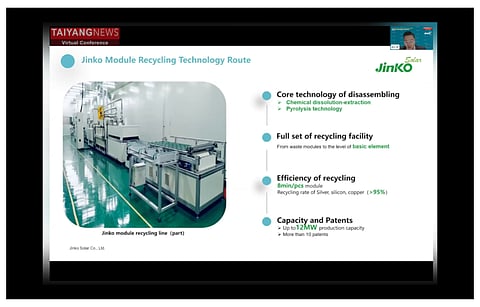
At the recently concluded TaiyangNews Virtual Conference on Solar & Sustainability, JinkoSolar's Global Product Solution Manager Roy Bi discussed the various measures the vertically integrated solar module manufacturer is deploying to operate in a sustainable way. This includes setting up a 12 MW pilot production line to recycle its solar modules.
JinkoSolar started working on its recycling efforts in 2017 when it confirmed the technical route and started constructing the 12 MW recycling demonstration line in 2019. Having completed the acceptance check in 2022, the line came online for large-scale module recycling.
The 12 MW pilot line takes 8 minutes/pcs module with a 95% recycling rate of silver, silicon, copper. Bi explained that this line uses a mix of physical and chemical recycling methods. For the physical part, the frame, junction box, backsheet, glass, ribbon and cell can be separated using customized equipment. For cell, we use chemical dissolution-extraction and pyrolysis methods.
A combination of physical separation and chemical extraction helps recycle almost all materials of a solar module. To reduce energy consumption of the recycling process, JinkoSolar uses thermal recirculation system.
Bi opined the key issue as volume since very little module waste is available. Referring to an IHS research that claims the initial wave of solar panels to retire in Europe by 2030 can reach 59 GW, while globally it will be 681 GW by 2050, he said dumping modules in landfills or burning them is not a viable solution. Recycling them then is the most optimal and sensible thing to do.
As more modules retire in the years to come, the Chinese company may consider expanding the recycling capacity further thus contributing to the sustainability of the module industry at large, he shared.
The company's total solar module production capacity stands at 70 GW currently which it aims to grow to 90 GW by the end of 2023.
Talking about sustainability in its production processes, the company that has shipped more than 150 GW modules globally, more than anyone else, Bi said JinkoSolar aims to go completely green in its manufacturing production by switching over to 100% renewable energy power supply by 2025 as part of its commitment to RE100. With only few solar companies listed among the RE100 member, Jinko has the most ambitious target to transition to full renewable energy supply among them; it is also in the top group when compared to many other industries' manufacturing members of RE100.
In fact, JinkoSolar's facilities operational in Yunnan's Chuxiong, Sichuan's Leshan and in Malaysia are already zero carbon plants, he shared, which was achieved with the help of expansion of its solar PV capacity and adding energy storage component.
Bi's presentation during the conference is available on TaiyangNews YouTube channel here.