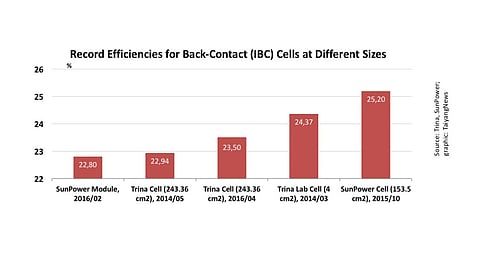
Integrated PV manufacturer Trina Solar is narrowing the gap between laboratory performance and commercial feasibility of its Interdigitated Back Contact (IBC) cell technology to less than a percentage point. The world's largest module company from China announced a world record conversion efficiency of 23.5% for an IBC cell on a 156 x 156 mm n-type wafer substrate.
Close to the lab record
This means that Trina improved its former record by over 0.5 percentage points within about 2 years time. Its old record stood at 22.94% efficiency and was announced in May 2014. The newly attained efficiency has been independently confirmed by the Japan Electrical Safety & Environment Technology Laboratories (JET), Yokohama, Japan.
The record is even more impressive, when taking into account that the top efficiency for laboratory solar cells is not so much higher – in fact, less than 1% point. The best lab cell measures 24.37% on a 2 x 2 cm cell size.
For IBC cells it is not just about record level performance or upscaling the technology to commercial size, but employing low-cost industrial process. According to Trina, its IBC cell technology developed at its State Key Laboratory of PV Science and Technology of China is based on proven practices, such as screen printing. That's the right direction. IBC has always has been known to result in very high conversion efficiencies as the junction and contacts are moved to the rear side of cell, thus eliminating the shading losses. But the technology requires rather complicated manufacturing steps, which makes the process expensive compared to other silicon cell technologies.
Lower than SunPower but larger
That's also the reason, why SunPower from the US is the only large-scale manufacturer of back-contact cells. The company, moreover, nicely packages its rather high-cost products for the market – either by offering financing services for rooftop systems or developing utility-scale projects directly on its own.
SunPower has pioneered IBC cells and is an efficiency leader in this field for a long time. Only in February, it announced a module with an impressive 22.8% efficiency. Its record back-contact cell even reaches an incredible 25.2% (153 cm2), which was confirmed by Fraunhofer ISE in October 2015.
But SunPower still produces 5-inch cells for its modules. In this regard, Trina's achievement is significant. The company not only says it employs low cost and standard manufacturing techniques (although all record cells usually come with a few tricks), it also uses today's standard wafer formats of 156 mm side length.
More records than just for IBC
Trina's IBC record is absolutely notable, especially when taking into account that the Chinese company produces mostly traditional standard crystalline cells. But Trina also has taken over the world records for PERC cells, where it leads the pack in both multicrystalline (21.25%) and mono PERC (22.13%) – and it is increasingly moving into PERC production, which reaches quite high efficiencies that can be produced rather simple (see our new free study PERC Solar Cell Technology 2016)