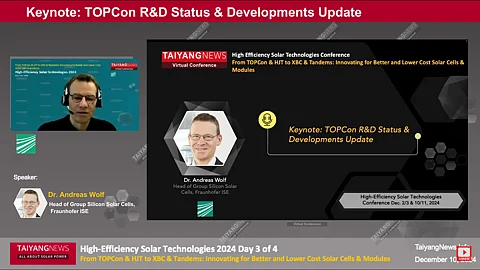
Fraunhofer ISE, in collaboration with RENA, has established a clustered wet treatment solution featuring inline and batch-type wet chemical etch tools for cost-effective industrial wraparound etching solution
The institute claims to have implemented the LECO process on TOPCon cell for the first time
It also developed passivated edge technology (PET) for half-cell edge passivation with Al2O3 layer deposition
Its TOPCon cell pilot line, featuring metallization with Cu plating technology, delivered up to 24% efficiency
Frauhofer ISE promotes TOPCoRE technology, where the front emitter is omitted and n-type wafer is replaced with p-type wafer, as an emerging technology
The recent upstaging of PERC as the mainstream cell technology by n-type TOPCon, which offers higher efficiency and cost-effective mass production, is a testament to the successful industrialization of a promising cell structure that originated at Fraunhofer ISE’s lab in 2013. Starting industrial implementation around 2015, TOPCon cell technology has evolved multiple times.
Dr. Andreas Wolf, Head of Group, Silicon Solar Cells at Fraunhofer ISE, delivered an informative keynote presentation on TOPCon R&D and development status at the TaiyangNews High-Efficiency Solar Technologies Conference 2024 (see Fraunhofer ISE presentation here). Fraunhofer ISE, the largest solar energy research institute in Europe with a staff of around 1,500 people and large lab facilities in Freiburg, called CalLab, offers feasibility studies, concept development, basic engineering for setting up new facilities, as well as training, ramp-up support, and ongoing operational assistance.
TOPCon (Tunnel Oxide Passivating Contact) technology features a carrier-selective contact through rear-side surface passivation. This allows the majority carriers to be easily extracted through the contact, while the minority carriers are rejected. The key to TOPCon technology lies in its rear-side passivation engineering, which involves an ultra-thin silicon oxide tunnel layer on top of n-type doped c-Si, followed by the deposition of an n-doped polysilicon layer on the rear side of the tunneling oxide. In this structure, the majority charge carriers pass through the tunnel oxide into the polysilicon (p-Si) layer, while the minority carriers are rejected. Wolf explained that the low-defect oxide layer results in a low surface recombination rate, leading to higher cell efficiencies.
After briefly describing TOPCon rear surface passivation engineering, Wolf outlined the generic fabrication process flow as follows: starting with n-type wafer texturization, followed by boron diffusion to form the front-side p+ emitter. The remaining borosilicate glass (BSG) on the surface causes some wraparound, which is removed in the next step, chemical edge isolation. Furthermore, the rear-side passivation is achieved by growing a silicon oxide layer, followed by the deposition of a thin p-Si layer, either doped or undoped. This is then followed by annealing or phosphorus doping. After removing the wraparound of the undesired p-Si layer through a separate wet chemical etching process, which also eliminates the BSG layer, the final surface passivation steps include front-side passivation, having a stack of Al2O3 and silicon nitride layers, or silicon oxynitride stack systems. However, the rear side surface is also passivated with silicon nitrate-based stack systems. Meanwhile, the metallization of the cell surfaces is achieved using screen printing technology, with the help of floating busbar or zero busbar technology in combination with a silver paste containing no aluminum, as part of the LECO process. This forms the contacts during the contact firing process, followed by a post-annealing step that facilitates hydrogen diffusion into the bulk, which increases the cell fill factor and Voc, explained Wolf.
Regarding the wet chemical etching steps – chemical edge isolation, Si wrap-around etch, and BSG removal – in the TOPCon fabrication process, the research institute established a cluster of inline and batch-type wet chemical etch processes in collaboration with RENA. This high-throughput clustered process includes an inline, fast single-side oxide removal on the wafer, with the rear side protected by a water capping during the process. It is followed by a batch-type rear-side etching process. According to Fraunhofer ISE, this high-throughput clustered etching process offers a cost-effective wet chemical treatment solution for the industry.
However, out of the 3 existing routes – ex-situ doping in LPCVD, in-situ doping for both PECVD and PVD – for TOPCon’s rear-side surface passivation layer deposition, the institute demonstrated the advantages of in-situ doping PVD tunnel oxide formation and PVD Si layer deposition in collaboration with VON ARDENNE. Moreover, Wolf stated that hydrogen management such as hydrogen concentration and distribution is essential to achieve good passivation. He also raised concern about recent trends of TOPCon cell degradation under UV light.
The LECO process, which decoupled the contact resistance from the contact recombination parameters, was first applied by the German institute to TOPCon cells. According to Wolf, the LECO process produces high-quality contacts with very low recombination parameters, due to the formation of small current-fired contacts and the fact that most of the interface under the silver finger remains passivated by the passivated layers. This latest metallization process enables the usage of aluminum-free silver paste featuring much lower firing temperatures and boron diffusion parameters with lower diffusion temperatures compared to its peers for cost-effective process steps.
Fraunhofer ISE’s baseline technology for TOPCon currently achieves 24.5% efficiency on M2 wafers and has recently scaled all tools to the M10 format, delivering 24% efficiency, noted the institute.
To meet the demand for silver paste cost optimization in the metallization process, the German R&D lab has recently achieved a champion cell efficiency of up to 24% on the first pilot line for M10-sized TOPCon solar cells with plated Ni/Cu metallization. The lab has also developed passivated edge technology (PET), which passivates the edges of half-cut cells by depositing an Al2O3 layer followed by a subsequent annealing step.
In terms of emerging technologies in the TOPCon cell development route, Fraunhofer ISE has advanced the TOPCon Rear Emitter (TOPCoRE) structure by omitting the front-side p+ emitter and replacing the n-type wafer with a p-type wafer. This development has recently achieved up to 26% efficiency and up to 732 mV Voc for a 2 x 2 cm² TOPCoRE cell.
Additionally, Fraunhofer ISE shared updates on progress in multi-junction tandem cells featuring the TOPCon cell structure as the bottom cell—specifically, inverted TOPCon and TOPCon². The lab has demonstrated an III-V/Silicon solar cell with a TOPCon² structure, achieving a record efficiency of up to 36.1%.