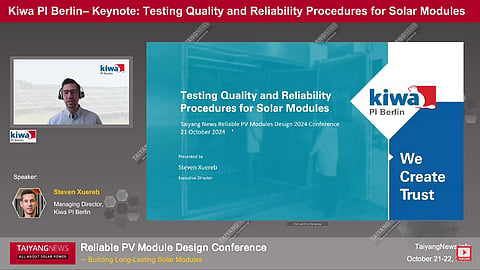
Kiwa PI Berlin, as a 3rd party service provider, offers a comprehensive quality assurance framework for module buyers
This comprehensive quality assurance framework spans across procurement, pre-production, to pre-installation phase
The company’s pre-shipment inspection (PSI) phase ensures the factory is meeting all the agreed inspection criteria related to quality
The batch testing stage under the production module testing phase, assesses material and process consistency in ongoing batch production
Today’s high-efficiency and high-power PV modules, the backbone of utility-scale PV plants, offer up to 30 years of guaranteed power generation for buyers like solar developers. Achieving long-term milestones such as Return on Investment (ROI) and low Levelized Cost of Electricity (LCOE) hinges on maintaining stringent quality standards during manufacturing. Recognizing this critical need, many solar developers outsource on-site auditing and quality assurance to 3rd party testing and inspection agencies.
Steven Xuereb, Managing Director of Kiwa PI Berlin, a global leader in 3rd party testing and inspection services, outlined the company’s comprehensive quality assurance framework for module buyers at the recent TaiyangNews Reliable PV Module Design Conference 2024 (see the presentation here) . Kiwa PI Berlin has conducted over 1,000 factory audits for PV modules, inverters, storage systems, and electrical equipment, overseeing more than 175 GW of PV module production. The company operates testing laboratories in Berlin, Germany; Suzhou, China; and California, USA.
Kiwa PI Berlin divides its quality assurance services into 4 phases: procurement, pre-production, production, and post-shipment.
During the procurement phase, Kiwa PI Berlin works with its clients to define the desired module technology, size, and specifications. The company establishes manufacturing and quality requirements, consolidating them into a single module supply agreement that outlines the scope of quality assurance and pass/fail criteria. It also provides recommendations for batch or product-level rejections and facilitates the closure of supply agreements.
In the pre-production phase, conducted 4 to 6 weeks before manufacturing begins, the company performs risk assessments and factory audits. These assessments involve reviewing all process steps and standard operating procedures (SOPs) to identify potential issues. Recommendations are provided to manufacturers to rectify shortcomings before production starts.
After acceptance of the factory readiness, Kiwa PI Berlin moves into the production phase which includes 4 sub-phases – production oversight, pre-shipment inspection, pre-shipment testing – batch, ongoing reliability monitoring, and container loading inspection.
After supervising each shift of the production, the process shifts into the pre-shipment inspection stage. In this inspection, at the end of batch production, the company typically reinspect and retests modules in a specified sample rate to verify that the factory is meeting agreed inspection criteria in terms of quality. This inspection, which can take between a half and a full day, includes flash testing, bifaciality measurement, visual inspection, and EL image. The company shares that after completing the pre-shipment inspection (PSI) for over 774 batches of modules in the last 2 years, only 10% of the batches were without any defect. Xuereb further noted that the largest amount of defects of up to 25% share, were under the EL category, including cell cracks, soldering defects, short-circuit cells, frame defects, sealant missing, and cell connector defects.
The company also highlighted a notable observation: modules with the same bill of materials (BOM) exhibited varying quality when manufactured at different geographical locations, often due to insufficient manpower training, inconsistencies in production equipment, or limited factory resources.
During the PSI phase, the company adheres to ISO 2859-1: General Inspection Level II, sampling a minimum 10 MW batch with acceptable quality limits (AQL) set at 0 for critical defects, 1.5 for major defects, and 4.0 for minor defects. Across 60 utility-scale projects involving 25 manufacturers, Kiwa PI Berlin’s analysis revealed that an AQL of 0 was applied for critical defects in 100% of the projects, while over 80% adopted an AQL of 0.65–1.5 for major defects and 2.5–4.0 for minor defects.
In production-level module testing, Kiwa PI Berlin employs 2 tiers of laboratory testing: batch testing and ongoing reliability monitoring (ORM). These tests, ranging from short- to mid-term durations, assess material and process consistency in ongoing batch production. The batch approval process can be done in either a 3rd party laboratory or Kiwa PI Berlin’s lab, whichever is closer. Following the completion of the test sequence in between 7 days and 10 days, including initial characterization such as flash testing, visual inspection, and wet leakage testing, the batch can be approved if there are no repetitive defects.
In ongoing reliability monitoring, a sequence of tests is designed to check the consistent performance and reliability of modules during a large production volume, such as 200 MW. These tests include thermal cycling (TC), damp heat (DH), humidity freeze (HF), and UVID. Spanning 4 to 6 weeks, these tests are not part of the batch rejection process but provide valuable insights into production consistency through root cause analysis.
Other tests
The last stage of the quality assurance program will be post-shipment inspection, such as installation supervision and post-installation inspection including IV and EL testing.