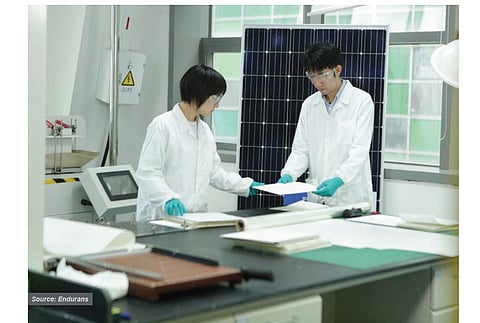
No doubt the backsheet segment is innovative and very dynamic. But these developments are rather limited to the polymer chemistry and finding new configurations in terms of the backsheet structure; regarding the manufacturing process, the segment is rather "old school." The majority of the backsheets in today's market are produced with lamination; procuring the different layers of films, mostly externally, and glue them together by means of lamination. Coating, especially when applied on both sides, is a step forward from the lamination method; however, the core film is still procured externally. Coextrusion, on the other hand, offers the ability to produce backsheets directly from resin. The beauty of the process is that it allows the stacking of multiple layers of different polymer chemistries, if needed, in one go. Not only does it simplify the manufacturing process, which has a high cost savings potential, the process is free from glue. That means the coextruded backsheets are free from inter-layer delamination.
There are two kinds of solutions from two different companies. Endurans from Holland is offering a final backsheet product. Then, Borealis designed its business model to operate a step above in the supply chain. The Austrian chemical company is supplying resin and encouraging backsheet makers to produce the backsheet, eliminating the need to procure the films externally. As for polymer chemistry, both are relying on polypropylene (PP) in mono material configuration, meaning the produced backsheet stack still has 3 layers, but each layer of PP is modified for a specific role. BISCHOF + KLEIN from Germany has also commercialized a backsheet product based on an all-Pp coextruded backsheet; but the company has not responded to the enquiry for our Backsheets Market Survey (see Variants Of Transparent Backsheets).
Borealis calls its solution Quentys and started promoting its solution in two configurations — a PP core layer to replace the PET alone and an all-PP based fully functional backsheet. While the customer can choose what is the best, highest cost benefit can be availed when choosing the co-extruded full PP-backsheet as it avoids any further lamination or coating steps, according to Borealis' business manager for solar, Alper Muraben. Borealis currently supplies a polypropylene compound, not the film itself, leaving backsheet makers in the position to design their own films from the Quentys compound in-house for use on their own production lines. While standard polypropylene can be bought on the market in the form of homopolymers or copolymers, this would not suffice for the requirements of backsheets. Based on long term knowledge and experience Borealis has developed multiple tailor made polypropylene products. According to Muraben, this not only requires a high level of polymer know-how, but also brings in additional costs with it. Borealis is offering ready-to-use polypropylene compounds specifically made and tested according to the requirements of the backsheets, so that manufacturers can run Quentys directly on their lines. This means that the backsheet maker does not have to go through the tiresome process of developing their own compounds. "It is a kick start for the backsheet maker when they want to introduce a new product line," said Muraben. The resulting product has passed all tests required for backsheets. The industry feedback about the performance of the backsheet in different tests is positive, according to Muraben. He quotes water vapor transmission rate, electrical performance and temperature index as examples (see Quick Rise In Backsheet Materials Prices).
At the backsheet supplier level, Lucky Film is in favor of the technology and the company estimates it to have a big application in next 3 to 5 years. The Chinese company is also working on a coextrusion project that is still in the development phase, while the products are expected to hit the market next year, while Lucky Film declined to elaborate on the details of the polymer chemistry it is working on.
Fumotech is yet another Chinese company that is in favor of the coextruded PP structure and is evaluating the technology. Referring to PP coextrusion, Jiang Wei from Fumotech's Marketing Department said that it is an effective way to reduce the costs, while underscoring the limitations in passing the hot spot test and lamination temperature as shortcomings. Fumotech is working on a coextruded PP solution but given the background of the company as a PVDF supplier, the business model behind the project is a secret, at least for now, as Wei would not provide any details.
Another strong proponent supplying coextruded backsheets for some time is Endurans; the company however is now mainly focusing on an all-PP based configuration. Each of the PP layers in the backsheet is designed with a specific purpose. The core layer, for example, is less sensitive to moisture compared to PET and the mechanical properties remain unaltered for longer durations, justifying its usage in extreme outdoor applications.
In addition to being cost-competitive with all traditional laminated/coated backsheets, including CPC, Endurans highlights the ease of end-of-life treatment with its product configuration, an often-neglected topic in price/cost discussions. Recycling fluoropolymer backsheets, whether through incineration, pyrolysis, or direct remelting, is technically difficult and thus costly. In contrast, the Endurans HP range is fully recyclable through the lowest-cost option of remelting. The company has been monitoring 9 solar fields in Europe and Asia since 2015 that have its backsheets installed, with zero failures reported so far, according to Endurans' global communication and branding lead Annet Hoek. "Our backsheets meet, and sometimes even surpass, the highest industry standards; the PVEL stress test is one example," said Hoek.
In addition to Endurans HP backsheets for mainstream modules, the company is also supplying a conductive backsheet under its Endurans CB brand that is targeted at high-end applications. The customer base for this product is currently in Europe and the US, while the company is working to expand into Asia as well.
The Text is an excerpt from TaiyangNews' recent Market Survey on Backsheet and Encapsulation Materials, which can be downloaded for free here.
An overview of the survey was presented during TaiyangNews Conference on Reliable PV Module Design. To learn more about the conference and view the presentations click here.