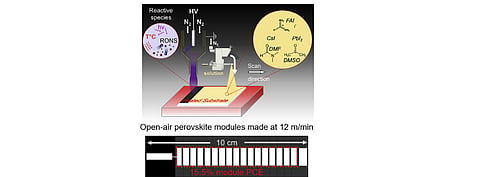
With an aim to demonstrate a rapid and scalable open-air processing route to fabricate perovskite solar modules, Stanford researchers developed a process called Rapid Open-Air Fabrication method for producing perovskites modules and published the latest results in Joule. The research group demonstrated perovskite deposition with linear speeds of 12 m/min without post-annealing combined with monolithic integration that resulted in a cell efficiency of 18% and module efficiency of 15.5%.
The process is shown in a brief YouTube video placed in the announcement on the Stanford website.
The application technologies such as slit die coating and ambient spray coating have the advantage in scalability, but these methods often require lengthy annealing times. To overcome the challenges with well-known application methods, the Stanford group has developed open-air Rapid Spray Plasma Processing (RSPP) that not only supports ultrafast deposition of the perovskite precursors, which are simultaneously exposed to plasma in linear processing sequence. The combination of reactive species and thermal energy produced by the plasma rapidly converts the deposited perovskite precursor into thin film, avoiding lengthy annealing steps. Another advantage of the RSPP – it improves the utilization rate of the precursor by several folds over the contemporary coating methods.
The apparatus consists of an atmospheric plasma post-discharge and ultrasonic spray nozzle arranged on a robotic arm in series. After spraying of the perovskite liquid precursor with ultrasonic nozzle on the substrate, in this case glass, the plasma gun simultaneously scans the spayed area. According to the latest results, the process is accomplished at a very high speed of 12 m/s. The approach uses clean, dry air as plasma gas, making the plasma process cost effective. The research group demonstrated "10x" carrier lifetimes and subcell Voc of about 1.06 V. The series connection in the module is accomplished with monolithic integration using single-source low-cost fiber laser scribing.
The Stanford researchers indicated that the process has high potential to reduce the cost quite significantly compared to incumbent crystalline technology to about $0.25/square foot. A typical 60 cell module with an area of 16 square foot is roughly price at $62, which translates it not $3.75/square foot.