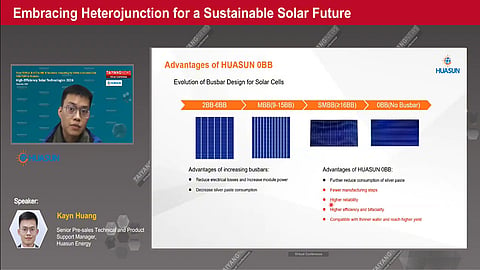
Zero-busbar (ZBB) architecture is gaining traction across all major cell technologies, reducing paste use, equipment needs and optical losses
By eliminating centralized busbars, ZBB enables more efficient current collection, reduces resistance and improves reliability
Implementation methods vary, with Huasun’s combined welding dispensing approach emerging as a high-performance solution
Complementing rapid innovations at the cell level, a wave of dynamic advancements has also hit module manufacturing. Today’s module designs are meticulously optimized to ensure no photon goes to waste, capturing every bit of light that strikes their surface. At the same time, modules are becoming increasingly application-specific, with manufacturers fine-tuning their BOM and offering a wide range of designs tailored to meet the demands of various installation scenarios. What were once considered niche or specialty products are now evolving into standard offerings across the industry. Interestingly, innovations initially developed for particular cell technologies are quickly proving versatile. Technologies such as zero-busbar interconnection, first introduced for HJT, have been successfully adopted by other architectures, while down-conversion films, originally created for HJT, are now finding relevance in TOPCon modules as well.
Zero-Busbars (ZBB)
Irrespective of cell technology, the hottest topic in the module making segment is ‘zero busbars.’ In principle, the technology is applied at the cell level, but consequent changes and adaptations must be made at the module level. What it essentially means is that the cells have no busbars, meaning the interconnection wires that establish the series connection are directly attached to the finger pads. There are several advantages of ZBB: it reduces paste consumption, equipment, energy and also costs, while improving efficiency, power and reliability. Starting with equipment, it eliminates 2 screen printers from the line to apply the busbars at the front and rear. In terms of electrical gains, ZBB decreases electrical resistance within the solar cell. By eliminating the need for centralized busbars, current can be collected and transported more efficiently across a large number of fine contacts. This design reduces the distance electrons must travel, minimizing resistive losses and enabling a more efficient flow of electrical charge. This helps in increasing efficiency. Huasun also showed that the ZBB technology improves reliability by reducing the occurrence of hot spots. It also brings in optical gains; the metal shadowing area on a ZBB module is about 16% less on the front and 27% on the rear, which increases the open area for sunlight absorption, according to Huasun. The latter also helps increase bifaciality (see Module Design Strategies For Back Contact Integration).
As for its implementation, there are 4 methods followed for ZBB, all nicely summarized by Huasun. The HJT maker follows an approach called Welding combined with Dispensing. In this method, the ribbons are soldered to the solar cells while simultaneously applying dispensing techniques to reinforce the bond. This allows both the cell interconnection and the ribbon-to-cell bonding to be completed in a single step. Standard EVA is typically used as the encapsulant material, with infrared soldering and UV curing supporting the process. A major advantage of this approach is that it eliminates the need for a load-bearing film, ensures strong adhesion, and enhances resistance to hotspot formation. However, this combined approach demands high precision during the dispensing operation to achieve optimal results; Maxwell is a leading equipment provider for this technology. The other standalone approaches are Dispensing and Integrated Film Covering (IFC), detailed in the table below. It also lists SWCT, a Meyer Burger proprietary approach unavailable in the open market.
This text is an excerpt from the TaiyangNews Cell & Module Technology Trends 2025 report, which can be downloaded for free here.