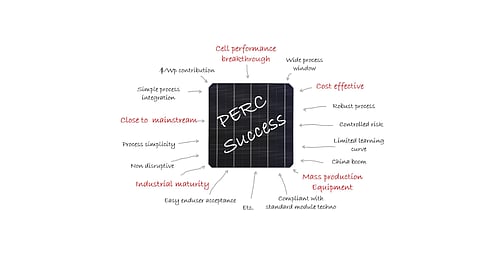
Passivated contacts could be the next big thing after PERC, which undoubtedly became the new standard in solar cell manufacturing. PERC as a technology has made strong progress in improving efficiency in recent year. The majority of PERC lines from leading PV manufacturers are producing cells with average cell efficiencies of 22.2% and above, according to research from TaiyangNews. However, many industry experts see PERC reaching its practical limit of 23% soon, probably in a year's time. Thus, the industry is seriously evaluating the cell technologies beyond PERC. Passivated contacts is considered one serious contestant.
Passivated contacts as an approach is exactly at the same stage as PERC during its commercialization phase – 2014 to 2015. Indeed, when attending presentations about the industrialization of passivated contacts, it is hard to miss at least one slide about the similarities of passivated contacts and PERC.
Passivated contacts following footsteps of PERC
Many consider passivated contacts the direct successor for PERC. One strong advocate of this idea is Raymond de Munnik, CEO of Semco Smartech, originally a French PV equipment maker that is now owned by a Chinese company. There are several parameters to consider when predicting next-generation technology (see graphic), but the most important one is that it 'must be close to the mainstream,' according to de Munnik. Considering PERC is today's standard, passivated contacts technology qualifies for all those parameters and offers the same benefits PERC had over BSF, according to de Munnik, who provided his views on this technology in an interview with TaiyangNews (see Passivated Contacts Will be the Next Thing!). For example, passivated contacts cells have about 20 mV higher Voc compared to today's PERC, which is the same advantage PERC showed over BSF. Passivated contacts also require two to three additional process steps and the appropriate production equipment, depending on the base process. While the BSF cell has a full rear contact, but weak passivation; PERC features good passivation, but only has partial contacts. Passivated contacts, on the other hand, enable both full contact and passivation.
A graph published by Fraunhofer ISE that mapped the average industrial efficiency of different cell technologies, shows a 0.6% efficiency gain per year. Staying with single junction, the graph shows that passivated contacts is the only approach to take cell efficiencies to the next level. However, the evaluation of ISE, which has been strongly involved in the development of passivated contacts cell technology, misses HJT, which reaches even higher efficiencies.
The similarities between PERC and Passivated contacts were shown in a presentation of Yifeng Chen, vice director of high efficiency cells R&D at Trina Solar during PV CellTech 2019. Just like PERC during its inception days, the industrialization of passivated contacts raises several questions, for instance how to implement the technology, starting from substrate selection to metallization process. This includes methods for oxide growth, deposition technologies, optimized cell structure, process flow, costs and etc. (see table below)
Brief history of passivated contacts
Passivated contacts using a stack of silicon oxide and doped polysilicon is not a new concept. Such structures were first used in bipolar junction transistors in the 1970s in semiconductor applications. The approach has been implemented for PV related applications about a decade later, around 1980. Well known Australian solar scientist Martin Green developed cell architectures using tunneling oxides and polysilicon stacks in 1983. The technology first saw the commercial light in 2009 when SunPower introduced a tunnel layer passivated interdigitated back contact cell structure. However, German research institute Fraunhofer ISE brought the technology into the limelight in 2014, when it announced 23% efficiency on a small area and gave the technology a name – TOPCon. The research institute still holds the best monofacial cell efficiency of 25.8% for a TOPCon structure. Adapting passivated contacts technology to the IBC structure, research institute ISFH has developed a cell architecture called POLO that has attained an efficiency of 26.1% in 2018.
Due to this high efficiency potential, similarities with PERC from a manufacturing point of view, the possibility of an organic upgrade from PERC passivated contacts is gaining popularity. And the technology has several qualities that could make it the next big thing after PERC. However, so far only few companies have jumped on the passivated contacts commercial bandwagon – and that will only change once the pioneers have proven that efficiency improvements are large enough to justify the additional investment cost.
For details on further important aspects of passivated contacts technology, see TaiyangNews Report on High Efficiency Cell Technologies 2019.