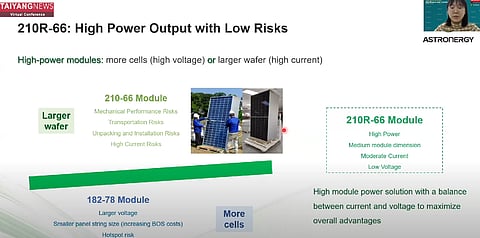
Building modules based on rectangular wafer formats is a hot topic in solar module manufacturing these days. This is facilitated by the fact that every PV module is built on sliced silicon substrates either before or after cell processing. Thus, rather than cutting a wafer or cell into 2 equal parts, dividing them into asymmetrical pieces still enables them to meet the required module dimensions and corresponding power ratings for different applications. This also gives module makers the freedom to achieve the voltage and power requirements for a specific application by selecting the size and the count of cell strips wisely.
Companies are also finding their own sweet spot for a wafer dimension. A few companies are even adopting more rectangular wafer dimensions than one to build modules for different applications. Astronergy is a case in point. The company is using dimensions of 182 x 210 mm, commonly referred to as 210R, for the modules for utility applications, whereas it uses 182.2 x 191.6 mm, known as 191R, for products for DG applications.
Recently, the company introduced 2 new products: ASTRO N7s based on 191R, and ASTRO N7 using the 210R wafer format. Its current version of ASTRO N5 is based on the 182 wafer format.
At the recently concluded TaiyangNews High Efficiency Solar Technologies 2023 – Today, Tomorrow And Beyond, Zoe Shi, product manager of Astronergy, provided some insight into the value addition of these 2 products. In her talk, Shi also briefly spoke about the progress in TOPCon cell technology.
A glimpse of cell development
One important technology development with respect to TOPCon cells, which is being evaluated by nearly every manufacturer, is laser-enhanced contact optimization (LECO) metallization technology. Here, a bias voltage and strong light injection with high current density diffuses the silver paste into silicon to form an ohmic contact. The approach has increased the cell efficiency by 0.3% in the lab over the base value of 26.1%, according to Shi. On the other hand, the company is already implementing the laser-doped selective emitter to reduce contact resistivity. As it is well known, the application of selective emitters creates a heavily doped metal contact region and a lightly doped non-metal contact region with reduced J0, metal that ultimately helps in increasing fill factor (FF) and Voc. In the end, the process resulted in a relative cell efficiency gain of 0.25% to 0.35% (not percentage points).
Mid-sized module for Utility
Coming to the main theme of Shi's presentation, Astronergy is promoting its flagship ASTRO N7 series glass-glass modules for utility applications. The module is built with 132 cell slices cut from 210R cells. The Astro N7, with its power rating of 605 W, places itself nicely between the products built with M10 and G12 wafers, according to Shi. In comparison to G12 based modules, which have a higher length of 2,465 mm, this G12R based product offers better reliability, especially with improved fixed and dynamic mechanical load performance. The module's size, conforming to the agreed standard for module dimensions for mid-format modules, i.e. 2,382 x 1,134 mm, eases the transportation, unpacking and handling during installation. The given dimensions also helps increase the cargo container loading capacity by 4.3%, equivalent of 18 kW of additional power per container or a savings of 0.04 c$/W in sea freight cost, compared to M10 based products.
There are other benefits in this line comparison as well. The ASTRO N7 apparently has higher power resulting from an increase in active area by 15.6%, while the cell count remains the same. Increasing the number of cells to 156 slices (half cut M10) can match this power. However, the high number of cells directly increases the module Voc, which reduces the number of modules per string, increasing BOS costs. The lower Voc of ASTRO N7 modules, given as 51.6 V, compared to the products based on 191R as well as M10 based utility-scale modules, allow the connection of 2 additional modules in a string, meaning in a tracker with 3 strings, 6 additional modules can be connected, according to Shi.
The ASTRO N7 utility-scale module uses 16 busbars, which the company characterizes as Super Multi-Busbar (SMBB), which helps reduce series resistance, stress distribution, and finger defects. The module further features 3-layered light redirect film (LRF) between the cell gaps. The film is built with a highly reflective good weather–resistant aluminum alloy, a low shrinkage PET film layer, and an EVA layer.
Modules for DG applications
For distributed scale application, Astronergy adapted the ASTRO N7s series on the 191R wafer format. It has a rated power of 445 W and 22.27% efficiency. The module, measuring 1,762 x 1,134 mm, meets the requirement of being less than 2m2 for DG applications. On the other hand, it has 5.7% higher active module area compared to M10–based products; for example, the ASTRO N5 series. ASTRO N7s is built with an innovative gapless interconnection technology implemented on busbar–less cells. The combination of this special metallization and interconnection method reduces microcrack risks and saves silver paste cost, according to Shi. The elimination of busbars from cell metallization is a self-explanatory saving in silver. As for interconnection, Astronergy is adapting the tiling film method, in which the laminated interconnection ribbons are placed precisely over the solar cells and contact between the cell and ribbons is established during the lamination process, at below 150°C. Soldering at a lower process temperature with reduced thermal stress and filling up the cell overlap gap by tiling film effectively reduces cell microcrack risk, explained Shi.