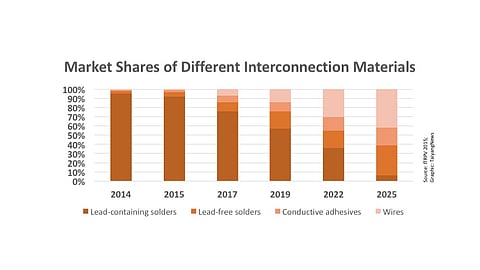
Compared to the previous 2 International Technology Roadmaps for Photovoltaic (ITRPV), the 2015 version has given a more prominent position to the interconnection section of module making. The 6th edition has for the first time discussed the anticipated changes in solar ribbon's solder composition, cell layouts with more busbars and new interconnection technologies.
"Green" ribbons soon?
As with metallization pastes, the roadmap anticipates lead free solders to gain market share over the next 5 to 7 years. However, eliminating lead from the solder composition is not as complicated as with metallization pastes. Solar ribbons coated with several different lead-free compositions are available. But these products typically require higher processing temperatures. The presence of lead promotes better solderability and its absence increases the melting point. Higher temperatures in the interconnection process enhances the risk of cell breakage. However, lead-free solders containing bismuth can compensate for the lead as for the processing temperatures. But lead-free solders often have higher silver content in order to facilitate better solderability, thus increasing costs of solar ribbons. According to the 2015 roadmap, the share of lead-free solders will increase from less than about 5% today up to 10% in 2017, and grow close to 20% in the following 2 years. In 2025, heavy metal free ribbons are expected to enjoy a market share of 35%.
Sticky solutions will work
Removing lead from solder is one thing, but alternate interconnecting approaches, such as employing conductive adhesives, can also contribute to free module making from heavy metals. Here, instead of soldering, which is the current state of the art technology for cell interconnection, a glue-like substance is used to establish the connection between solar cells and ribbons. Conductive adhesives are metal fillers loaded into a thermosetting epoxy base along with some additives, curing and diluting agents. As only curing is required to attach ribbons to a cell's busbars, conductive adhesives based interconnection is relatively independent from soldering composition. Thus, lead-free solders can be used without increasing the processing temperatures. Its capability to support lead-free module processing is just an example, but the inherent benefit of the conductive adhesives is its ability to be processed at low temperatures of less than 120 °C. This is especially beneficial for high-temperature sensitive applications, such as hetero-junction cells and thin film PV. The flipside of the technology – silver is the main constituent of conductive adhesives, which makes it expensive. Still ITRPV anticipates that 20% of the interconnections will be accomplished using conductive adhesives over the next 10 years, from a negligible presence in today's manufacturing. The roadmap expects conductive adhesives would be noticeable in module production from 2017 with a share of 5%, and then progressively become more prominent.
Wires are the future
Interconnection based on thin wires is yet another alternative to soldering. Leading production equipment makers Meyer Burger, Schmid Group and GT Advanced are offering solutions for wire-based interconnection, thought the methods employed by each of these companies are fairly different in details. A generic explanation of it this method: instead of 3 or 4 ribbons used to realize series connection between the cells of the modules, several thin wires are employed. The 6th roadmap expects that wire based interconnection would go from basically zero up to 5% in 2 years from now and eventually dominate the sector in 2025 with a 40% share.
The positive outlook for both conductive adhesives as well as using wire is based on the estimate that ultra-thin wafers become widespread in the future. These approaches have the inherent advantage of low temperature processing, which induces lower thermal stress on the wafers during the interconnection step and in turn reduces the breakage risk.
Either more or no busbars
In addition to these innovative new concepts, ITRPV also expects some developments in the standard interconnection process. One such recent advancement is an increase in the number of busbars, which is a topic touching the intersection of metallization and module making. While the metallization process is where the change is required, the implications of the shift take place in module making. The cell layout with 3 busbars is still common, but the 4-busbar concept is gaining ground. At recent fairs you could see almost every module maker exhibiting 4-busbar products. ITRPV expects the share of 4-busbar modules to approach close to 20% this year and 30% market by 2017, and remain at the same level for the following five years. By 2025, the share of 4-busbar modules is expected to reduce to 20%, while there will be even less 3-busbar modules around – only 15%. Cells with 5 busbars, which were recently introduced by German company SolarWorld AG, are also expected to follow the same trend. From a mere presence in 2014 and 2015 – which still seems optimistic – they are expected to attain a meaningful share of about 10% in 2019 and 15% in 2022, before they fall to about 12% in 2025. ITRPV has not looked into busbar concepts beyond 5, which makes sense; even 5 busbars are difficult to handle with today's machines and, moreover, hardly result in further cost savings due to increased complexity in production and potentially higher breakage.
The only cell layout that is projected to gain consistently is the busbar-less cells, which are required for advanced interconnection technologies. ITRPV believes it will grow from about 2% in 2015 – which seems also a bit too upbeat – to a 30% share in 2025, when it will have overtaken the traditional concepts.
Tools to become faster with new technologies
As for the developments at the tool level, the current roadmap anticipates a significant improvement in throughput for the interconnection process. The average capacity per tool is expected to improve by 20% and 40% over the current level in 2017 and 2019, respectively, mainly driven by the new interconnection technologies and back-contact cell concepts. However, in summary, the biggest thing that is expected to change in module manufacturing are new interconnection technologies, most likely the one employing thin wires.