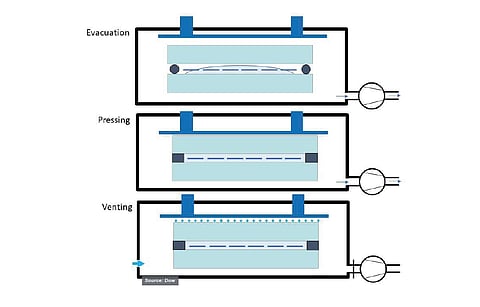
Silicone is also an interesting and well-known material used for encapsulation applications. Several variants of silicones have been introduced in the past but with very little success.
US chemical company Dow has now introduced its DOWSIL 9955, which like most silicones is a poly dimethyl siloxane (PDMS). The difference between this material and other silicones used for encapsulants lies in its curing chemistry, meaning establishing the cross link. According to Guy Beaucarne from the façade engineering and architectural design team of Dow Silicones, DOWSIL 9955 uses a 'unique and proprietary' condensation cure method as against the "additional cure" chemistry in traditional silicone encapsulant technologies. The new material has several advantages, the most notable of which is that it can be cured at room temperature and develop primer-less adhesion at room temperature, he said.
The condensation cure chemistry for silicone is not new and has been used in many products, including traditional silicone sealants, but it is new for transparent encapsulant products. DOWSIL 9955, originally a product developed for construction applications, is now promoted for module encapsulation applications. However, Dow is not directly competing with EVA or POE as both the materials are well established in their respective mainstream applications; but Beaucarne sees some segments where silicone can prove to be advantageous. "BIPV is one example," says Beaucarne. In this scenario, it is best to have the module life matched to the lifetime of other building components, which is typically 50 years, he explains. Beaucarne believes that, given their track record, silicones could provide such longevity when complemented with module technology and other bill of materials. Another potential application is modules for high temperature regions where silicone would provide the required reliability that is needed in such extreme weather conditions.
Dow's new solution is not to be confused with the product that has been introduced by Dow Corning many years back but under the PV6212 brand, which along with other silicone materials for PV are now part of the DuPont portfolio.
The DOWSIL 9955 material comes in a liquid form, and it can be used directly by the module maker by standard dispensing, facilitated by its fairly low viscosity, according to Beaucarne. It is not recommended for all module configurations, but primarily for glass-glass modules with a commercially available edge sealant. Beaucarne did not reveal the names of the module makers that are using DOWSIL 9955. However, while acknowledging that it is still at a very early stage, given the market for silicone-based encapsulant is very small, he believes that the solution has good growth potential with the emergence of PV in countries with harsh weather conditions as well as the emergence of BIPV.
Regarding the change required in production process, the solution eliminates the layup to cut and place the films but requires additional stations to dispense the silicone and edge sealant. The laminators which are generally used for glass-glass modules can also be used. The need for laminator arises due to the requirement of the vacuum and does not require the heating feature. In principle, one can develop a low-cost piece of equipment that can do just the evacuation and pressing. As for the costs, Beaucarne says that the silicones are substantially more expensive than EVA and a little more than POE; however, developing a completely new line keeping in view the strengths of DOWSIL 9955 can potentially reduce processing costs. "I cannot quantify the benefits now," he says. TaiyangNews covered POE and EVA in a different article (see: EPE: The Two In One Approach For Module Encapsulation).
While there is no study available to substantiate the 50-year reliability claims of Dow's latest solution, there are some studies out about modules using silicone as encapsulant. Beaucarne highlighted a recent joint technical research paper presented by Dow in cooperation with the European Commission's Joint Research Centre in Ispra, Italy, "Material study of photovoltaic modules with silicone encapsulation after long-term outdoor exposure" that showed that silicone has changed only a little after 20 years of operation in outdoor conditions. "We expect a similar level of performance with our 9955," said Beaucarne.
The Text is an excerpt from TaiyangNews' recent Market Survey on Backsheet and Encapsulation Materials 2021, which can be downloaded for free here.
An overview of the survey was presented during TaiyangNews Conference on Reliable PV Module Design. To learn more about the conference and view the presentations click here.