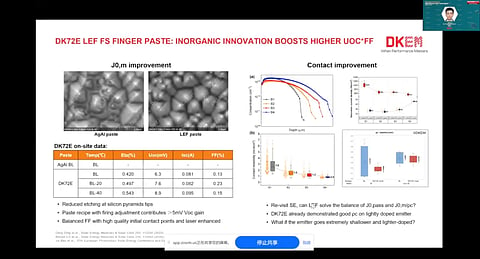
Metallization is one of the most important process steps in the processing of cell manufacturing, irrespective of the cell architecture. The process not only influences the performance of the PV device, metallization pastes, the process consumable of the step is also the key cost driver across cell processing. At TaiyangNews flagship event High Efficiency Cell Technologies Conference 2023 (Mike Guo, DKEM: Innovative Metallization Pastes), New Technology Development Director at the leading Chinese paste supplier, DKEM, Mike Guo presented innovative paste solutions of the company for TOPCon, especially for laser enhanced firing (LEF).
In fact, LFE is currently a very hot topic with in TOPCon processing with a promise to boost efficiency of TOPCon cell structure. While LFE is only related to the front side metallization, Guo presented the entire paste system that also consists of pastes for rear contacts and busbars that boost TOPCon efficiencies above 26.5%.
Before going into the details of his topic, Guo provided basics of the contact formation, which is the crux of metallization to attain the low contact resistivity and metal-included recombination rate (J0.m). While there are four different ways of contact formation, bulk silicon forming at direct contact with silver or/and silver crystallites are the two mainstream contact mechanisms that are responsible for different higher cell efficiency structures, especially that use fire through pastes.
On the front side of the PERC cell, which is n+ emitter, silver crystallite can be easily formed due to the silver ion's easy bonding with available electrons in n+ emitter. For TOPCon cell, in which the emitter is p+, the silver ion gets suppressed. To overcome this limitation, the current practice is to use silver-aluminum paste on the front side. Though the silver-aluminum paste solution improves contact resistivity, the formation of silver-aluminum spike sometimes results in higher recombinations. This can be explained due to the formation silver-aluminum spike at micron scale, which damages junction.
Alternate approaches using external carrier injection methods, like electro carrier injection and laser induced carrier injection, have shown to have improved contact formation. The latter, which is nothing but LEF, is widely evaluated currently in the industry. It involves subjecting the front contacts to laser treatment after firing. The process essentially decouples the metal contact recombination and contact resistivity..
The firing process controls J0.m while the laser process enables good contact formation, which put together mitigates bottleneck of using Ag-Al metallization paste in p+ emitter cells. The LEF process pushes the balance between the Voc and FF to a higher level, said Guo.
Front side paste DK72E LEF FS:
DKEM recently launched a LEF specific front-side finger paste called DK72E LEF FS, which, according to Guo, demonstrated good results compared to DKEM's silver-aluminum paste. In his presentation, Guo showed the SEM images for contact formed with both kinds of pastes, revealing that DK72E laser-enhanced metallization paste shows a significant improvement in the etching of silicon pyramid, especially at the tips. The reduced etching of the silicon pyramid indicates that the passivation layer is protected and leads to less junction damage, which helps in improving Voc.
Guo also presented DKEM's testing data that shows at standard firing conditions, the DK72E leads to a Voc gain of about 5 mV along with a slight improvement in FF. By reducing the peak firing temperature by 20℃ or 40℃ in LEF with DK72E LEF paste, a further 2 mV gain is realized without compromising the fill factor (FF). Thus, DK72E LEF paste shows good control on J0.m and allows a wider firing window, Guo emphasized. He further notes that the latest generation of pastes also opens optimization window for cell processing, especially for selective emitter. The pastes also showed a better printability; while the silver-aluminum pastes became challenging for screen opening below 13 µm. The DK72E LEF paste has shown a relatively better printability in narrower screen opening of 11.5 µm, also adopted by a few cell makers, according to Guo. The absence of aluminum content in the DK72E LEF paste improves the grid line resistance, which supports reduced laydown and fine line printing optimization.
Reliability
DKEM also tested the reliability of DK72E LEF, in which both in pressure cooker test at the cells level and damp heat test at module level showed better performance over the reference silver-aluminum paste. While acetic acid test results were not up to mark, Guo calls industry to reevaluate the acidic acid treatment conditions, given all other test results are quite optimistic.
Rear side pastes DK95E LEF RS:
Adapting LEF on front side also requires paste optimization for rear side. For the rear side finger metallization in laser-enhanced process, DKEM has launched their new DK95E LEF RS paste. This new pastes carries forward the wide process window capabilities of previous DK93E, which is compatible with wide varieties of rear surface engineering of TOPCon cell including technologies used for tunneling oxide, polysilicon, aluminum oxide and texturing.
The DK95E RS paste also supports TOPCon cells with ultra-thin polysilicon layer of 80 nm. Following the standard firing process, the size of silver crystallite can range up to 100 nm that can damage polysilicon layer of less than 100 nm. The DK95E paste, featuring optimized organic system, in combination with LEF on front enables precise control on silver crystallites, thus facilitating the use of thinner polysilicon layers. "DK95E paste series demonstrated mass production with 80 nm thinner polysilicon layer at the customer site," shared Guo.
Busbar pastes DK82E:
LEF process requires lower firing temperatures for attaining higher efficiency, which results in lower adhesion of busbars on front and rear. Addressing these concerns, DKEM has launched new LEF compatible front and rear busbar pastes called DK82E. This new busbar paste showed good adhesion and ageing adhesion even with 60℃ lower peak firing temperature, enlarging the firing window for higher efficiency gain, according to Guo. Also, the ultra-floating design of the busbar paste showed lower recombination and low busbar-finger interruption reducing the busbar dark EL issues.
Paste for Bifacial Poly TOPCon:
Not just the state-of-the-art TOPCon technology, DKEM is also working on the Bifacial Poly TOPCon cell which is expected to be the next generation TOPCon cell with respect to the passivation technology. The approach extends the TOPCon architecture, which is currently adapted only on the rear side, on to the front as well. Here, n-Poly on the front and rear side p-Poly raises new requirements for metallization pastes.
For the front side n-polysilicon, due to the texturing surface, the passivation layer is more easily etched through pyramid peaks. It causes high J0.m compared to polished rear side. Also, considering the parasitic absorption in polysilicon, the cell makers prefer thinner n-poly, thus there is a need to control the width of the poly finger. This also necessitates control of the size of silver crystallite, especially at the pyramid peaks. Narrowing the poly fingers also requires narrow finger grid lines, which puts a new requirement for the n-poly finger paste.
For the rear side, considering the p-poly is much thinner at 300 nm than the p+ emitter, which with selective emitter (SE) is up to 2 microns and without SE is around 800 nm. Then, the rear surface is also polished, topped with several stacks of deposited layers. All these raise the bar for rear contacting paste as well. For the bifacial poly-based TOPCon structures, DKEM says it offers a total package – DK95B for the front side and DK73K for rear. The paste system showed more than 0.1% efficiency benefit compared to the solutions from other pastes vendors for this structure.