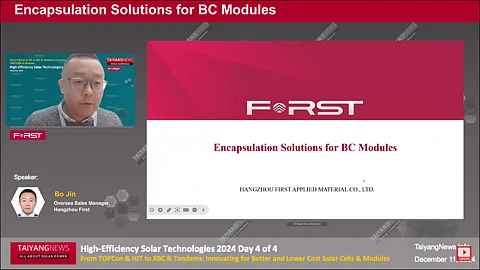
BC cell with no front-side metal contact can use thin front-side POE- or EPE-based encapsulant with a GSM value of less than 360
For the back side of BC cell-based module, HANGZHOU FIRST is offering a high reflective black film to boost power generation and module appearance
The company is offering insulating ink, being used for insulation between positive and negative gridlines, in both thermal curing and UV-curing categories
The growing adoption of various back contact (BC) cell technologies, including HPBC, TBC, and HBC, by mainstream PV module makers has driven the demand for BC-specific encapsulation solutions. These encapsulants must be tailored to meet the unique requirements of BC modules, such as the distinct characteristics of BC cells, resilience to environmental stressors, and cost-effectiveness, whether in double-glass or single-glass configurations.
In this context, at the recent TaiyangNews Annual Flagship Conference – High-Efficiency Solar Technologies 2024 – Bo Jin, Overseas Sales Manager at HANGZHOU FIRST, provided an insightful overview of the company's comprehensive encapsulation solutions for BC modules (see the presentation here).
Opening the presentation with a timeline of BC technology development – starting with the first proposal of BC cell technology in 1975 – Jin highlighted that lab-scale efficiency reached 23.2% by 1996, followed by SunPower's initial industrialization efforts between 1997 and 2010. From 2011 to 2016, the technology experienced significant growth, with Trinasolar’s national project and SunPower’s third-generation BC cells achieving an efficiency of 25.2%. Since 2017, the industry's milestones have expanded, thanks to the adaptability of BC technology across all mainstream cell types. Notable achievements include Huanghe Hydropower's IBC cells reaching up to 24% efficiency in 2021, SunPower’s and AIKO Solar’s TBC cells achieving efficiencies of 24.7% and 24.6%, respectively, and LONGi's HPBC and HBC cell technologies reaching efficiencies of 25.4% and 27.3%, respectively.
Aligning with the unique characteristics of BC cells – such as no metal contact on the front and both positive and negative electrodes on the back – a typical BC cell structure requires specific features from encapsulants. These include thinner front films with high transmittance, thicker back films offering strong resistance to corrosion and enhanced fluidity, as well as fine-tuning to meet the varying anti-PID requirements of BC cell structures, elaborated Jin.
After explaining the unique requirements of BC cell encapsulations, Jin proposed an optimized combination of front and rear encapsulations tailored to the specific characteristics of BC cell technology. The HPBC cell technology module, whether in a glass-glass or glass-backsheet configuration, faces PID issues on the front side and a high risk of corrosion on the back due to metal contacts on both polarities. The TBC cell technology (the BC version of TOPCon) glass-glass module is also susceptible to PID degradation on both sides and carries a risk of corrosion on the backside. Additionally, the HBC cell technology (the BC version of HJT) module, in a glass-glass configuration, requires high resilience against front-side UVID and rear-side water ingress to the TCO layers.
Aligning with the specific encapsulation needs of different BC technologies, Jin recommended POE or EPE-based front-side encapsulation of less than 360 GSM for both HPBC and TBC modules, with EVA for the back-side of HPBC modules. However, for the back-side of TBC modules, POE or EPE should be used. For the HBC technology module, Jin suggested thin front-side EVA or POE or EPE-based encapsulants, with a GSM value of less than 360, and POE or EPE-based encapsulants for the back-side.
For the front-side thin encapsulation films, HANGZHOU FIRST offers both POE and EPE encapsulants. The company began in 2012 with the launch of the TF series cross-linked POE and has since made periodic technological upgrades. In 2019, they developed the first co-extruded EPE film, followed by the TF4N series POE film and 360 GSM POE film for BC cells in 2022, noted Jin. This thin POE film, with high light transmittance, possesses key characteristics required for BC modules, including a thickness range of 280 µm to 360 µm, anti-PID properties, low shrinkage rate, good adhesion to glass, and no visual defects. However, the thin front-side EP304 EPE film, with a GSM value of between 280 and 360, can be customized with a middle POE layer ranging from 90 to 150 GSM. Additionally, it meets key property requirements, including excellent PID resistance, cross-linking, and adhesion performance, as well as process requirements such as uniformity, flatness, and low shrinkage rate, explained Jin. Internal test data, under extended PID stress test of up to 288 hours for a glass-glass TOPCon module, featuring front-side EP304 EPE and rear-side EVA, shows anti-PID requirement can be met with an EPE having 110 GSM POE layer. According to Jin, the anti-PID requirements of TBC cells are similar to those of TOPCon cells, suggesting that EP304 can also meet the anti-PID needs of TBC cells.
Furthermore, the company has launched the FW806WH series of high-reflective black films, featuring 2 layers: a black layer (cell side) and a white layer (airside). With a reflectivity of up to 75%, this film allows infrared wavelengths between 760 nm and 1,100 nm to pass through the black layer and be reflected to the cell. This unique feature enhances the module’s aesthetic appeal and boosts power output, said Jin. The film also offers high color stability and migration stability.
The insulating ink, a new material developed for BC cells, meets the insulation requirements between the positive and negative gridlines during the interconnection process. It is available in 2 main categories: thermal curing and UV curing, as well as either in colored or transparent formats, suitable for glass-glass and glass-backsheet configurations, added Jin. Additionally, the FT (thermal curing) and FURN (UV curing) series insulating inks, with visible light transmittance of up to 86.4% and 84.4%, respectively, demonstrated excellent reliability properties, such as good adhesion and a low yellowness index under in-house extended stress tests, noted Jin.
The company also offers cover strips or PI strips for BC modules, designed to cover the wires between the cell matrices, further enhancing the module's aesthetic appeal. On the backsheet side, the company provides high-reflection (HR) black backsheets with an infrared light reflection rate of over 60%, says Jin.