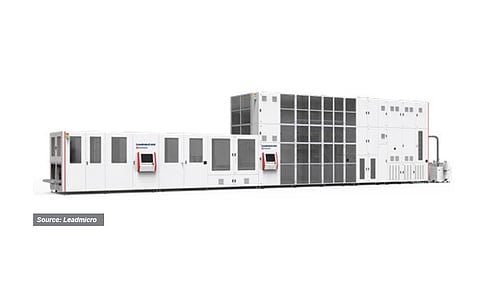
PECVD tools have been the work horse for application silicon nitride film applied on the emitter of the p-type solar cells since the past BSF days to the current PERC. The silicon nitride coating on the emitter serves two functions – passivation layer as well as antireflecting coating. On the process end, silicon nitride films of moderate refractive index of about 2 were typically used during the early days of its introduction. However, it is a tradeoff between passivation and optical properties. While silicon rich films with higher refractive index support better passivation, lower refractive index films are ideal for better optical properties. Films with a graded index, meaning decreasing the refractive index from substrate to ambiance, and multilayer films built on the same logic became promising in this context. Such films were also considered a means to combat PID a few years ago. However, depositing these films has been a standard for several years and most PECVD tools support this. The silicon nitride deposition technology knowhow is so widespread that it isn't even aggressively promoted (See Two-In One With PECVD).
The current survey features 8 products from 6 suppliers, and none are new, as they feature in one or the other sections discussed above. While there is nothing groundbreaking that is happening in terms of the process, Ideal Deposition has an interesting tool platform in the market. The Ideal PECVD System applies the SiNx layers on both sides of the wafer in one go. It is still a tube PECVD device built on direct plasma technology, but it comes with a trick – the tool is provided with a special arrangement that flips the wafer front to back without unloading it. Although there is no benefit in the actual process time, as the deposition time doubles, one cycle of heating and cooling can be avoided overall. But according to the company's technology team, the main benefit is coming from eliminating the stress in wafers. The integrated steps avoid the possibility of warpage or wafer deformation originating from the stress caused by the single side deposition at higher temperatures and quickly cooling to room temperatures as part of the process.
Banking on its experience of installing and commissioning such SiNx deposition tools, Centrotherm's c.Plasma XL – SiN tool supports deposition of a variety of silicon nitride layers and stacks. The deposited films have a refractive index ranging from 1.95 to approximately 2.7. The company also offers a nitrous oxide upgrade for depositing silicon oxynitride, nitrous oxide being the obvious addition that needs to be pumped into the process chamber. It involves depositing a sequence of special layers with different stoichiometric ratios of silicon oxide, silicon nitride and silicon oxynitride with a gradient refractive index of 1.5 in order to match it to the EVA used at the module level. This five-stack batch system has a rated throughput of 2,600 wafers per hour.
Except for the process related differences, the silicon nitride deposition systems from Semco, S.C New Energy and Naura are the same as the above discussed respective aluminum oxide deposition systems. The difference with Naura is that it has provided data for 3 systems, which by and large differ in throughputs only marginally. The HORIS P12571A, HORIS P12622 and HORIS P12631 process 3,733, 3,456 and 3,894 wafers of G12 size per hour, respectively.