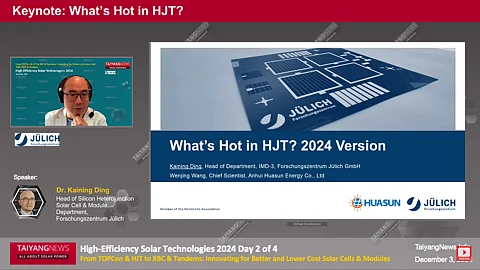
According to Jülich, the use of CCZ technology with fluidized bed reactor-produced granular polysilicon provides a more cost-effective HJT wafer solution, although with a slightly lower purity level
The transition to busbarless (0BB) metallization typically involves Smart Wire Connection Technology (SWCT), featuring wires coated with a low-temperature solder alloy, embedded in an adhesive polymer foil
The average mass production efficiency of HJT cells is between 25.4% and 25.5%
Heterojunction technology (HJT), a leading n-type cell technology alongside TOPCon and XBC, has made significant strides in cost reduction and efficiency gains, though its capacity expansion remains smaller compared to TOPCon. The HJT module has also experienced several technological advancements, in line with recent progress in cell technology. In addition to these implemented advancements, the industry is actively pursuing multiple potential pathways for further technological improvements.
On Day 2 of the recent TaiyangNews High-Efficiency Solar Technologies 2024 virtual conference, Kaining Ding, head of the Silicon Heterojunction (SHJ) Solar Cell and Module Department at Forschungszentrum Jülich GmbH, discussed the latest technological advancements and emerging trends across the HJT value chain (see Julich GmbH presentation here). Based in Germany, this research center houses the SHJ Cell and Module Department under the IMD-3 Photovoltaics division. It is equipped with cell and module lines capable of processing up to G12 half-cut (HC) formats, along with a range of advanced characterization tools. Additionally, the center operates a perovskite tandem cell line for the development of perovskite-silicon heterojunction tandem solar cells.
Ding began his presentation by highlighting the latest advancements in both HJT cell and module technology, along with key trends in ongoing technological progress. The industry continues to adopt G12 HC or G12R HC-sized wafers, with wafer thickness reduced to 110 µm and, in some cases, down to 90 µm for select manufacturers. However, the cell structure has transitioned to a double-sided microcrystalline process, featuring a μc-SiOx:H (n) front and μc-Si:H (p) rear side passivation layer. The metallization busbar design has evolved to SMBB with 20 busbars and, in some cases, has shifted to a busbarless (0BB) design, noted the research institute. In addition, the industry has shifted to stencil type of printing, featuring nickel or steel masks, by replacing screen printing technology. Other major advancements are the usage of silver-coated copper paste (AgCu) having Ag content between 40% and 50%, which has been further reduced to 30% in some cases. These advancements translate into average mass production efficiency from 25.4% to 25.5%.
On the HJT module level, the latest incorporated technological improvements are the bifacial glass-to-glass module, the usage of PIB-based edge sealant, and textured or coated front glass and rear glass with reflective stripes. In recent times, the industry also adopted UV-downshifting encapsulant after solving the initial reliability-related issues, added Ding. According to the research institute, the average mass-scale commercial module efficiency has crossed the 23% mark.
Following the brief overview of HJT technology’s current status, Ding discussed multiple topics that are trending in the industry.
The transition from using HJT wafers produced by the rechargeable CZ (RCZ) process to the continuous CZ (CCZ) process offers several advantages, particularly as polysilicon is fed during the ingot-pulling process. However, a drawback of CCZ technology is the slightly higher oxygen content within the wafer, which does not negatively affect the HJT cell due to the low-temperature fabrication process. Additionally, the use of CCZ technology with fluidized bed reactor (FBR)-produced granular polysilicon provides a more cost-effective wafer solution, although with a slightly lower purity level.
Dark degradation refers to the degradation of HJT cells after being kept in the dark for a period, such as between cell production and module assembly. While this issue can be reversed through light soaking of the module, it incurs additional costs. The institute emphasized that some observations suggest that if one shifts from amorphous silicon to nano-crystallized silicon oxide, the dark degradation seems to be stronger, while some reports suggest that using N2O as an oxygen source for the nanocrystalline silicon growth instead of CO2 controls dark degradation issue quite well.
The transition to 0BB metallization typically involves Meyer Berger's Smart Wire Connection Technology (SWCT), which utilizes wires coated with a low-temperature solder alloy, embedded in adhesive polymer foil. The foil is aligned to the cell with a subsequent low-temperature lamination process that creates contact with the cell's fingers. However, some systems, such as MAXWELL and XN Automation, use integrated film covering (IFC) to lay down wires and adhesive foils directly onto the cells.
The efficiency levels of HJT modules can be summarized as follows: up to 26.81% for the SHJ M6 cell, up to 27.30% for the HBC M6 cell, and 24.99% for the SHJ module, among others.