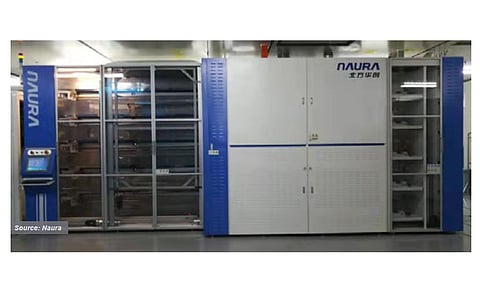
Diffusion is the most predominant technology employed for the solar cell's emitter formation, typically accomplished in diffusion furnaces. Fundamentally, there are 2 variants of diffusion furnaces – conveyor-based inline tools and batch type tube furnaces, the latter being the current state of the art.
For PERC, which is based on p-type wafers, phosphorus is used as the dopant to form n-type emitters. Batch type tube furnaces have been the workhorse for diffusion. These tools consist of a stack of quartz tubes serving as the processing chamber. The wafers to be processed are placed vertically in quartz boats and are then loaded into the quartz tubes. These furnaces support processing temperatures up to about 1,050 °C. For doping p-type wafers with n-type impurity, liquid phosphorus oxychloride (POCl3) is used as the phosphorus precursor, delivered through a bubbler. Colloquially called "POCl" diffusion, this process works on the principle that the gaseous POCl3 delivered through the bubbler reacts with the oxygen also supplied into the tube to form PSG, which acts as the source for elemental phosphorus in the following drive-in step.
Sheet resistance between 70 and 80 ohm/sq was common a decade ago. Around the same time, however, in order to reap the full benefits from the developments in metallization pastes, the industry was aspiring to move towards high sheet-resistance emitters. The atmospheric pressure furnaces have been facing uniformity issues when moving to such emitters. Circa 2014, diffusion equipment suppliers started aggressively promoting low pressure diffusion, which is still based on diffusion technology at its core but accomplished in a slight vacuum. Semco Smartech was the one that has developed low pressure diffusion furnaces based on this principle under the LYDOP brand that stands for Leak-Tight Yield Doping. Slight vacuum in the tube reactor reduces the movement of gas molecules in the reaction chamber, making the gaseous atmosphere more uniform all along the process chamber. Given that vacuum-assisted operating conditions afford a high degree of control over the processing environment, this approach not only enables attaining high sheet resistance emitters, but also improves the distribution. Low pressure diffusion works even better with throughput improving methods such as half-pitch loading and back-to-back loading.
The diffusion furnaces listed in this survey – a total of 7 from 5 companies – are all based on low-pressure diffusion. One of the most important developments associated with the diffusion furnaces is, again, the ability to process larger wafers. The industry has been quite successful in this transformation, and Raymond de Munnik, the CEO of Semco Smartech, credits batch type tube reactors for it. "Semco's LP Boron (SOLUS), Phosphorous (TELLUS) and Oxidation (DOMUS) equipment is capable of G12 manufacturing since 2020," said de Munnik. He further emphasized that the transition from M10 to M12 was rather smooth, due to the horizontal wafer orientation in Semco's reactor design.
Its TELLUS 8000 Series is a 5 or 6 stack configuration where each tube can be loaded with 1,800 M12 wafers. These wafers are loaded into compact cassettes and 10 such cassettes are placed in each tube, and the company sees a clear path towards a loading capacity of 2,000 wafers. The tool supports an hourly throughput of 7,000 wafers.
However, Semco is the only company offering horizontal processing, while the remaining 6 products from 3 companies are still based on vertical processing, and all the machines are capable of processing 210 mm wafers.
Germany based Centrotherm, another well-known equipment maker, has provided data for its furnace called c.Diff X-POCl. Offered in a 10-stack tube configuration and each tube with a 2,000 mm flat zone, supporting 1,200 or 1,600 wafers per boat in full-pitch and half-pitch, respectively, the tool supports a throughput of 11,100 M6 wafers per hour.
Ideal Deposition from China, well known for its ALD tools, also has a diffusion furnace on offer in a 5-stack configuration. Ideal's VP of Sales Zhang Dan mentions the precise temperature control, and a 595 mm inner tube diameter are the tool's most important features. The multi-gas flow distribution and control helps the tool reach a sheet resistance distribution of 4%. The tool has a 2,400 mm flat zone and the boat loading capacity varies with wafer size – 1,400 G12 wafers, 1,600 M10, and 1,800 M6 wafers. The system supports a rated throughput of 4,666 G12- size wafers per hour, while the tube diameter of 420 mm already supports processing wafer sizes of up to 230 mm side length.
S.C New Energy is one of the leading equipment suppliers from China and a low-pressure diffusion furnace for phosphorus diffusion is also part of its offering. Its DOA series is capable of forming high sheet resistance emitters – up to 150 ohm per square – with distribution of +/- 6% within a wafer and wafer-to-wafer from the same batch, and +/- 5% between batches. The 5-tube tool has a boat loading capacity of 1,400 of M10 or 1,200 of G12 wafers, translating into a final throughput of 3,500 G12 wafers per hour.
Naura claims to have developed the first low pressure diffusion furnace in China. Jiang Shuai, the company's overseas sales director, provided several insights into Naura's diffusion furnaces during his presentation Application of Cost Effective Doping Solutions in PERC Solar Cells at our Pushing PERC To Its Limits Conference 2022, where we discussed with experts how to manufacture highly efficient PERC cells. An important factor that determines the throughput of these machines is the number of tubes integrated into the machine which comes in 4 configurations – 5, 6, 10 and 12 tubes – each with a capacity of 1,200 to 1,600 wafers. Shuai emphasizes that Naura's tools are not only cost effective, but also of high quality. The company's furnaces provide 3 layers of safety – the top exhaust and the hazardous gas detection, the independent gas source and the box, and also the safety door switch. "We incorporate all these prevention systems in our tool design," said Shuai. On the process uniformity front, he says that even with very high sheet resistance of 150 to 170 ohm/ sq in the case of very shallow emitters, Naura's diffusion tools realize a uniformity deviation of 4% or less. The company's furnace design allows for better control over the ECV profile. The key elements here are higher process gas cleanliness, better process gas ratio regulation, higher accuracy in source control and optimization, continuously adjustable process pressure, and finally high process condition repeatability and reliability.
We have data for 3 products from Naura. The HORIS D8573AL can process a wafer size up to M6, while the HORIS D8578AL can handle a maximum size of M10. The third model, HORIS D12542P, can actually go beyond G12, up to 230 mm, facilitated by the larger diameter of the tube. While the first has a loading capacity of 1,200 wafers per boat, the latter 2 are rated at 1,600. These tools have higher throughput when processing smaller formats than the maximum spec. HORIS D12542P, for example, has 3 rated average throughputs of 4,456, 3,900 and 3,342 wafers per hour in M6, M10 and G12 wafer sizes, respectively.