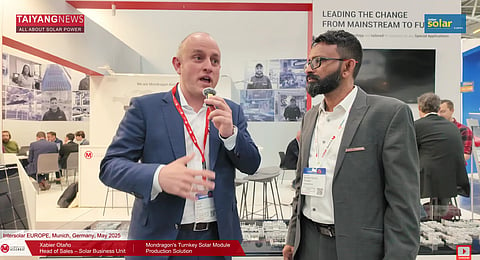
Mondragon Assembly showcased its miniature model of a 1.5 GW turnkey PV module production line
The company also displayed innovative and special PV modules, built with its tailor-made production tools
It has achieved process optimization for its tabber and stringer, typically in interconnection technology, and widening of process windows
Choosing between a turnkey PV module production solution and an assembled line consisting of third-party equipment is a strategic decision that impacts efficiency, quality, scalability, and long-term investment for a PV module maker. Unlike the assembled line, the turnkey line is offered by a single vendor, which includes production tools covering production stages from start to end, along with software, process design, training, and support. This facilitates full system integration with reduced downtime and fewer compatibility issues, resulting in faster commissioning and process optimization. Procuring the whole system from a single vendor makes the after-sales service and troubleshooting easier, in line with the warranty and service agreement, compared to an assembled fabrication line.
Aligning with the advantages that come along with a turnkey production line, Mondragon Assembly, a Spanish PV module production equipment provider, showcased a miniature model of its 1.5 GW turnkey line, along with other offerings, during Intersolar Europe 2025. Speaking to TaiyangNews, Xabier Otaño, Head of Sales – Solar Business Unit at Mondragon Assembly, shared a brief overview of the company’s turnkey line, innovative production solution, and latest process improvements.
The turnkey line features tools for up to 36 production stages, starting from the cell cutter to the module sorter. These tools, integrated according to the production process sequence, are the Cell cutter, Glass Loading, Foil Cutting, Encapsulant Flaten & Ironing, MTS Stringer, String Lay-up, Auto-bussing, String Taping, Barcode Placement, Foil Cutting with Punching, 2nd Glass Loading, Lead Bending, EL Test, Glass-Glass rework, Glass-Glass Edge Taping, Glass-Glass Edge tape removal, Edge Trimming, Corner Edge Trimming, Visual Inspection, Framing, JB station (bonding, placing, soldering, and potting), Curing Line, Sun Simulator (EL + Hi-Pot), Labelling, and Module Sorter. Along with these tools, Mondragon’s turnkey offering includes standard after-sales services and training to operators, says Otaño.
The company’s in-house research lab develops innovative PV module production tools, tailored for either new PV technologies or new processes, or production yield optimization. Following a brief overview of the displayed turnkey line, Otaño highlighted a few innovative PV modules, like the flexible module, organic module, building-integrated PV (BIPV) with different cell gaps, and a 3D-shaped module on fiberglass with back contact (BC) technology. These innovative products have been fabricated with Mondragon Assembly’s innovative production tools, added Otaño.
Otaño emphasized the company’s ongoing efforts on incremental process optimization in the tabber and stringer, typically in interconnection technology, and improving all aspects of maintainability and widening the process window as much as possible.