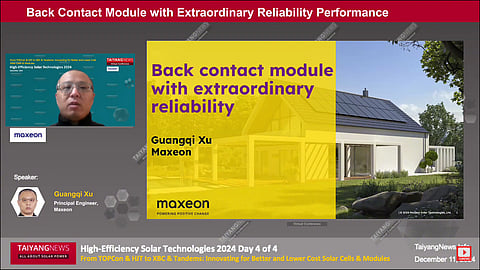
The Maxeon 7 series IBC module offers up to 24.7% efficiency and the Maxeon 8 series, to be launched in 2025, is expected to reach beyond 25%
This module offers 40+ years of lifetime with a 0.25% annual degradation rate
IBC cell technology can leverage multiple features from the TOPCon technology PV ecosystem
The success of any photovoltaic (PV) cell technology hinges on 3 key metrics: efficiency, durability, and adaptability within the broader PV ecosystem. To fully capitalize on back contact (BC) technology – shifting both positive and negative metal contacts to the rear side of the cell – it is essential to develop high-efficiency, durable BC products within a mature PV ecosystem that spans both upstream and downstream components.
At the TaiyangNews Annual Flagship Conference – High-Efficiency Solar Technologies 2024 – Guangqi Xu, Principal Engineer at Maxeon Solar Technologies Ltd., presented an in-depth look at the company’s high-efficiency, reliable IBC modules (see Maxeon presentation here). He also offered insights on how TBC technology can enhance the existing PV ecosystem of TOPCon while addressing several challenges and opportunities in the process.
A pioneer in IBC technology, Maxeon began in 2004 with the launch of the first commercially available IBC PV panel. In 2007, the company further advanced its technology with laser processing. By 2015, Maxeon transitioned from diffusion-based cell processing to tunnel junction BC (TBC) architecture. This evolution led to the periodic release of the Maxeon IBC module series, with the latest Maxeon 7 series now achieving up to 24.7% efficiency, says Xu.
This IBC module, featuring an IBC cell with a thin layer of solid metal on the rear side, demonstrates exceptional resilience against power losses caused by cell cracks, continuing to conduct current even after a silicon break. Additionally, Xu noted that, after extended field performance under variable thermal stress, potential cell edge ribbon cracks – caused by metal wire fatigue and subsequently transferred to solder joints – can occur in modules like PERC, TOPCon, or HJT, where thin metal wires form an 'S' curve for cell-to-cell interconnection. However, these issues can be mitigated with Maxeon’s cell interconnection technology, which includes redundant cell connections with embedded strain relief to neutralize stress on solder joints by absorbing expansion and contraction.
Leveraging the low-breakdown voltage characteristic of BC cells, the Maxeon IBC module offers higher reliability under partial shading and a lower safety risk of burnout following diode failure. Internal test data shows that the Maxeon 7 series IBC module reaches a maximum cell temperature of 59°C under unshaded conditions and up to 85°C during partial shading with the bypass diode intact. In partial shading with diode failure, the module can reach up to 78°C without any visible or measurable impact. In contrast, Xu shared that under partial shading and diode failure conditions, TOPCon and HJT modules experienced severe bubbling, burning of the backsheet and encapsulant, and discoloration, with cell temperatures exceeding 550°C.
Maxeon further validated the industry-leading 40+ years of useful life and 0.25% power degradation of its IBC module through SunPower’s internal extended environmental stress tests, including the DH8000 and TC800 tests, which resulted in less than 2% degradation, emphasized Xu.
Regarding BC technology, a new entrant following TOPCon and PERC, its adaptability to the existing PV ecosystem, including both upstream and downstream components, will play a crucial role in a successful technology transition, says Xu. Providing a brief overview of the PV ecosystem during the transition from PERC to TOPCon, Xu highlighted the major challenges, opportunities, and legacies that the industry encountered. Key challenges included the shift from p-type to n-type, the need for higher-purity polysilicon, silicon wafers with lower oxygen impurity (Oi) content – down to 12 ppma – the increase in minority carrier lifetime (MCLT) from 70 µs to 1 ms, the adjustment of resistivity range from 0.3-2.1 ohm·cm to 0.7-1.4 ohm·cm, and the reduction of wafer thickness to 125 µm.
Although TOPCon technology inherits the cell process flow and is largely compatible with tools used in PERC cell and module lines, several new process tools were required, including boron diffusion, SiOx+poly-Si deposition, laser for boron SE or LECO, as well as new metallization paste, encapsulant, and edge passivation. Xu also noted that TOPCon inherited established markets from PERC, such as utility, residential, and commercial applications.
In contrast, TBC technology inherited several features from the TOPCon ecosystem, including the same-grade n-type poly-Si, the same or lower requirements for Oi content (no boron diffusion), and identical MCLT ranges. However, the flexibility to use higher wafer resistivity, compared to TOPCon’s range of 0.7-1.4 ohm·cm, presents an opportunity for ingot makers, Xu noted. While the cell fabrication process steps offer multiple inheritances, including tool compatibility, a lower budget for thermal processes, encapsulant, and edge passivation, there is a need for 2 additional process steps: patterning/cleaning and an extra poly-Si deposition. Additionally, metallization paste, customized for contacting p-poly-Si, is required. On top of it, the BC transition must address the global economic landscape of oversupply and the industry's cash loss challenges.
The company expects to launch the next-generation Maxeon 8 series IBC module, which will feature more than 25% efficiency, in 2025.