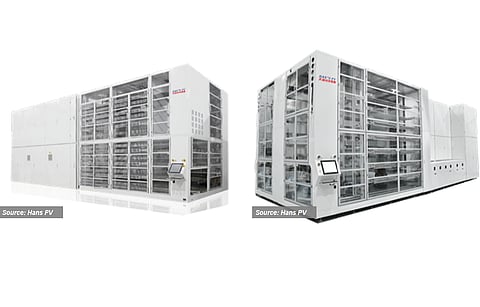
Passivation is a very crucial step in solar cell processing. The bulk of silicon wafers can neither be completely free from impurities, nor from crystal lattice disruptions on both surfaces. These interruptions in the periodical arrangement of silicon atoms result in dangling bonds, which work as recombination centers. Passivation is a process which deactivates these defects and reduces the surface recombination of charge carriers, safeguarding cell efficiency. (Please check our TaiyangNews Report on TOPCon Solar Technology 2021 for more details on the basics of passivation.) Rear passivation is what differentiates the PERC cell architecture from the standard BSF structure, thus is also what differentiates TOPCon from PERC. However, TOPCon also features another difference that it is typically implemented on the n-type wafer format. Interestingly, both PERC and TOPCon have superior rear junction engineering over their predecessor. The passivation schemes and required production equipment vary for different cell architectures. Silicon nitride has been the most reliable material for the sunny side of a BSF cell, and PECVD has been the state of the art for its application to act as both an antireflective and a front surface passivation film. The material of choice for rear passivation for PERC is aluminum oxide, hands down. As for the deposition of this material, one of the 2 mainstream technologies available is PECVD, which has been in use for depositing silicon nitride for years. The other is atomic layer deposition (ALD), with roots in the semiconductor industry. Irrespective of the method, a protective capping layer is a prerequisite, which again is silicon nitride deposited with PECVD. TOPCon involves growth of interfacial silicon oxide and deposition of intrinsic polycrystalline silicon layers, which is subsequently doped. The tunneling oxide can be grown thermally or as part of any other deposition methods used for polysilicon deposition, which is the heart of the TOPCon process. Almost every deposition technology used in PV is promoted here — LPCVD, PECVD, APCVD, ALD and PVD – however, LPCVD and PECVD are the mainstream now, while one TOPCon producer is pursuing the PVD route. For the context of the current survey, with the data that we have received, only PECVD and LPCVD are discussed. To provide insights into these 2 deposition technologies, we have also included interviews from leading suppliers of LPCVD and PECVD tools – Laplace (see Laplace's Zhang Yao Interview Why LPCVD Continues To Be An Attractive Solution For Manufacturing TOPCon Solar Cells) and Leadmicro (see Leadmicro Chief Scientist Baochen Liao Talked To TaiyangNews About The Key Enablers for TOPCon Cell Production).
LPCVD systems for TOPCon When it comes to the listed LPCVD tools, 3 companies – Laplace, Naura and Semco – have provided data for one product each.
Laplace is listing its LLP430 LPCVD system, designed for deposition of tunnel oxide and polysilicon layers for TOPCon cells. The tool is based on a 6-chamber configuration and supports wafer dimensions of 156 to 230 mm. Unlike the traditional LPCVD furnace, Laplace's tool processes wafers in a horizontal orientation. The processing boat has a loading capacity of 2,000 or 2,400 wafers. The system is sufficiently equipped to accomplish all the steps required for passivated contacts – applying tunneling oxide, polysilicon deposition and in-situ doping of polysilicon. However, for the throughput calculation, the company considered ex-situ doping and a 110-minute cycle time. The tool is rated with a throughput of 7,500 wafers per hour where 2 wafers are placed in a front-to-front configuration per slot. When following the current convention of single wafer per slot, the tool supports a throughput of 4,000 wafers per hour.
Laplace's tool processes wafers in a horizontal orientation and the system is sufficiently equipped to accomplish all the steps required for passivated contacts – applying tunneling oxide, polysilicon deposition and in-situ doping of polysilicon. (Source: Laplace)
Naura has provided data for its HORIS L12663, a 2023 model, which is offered in a scalable configuration where the process chambers can be 5, 6, 10 or 12 in number. This LPCVD tool is also designed to accomplish all the processes. However, it is unclear as to what degree of process integration has been considered for throughput evaluation. The rated throughput of 8,640 M10 or 7,656 G12 wafers most likely refers to ex-situ doping.
Semco has been an equipment partner for early adopters of TOPCon, Korea's LG for example, and the company claims more than 6 years of mass production experience with its tool. It has also supplied "several" of its toolsets to leading manufacturers that are operating in mass production. As to the listed products, Semco's HORTUS LPCVD platform comes in a 5- to 6-stack furnace configuration. Each tube can be loaded with 10 boats, each with a capacity of 180 wafers, in the horizontal orientation. The tool accomplishes all 3 processes – tunneling oxide growth, polysilicon deposition and in-situ doping of polysilicon film – in a cycle time of 102 minutes. This translates into an hourly throughput of 4,547 wafers. Semco actually recommends the thinnest polysilicon film of 100 nm while the other 2 LPCVD makers specify a range of 120 to 150 nm.
PECVD system for TOPCon
The rear passivation stack for the TOPCon can also be accomplished with PECVD, and we have data for 3 products from as many companies – Centrotherm, Ideal Deposition, Naura and SC New Energy.
Centrotherm is promoting c.DEPO X LPCVD system with a 10-stack tube configuration. The tool accommodates larger wafers up to G12, with a thickness of 110 to 250 μm. It accomplishes all the 3 processes for TOPCon as a standard configuration. Similar to the aluminum oxide deposition systems of the company, each boat in this tool has a loading capacity of either 350 M10 or 288 G12 wafers. It supports an overall throughput of 5,200 wafers per hour.
The Ideal PE-poly system from Ideal Deposition, launched in 2022 model, is equipped with 6 tubes and is designed to accomplish all passivation steps for the TOPCon cells. In addition to tunneling oxide, polysilicon deposition and in-situ doping, the tool also accomplishes the deposition of silicon nitride on the rear as well as the front. Designed to accommodate 540 G12 wafers per boat, the tool's max throughput is rated at 4,500 wafers per hour.
Naura has provided data for its latest tool platform called HORIS P12682, launched in 2023. It is designed for larger wafer formats such as M10 and G12 and is also capable of handling thinner wafers of 125 μm with M10 size and 145 μm with G12. The wafer boat can accommodate 768 M10 or 616 G12 wafers. The tool has a throughput of 6,912 M10 or 5,544 G12 wafers per hour.
The article is an excerpt from the TaiyangNews Market Survey on Solar Cell Production Equipment 2023, which also includes detailed product specs and can be downloaded for free here.