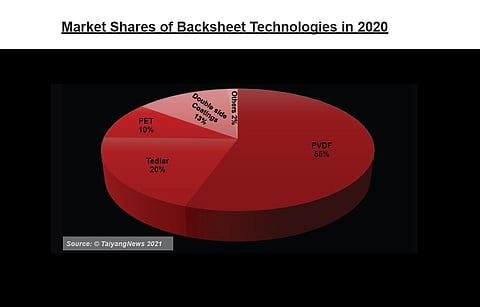
While every layer of a typical 3-layered backsheet is important, the outer UV protection layer is the most critical. It not only takes most of the responsibility of protecting the module from weathering – the primary job of a backsheet – the versatility and variety is also high. When it comes to the core layer, PET has been serving as the universal core layer. As for coatings, be it the inner side or the outer, these formulations are proprietary for their developers and thus the generic differences are hard to identify. Within the fluoropolymers branch, especially in the film based segment, the choice for the outer layer is between PVDF and Tedlar.
PVDF is the leading composite for the outer layer of the backsheet. More than 50% of the modules made in 2020 have used backsheets based on this fluoropolymer. According to Wei from Fumotech, the leading supplier of PVDF, about 300 million m2 of PVDF was used by the PV industry in 2020, half of which has been supplied by the company. "We shipped 150 million m2, equivalent to backsheets worth 30 GW and a market share of 25% in the backsheet business," said Wei. The company has an installed production capacity of 250 million m2.
ZTT is another leading PVDF supplier. The company was also an important backsheet supplier with 50% captive consumption, but chose to exit the backsheet business due to lean margins. With an installed capacity of 300 million m2 that is also serving other industries, ZTT shipped about 80 million m2 of PVDF to backsheet suppliers.
Since PVDF is such an important component, some backsheet suppliers are also producing PVDF in-house. Leading backsheet maker Cybrid operates a PVDF production facility with a capacity of 20 GW.
While 2020 was a good year for PVDF manufacturers. PVDF is a key challenge now as the price of the resin has increased significantly, which is also making related backsheets expensive. On the other hand, module producers are under high pressure to reduce cost. Consequently, backsheet manufacturers are pushing other configurations such as coatings and non-fluoropolymers. Even glass is gaining demand on account of high PVDF prices.
PVF, or Tedlar, which is exclusively supplied by DuPont, is also benefiting from the high PVDF prices. Tedlar, even with its high price tag but a proven track record in terms of reliability, is mainly used by two world leading module manufacturers – JinkoSolar and LONGi Solar. Since these PV giants have been expanding considerably, so is the demand for Tedlar. Not only that, DuPont has started offering a clear variant of its Tedlar for use in transparent backsheets for bifacial applications instead of glass. Backed by extensive testing, DuPont has convinced module JinkoSolar to offer the same 30-year power warranty as glass. The high price of glass at the end of 2020 also motivated a few module makers to adopt Tedlar-based transparent backsheets, according to DuPont's Mark Ma, who declined to reveal exact shipping data, "as a policy of the company." However, our research indicates that Tedlar-based backsheets were used in roughly 22 – 25 GW of modules in 2020.
PET is another important backsheet component. In addition to being the unanimous choice for the core layer, the chemistry of the polyester film is also optimized with UV protection attributes to be used as the outer layer. DTF, the inventor of polyester films, is active in supplying PET for core layers as well as the outer layer. Like any other component supplier, DTF also supplies backsheet components, but not the final product. However, the company, in close cooperation with Coveme, played an instrumental role in the development and commercialization of PET-based backsheets. DTF offers its PET solutions to the PV industry under the Mylar brand name. The UVHPET range is specially designed for enhanced UV barrier and hydrolysis resistance properties to serve as the outer layer of the backsheet. "We have a proven track record of using Mylar UVHPET in 200 million modules, which is 50 GW," emphasized DTF's PV marketing manager Steven Davies. However, he did not disclose any shipment data. The company also supplies a Mylar core PET film, which according to DTF has been used since the birth of the solar industry and can complement any outer layer.
According to our research, in 2020, PVDF had a market share of 55%, while Tedlar had a owned above 20%. Backsheets with coatings on both sides – with fluorine-based coatings dominating the segment –, had a 13% share and PET contributed 10%. Other structures represented the remaining 2%. However, due to the increase in the price of PVDF, the share of backsheets that are not using PVDF will considerably increase by the end of this year.
The Text is an excerpt from TaiyangNews' recent Market Survey on Backsheet and Encapsulation Materials, which can be downloaded for free here
An overview of the survey was presented during TaiyangNews Conference on Reliable PV Module Design. To learn more about the conference and view the presentations click here
Today the work horses of the solar industry are still PERC cells, TaiyangNews will organize a virtual conference on Pushing PERC Cells to Its Limits on March 22, 2022. To register for free, please click here.