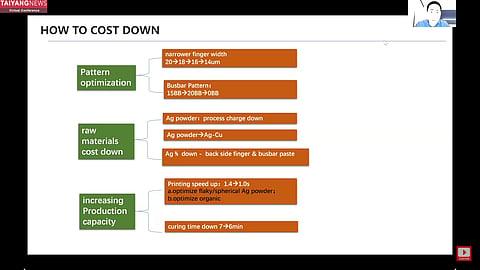
HJT is one of the widely adopted high–efficiency cell technology in commercial production with some companies exclusively focusing on it. While the technology has several benefits, an important limitation of HJT is its higher costs, and metallization pastes are the key contributors to costs. Addressing this challenge, Ocean Tang, technology director of HJT at Fusion Material, a leading paste supplier from China, in his presentation at TaiyangNews annual flagship event, High-Efficiency Solar Technologies 2023, provided insights into the ways and means to reduce HJT metallization costs along with the roadmap. Tang also provided an overview of the company's corresponding paste product solutions.
Bottlenecks & mitigation
As a matter of fact, HJT requires a fairly different metallization process and process consumable – the metallization paste – though the basic constituent is still silver. Unlike the pastes used for other cell technologies such as TOPCon or even PERC, which are fired at high temperatures, HJT pastes are cured at rather low temperatures of about 200°C to safeguard the underlying passivation layers. This is thanks to the thermoplastic polymers used in HJT pastes, which enable a low–temperature process.
Tang took the top weak points associated with the metallization of HJT in comparison to the other technologies, especially TOPCon, as the lead of this presentation, and laydown is naturally top of the list. He elaborated that the HJT silver finger paste has a 17 mg/W laydown compared to 13 mg/W with TOPCon and 9 mg/W for PERC, all at the cell level. The HJT paste's 30% higher laydown compared to the TOPCon paste significantly contributes to the higher mass production cost. The higher laydown is also partially due to the wider finger opening. According to Tang, 30 µm is the typical finger width realized with HJT, while 25 µm is the practice with TOPCon. The wider finger width not only consumes additional amount of a precious metal – silver – but it also increases the corresponding amount of shading, reducing the currents of the cell. The low temperature cured pastes for HJT require higher silver loading, 2% to 3%, according to Tang, to compensate for the lower conductivity of such pastes. Due to their composition, HJT pastes cannot support printing speeds of the typical fire-through pastes. The scale of the economy is yet another aspect that is missing in HJT. Unlike the fire-through pastes, which have a monthly usage of 700 tons, the HJT segment requires less than 100 tons, which makes the paste conversion process relatively more expensive.
As a means to overcome the aforementioned weaknesses of HJT pastes, Tang recommends 3 potential areas of improvements – metallization pattern optimization, tweaking paste composition and improving printing process productivity.
In the context of optimization of metallization layout, the main point of focus is naturally on narrowing the screen opening to deposit thinner fingers. As an example, he emphasized that reducing the finger thickness gradually from 20 µm to 18 µm and then to 16 µm can reduce the paste consumption significantly. Changing busbar patterns by adding a greater number of busbars initially, say having 20-busbars, and then eventually moving to busbarless (0BB) is yet another strategy as part of pattern optimization.
As for the customization of paste composition, blending silver with copper, with the latter having good conductivity and a lower price, is increasingly becoming the preferred alternative to pure silver composite. The usage of cheaper silver powder in the paste composition, and less silver content in busbar or rear finger paste are the other means of cutting the raw material costs of paste making.
Indeed, Tang provided the time stamps as to when a few of these advanced methods will be implemented. Characterizing the SMBB, most likely referring to 20-busbars, in combination with 18 µm finger width and using silver coated copper for rear fingers as the state-of-the-art as of the end of 2023, he is optimistic to reach the next level of 16 µm finger thickness and using silver coated copper on both sides in Q1-2024. This can reduce metallization costs by 30%. In about another quarter from there, he is optimistic of attaining even the next level of 0-BB pattern complemented with 16 µm finger thickness using silver coated copper pastes.
As to line productivity improvements, an indirect means of reducing the costs, finetuning the paste composition to be compatible with high-speed screen-printing and optimizing the chemistry of the paste composite to lower the curing time, can reduce production costs.
Fusion's solution
Fusion is already offering paste products that support a few of these advanced metallization schemes, while others are part of the future development roadmap. Delving into the current product offerings of this company, Fusion has 2 different HJT finger paste series with pure silver for 2 different busbar layouts – 0BB and SMBB. The 0BB paste series, called CSP-T2L, consists of 2 variants – FC010 with a silver content of 92% to 94% and FC020 model with a lower 91% to 93% silver content. The SMBB compatible paste series CSP-T2F consists of 3 models differentiated according to finger specs. The FC012 and FC013 models, while with the same silver content of 92% to 94%, the former is compatible with 19 µm screen openings and the latter with 16 µm. The FC012R, the third model, with 89% to 91% silver loading is mainly formulated for rear finger metallization.
Apart from the pure silver content pastes, Fusion also offers the CSP-T2C silver-coated copper paste series with 30% to 60% silver content. It is compatible with narrow screen openings as low as 16 µm to 20 µm. Fusion's in-house experiments with silver coated copper paste, when used on the rear side, show a similar efficiency level compared to pure silver paste. However, when applied on both sides, the results show 0.1% lower average cell efficiency value compared to pure silver pastes due to the loss in FF.
The current crop of products typically use of 50% copper content which can save up to 25% to 30% paste cost, according to Tang. He sees the potential to increase the copper content further, while mentioning that a 40% reduction in costs is doable. The other cost reduction potentials are to reduce the finger width with silver coated copper. A case in point: using 16 µm screen opening with its silver coated copper paste series CSP-T2C can reduce paste laydown by 20% compared to a 20 µm screen opening. Blending all these advanced concepts together and careful optimization, Tang expects to bring down the paste laydown of silver coated copper from the current level of 16 mg/W with 17 µm to 12 mg/W with 15 µm screen opening with costs at par with TOPCon by Q2-2024.
With respect to the cost reduction routes for busbar pastes, Tang mentioned that the silver content has been reduced by 1% over the 2022 level. Now the company is choosing an aggressive path of tin-coated silver pastes for the busbars. The company plans to reduce the silver content gradually – first to 80% in Q1-2024 and to 70% in the subsequent quarter. Fusion is currently offering 2 models – DLS-1 and DLS-3 for the busbars. The DLS-1 with 90.5% to 92.5% silver content can be used on 9BB to 15BB cells. Its new DLS-3 is a silver-coated tin paste (Ag-Sn). As reliability is the key criterion when evaluating such a new composition, in the case of busbars it is adhesion that speaks for it. Tang assured that the silver-coated tin pastes exhibit improved busbar adhesion strength of 2.3N compared to 2.2N with a pure silver paste.