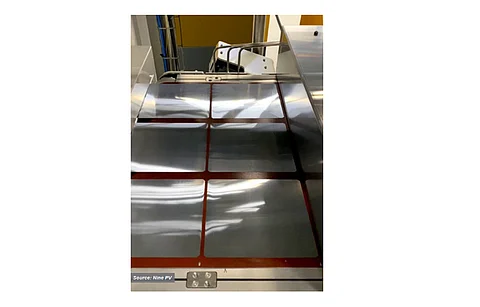
Surface preparation steps in a cell processing such as SDE and texturing are typically accomplished with wet-chemical benches (see Tools For Solar Wafer Texturing). And there have been quite some improvements in this traditional way of texturing the wafers, such as improving bath lifetimes or reducing texturing time (see Several Improvements In Wafer Etching).
However, there exists an alternate method called dry-etching. TaiyangNews Market survey on PERC cell production equipment lists 2 such products from Nines Photovoltaics ("Nines PV") that are based on atmospheric dry etching. As an alternative to the wet-chemical solutions, be it to realize SDE or texturing, Nines PV has developed a proprietary process called ADE, which stands for Atmospheric Dry Etching. The company has been developing this process since 2010. And what makes this technology unique is that it accomplishes dry texturing at atmospheric pressure using fluorine (F2) as the etching gas. This eliminates the need for vacuum and plasma – both key ingredients and cost drivers in typical dry etching technologies, emphasized Nines PV's CTO Laurent Clochard. He clarifies that the technology has no special adverse impact on the environment. The thought of fluorine as an etching gas itself rings alarm bells about greenhouse gases. However, Clochard underscores that the molecular fluorine used by Nines PV scores a zero against the commonly used SF6 that has high global warming potential
The TaiyangNews Report on TOPCon Solar Technology covers Nines PV's technology in detail, as its main promoted application is for silicon etching, to remove wraparound in TOPCon application to be specific, but it is not limited to TOPCon. The tool, when it was introduced in 2017, was mainly designed for texturing, specifically for multicrystalline, in which the gains in reflection with ADE are way higher than what can be achieved with the state of the art wet-chemical solutions. However, with the market shifting to monocrystalline, Nines PV also shifted focus to mainstream PERC and other advanced technologies. In terms of benefits it brings to PERC, especially with texturing, it is a single sided process, meaning the process alleviates the need for rear polishing. On top, "We remove less silicon than an alkaline process to achieve lower reflectivity facilitated by the sub-micron scale texture," said Clochard. "We are talking something like 200 to 300 nm," he added. The process is also selective, meaning it does this without disturbing the underlying emitter profile.
Nines PV is currently operating a pilot line at its facility in Dublin and has partnered with Fraunhofer ISE for cell process development, having also supplied an R&D-scale system. The company is now ready with the production-scale platform, which is offered in 2 variants – ADE-3000 and ADE-6000. The latter processes wafers up to a size of M4 in 6 lanes and M6 to G12 in 4 lanes, and with a rated throughput of 12,000 and 8,000 wafers per hour, respectively, in a footprint of 12 m2. The number of lanes is exactly half in ADE-3000, so is the throughput. The company is also willing to supply an R&D-scale system with a single lane of transport.