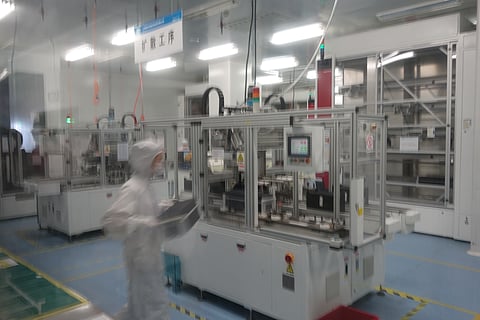
Surprisingly, the 6th International Technology Roadmap for Photovoltaics (ITRPV) sees a second chance for a few technologies, which were once the hottest topics in ingot and cell manufacturing but nearly disappeared almost as fast as they popped up – quasi-monocrystalline in the crystal growth segment and selective emitters in cell processing. Let's take a loot at ITRPV's view on selective emitters.
As part of its forecast of the trends in the diffusion segment, the 6th edition of the roadmap depicts that four different selective doping technologies, would eventually earn a prominent presence over the next 10 years. The other topics of interest in the diffusion section of the latest roadmap are the different methods used for boron diffusion, which is discussed for the first time, and the perennial subject – the PV industry's move to emitters with higher sheet resistance.
High on emitter sheet resistance
The emitter sheet resistance is one parameter that influences front surface recombination losses. In fact, the progress of cell makers in moving to emitters with higher sheet resistance has killed the prospects for selective emitters. ITRPV underscores that its earlier proposals to increase sheet resistance have been implemented, thanks to the developments made by the paste suppliers. However, while last year's document predicted that 110 ohm/square would be common in 2015, that was apparently a bit too optimistic. According to the 2015 report this level will be reached 3 years later, in 2018 – from the current level of 95 ohm/square and up from 90 ohm/square in 2014. Soon after comes a limit: a saturation level of 120 ohm/sq is expected to be reached in 2022, one year later than predicted in the 5th edition.
The progress in increasing sheet resistance is mainly driven by the improvements in contact formation. Because the challenge is not to form the emitter with high sheet resistance, but establishing the contact with a suitable silver paste. However, at some point sheet resistance cannot be increased further, as even a minimal penetration of silver into silicon – to attain the desired conductivity – would puncture the junction.
Selective emitters to come back?
ITRPV 2015 anticipates some changes also in the technologies used for phosphorus doping. While the homogeneous emitter formed via the diffusion process has been and will be the dominating process – with a share of 90% today and above 60% in 2025, ion implantation based doping is expected to pick up in the long run. But what seems a lot in relative growth terms will be still very limited regarding the absolute share. According to ITRPV, ion implantation for forming homogeneous emitters will grow from a negligible market share today to about 10% in 10 years. As for phosphorus as impurity, selective ion implantation would attain 5% share in 2019 and grow its presence to 9% within 10 years. Among the traditional methods to form selective emitters, employing lasers would double the share from about 3% today to 6% by 2017. The wet-chemistry based etch back method, which also has a 3% share and would slowly progress to a peak at 5% in 2022. Attaining selective doping using solid precursors applied with printing is expected to enter the market in 2017 and gain a 5% share in 2022. If added up, all selective emitter technologies would grow from a share of 4% today to 27% in 2025.
Implants are better for boron
N-type is yet another cell architecture that requires a major change in diffusion process. Though ITRPV 2015 expects the technology to gain only a 10% share in 10 years, the roadmap has emphasized on boron diffusion, a key step in n-type process flow. It mainly studied estimates market shares of various technologies to induce p-type impurity. Thermal diffusion using boron tribromide (BBr3) as the precursor is currently the most widely used process with a share exceeding 80%. However, it is not a simple drop-in replacement of the precursor. The byproduct of the process using BBR3 acts as a glue to quartz, thus creates lot of maintenance issues. Then, boron diffusion typically has higher process times, lowering the throughput of the diffusion furnace by about half compared to POCl process.
However, ion-implantation tools are more susceptible for such shift in dopant element. Not only do implants cut short the processing sequence, they also eliminate masking for cleaning steps. These tools are expected to play a bigger role in the future, growing from about 10% share in today's market to about 40% of n-type wafers in 2025, incrementally replacing thermal diffusion.
Hybrid diffusion for n-type
Diffusion using a solid source precursor is yet another method under serious evaluation for realizing boron doping. The process still employs traditional diffusion furnaces, but only for the drive in step of the wafer. The precursor, BSG, is coated on to the wafer surface using Atmospheric Pressure Chemical Vapor Deposition (APCVD) tools. The advantage of this method is that both boron emitters as well as phosphorus Back Surface Fields (BSF) required for typical n-type architectures can be realized in a single drive in step called co-diffusion. ITRPV 2015 expects the technology to double its followers for every two years from 5% in 2015 reaching close to 20% in 2019, with no significant further growth anticipated afterwards.
It is helpful that ITRPV has shown its take on the development of the different boron diffusion technologies, but first of all it remains to be seen if the n-type cell architecture grows as much as anticipated. Compared to former estimates its shares have not increased as much as forecasted. The reason is that p-type cells have improved dramatically – and there is still quite some potential.