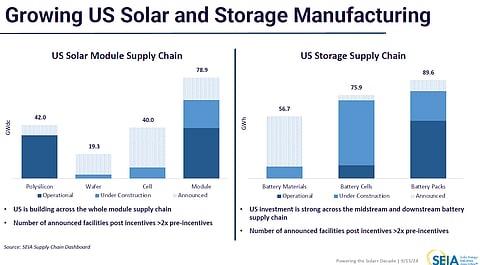
Session 1 of the physical conference was focused on the US' policy, incentive, cost and technology
The participants were representatives from RCT Solutions, SEIA, Department of Energy (DOE), and the Department of Strategy & Education
All participants unequivocally urged to cease the ongoing global IP-lawsuit war and to adopt a progressive global attitude towards technology
It concluded with a panel discussion on the US' potential to become the next big global solar manufacturing hub
Session 1 of the Solar – Made in the USA physical conference featured representatives from TaiyangNews, the Department of Strategy & Education, the Department of Energy (DOE), SEIA, and RCT Solutions. The agenda of this session focused on Solar Made in the USA – Policy, Incentive, Cost & Technology Overview. This conference was conducted on the sidelines of the RE+ 2024 exhibition in Anaheim, CA, co-hosted by EUPD, RE+, and TaiyangNews on September 9, 2024.
Stacy J. Ettinger, SVP of Supply Chain & Trade at SEIA, started by referencing the “U.S. Solar Market Insight Q3 2024” report drafted in collaboration with SEIA and Wood Mackenzie. The report reveals that in the 1st half of 2024, more than 90% of new generation capacity added in the US were from renewable energy (RE) sources, while solar accounted for 67% of new capacity additions to the grid. She also presented a forecast indicating up to 250 GW of new solar deployment by 2029. Ettinger highlighted the significant growth in solar-plus-storage systems over the past 2 years, particularly in the US distributed generation (DG) segments, including the residential and commercial markets. This growth, she noted, is driven by challenges faced by US consumers, such as grid outages and changes in state incentives.
Discussing upcoming manufacturing capacity additions in the US, particularly in PV modules and storage-related components, Ettinger expressed confidence in achieving self-sufficiency in the coming years, spurred by government-sponsored incentives, including the Inflation Reduction Act (IRA). However, she cautioned that it will be important to monitor how these incentives are implemented, as challenges such as labor shortages, interconnection delays, network upgrades, and high interest rates could impact progress.
The next presentation by Prof. Peter Fath, CEO of RCT Solutions, provided a comparative analysis of the "Cost Competitiveness of US Solar Manufacturing," drawing on his extensive experience in designing PV factories across the global value chain. After giving a brief overview of RCT Solutions, Prof. Fath emphasized the importance of establishing gigawatt-scale capacity at every step of the value chain, including modules, cells, ingots, and wafers.
He highlighted the decline of PV module manufacturing capacities in Germany over the past year, largely due to the influx of low-cost Chinese modules, and questioned why the US has yet to develop significant gigawatt-scale manufacturing capacities. Prof. Fath identified several factors hindering the growth of US PV manufacturing, including suboptimal location selection, prohibitively high construction material costs, extended planning timelines, and high labor costs.
Next, he discussed the major cost factors affecting manufacturing in the US, including the economy of scale for optimized CapEx, labor costs, and electricity tariffs for energy-intensive plants such as ingot production and high-efficiency cells. Referring to the total cost of ownership (COO) in $/Wp, irrespective of cell technologies or geographical locations, Prof. Fath presented a cost comparison chart from RCT Solutions that showed a $0.10/Wp delta between China and the US (or Germany). He explained that the primary contributors to this high COO in Europe and the US are high labor costs, high depreciation of equipment, and the elevated cost of imported materials.
Building on this, Prof. Fath pointed out that Chinese modules, which have a total production cost of $0.16/Wp, are being sold at $0.10/Wp, raising concerns about the competitiveness of US and European manufacturers. He also demonstrated that using locally produced PV modules in solar plants has a significant impact on the levelized cost of electricity (LCOE). In countries with low system costs, the LCOE increases by 5% to 8%, while in Germany and the US, it rises by as much as 13% and 17%, respectively, compared to Chinese-made modules.
Prof. Fath noted that this LCOE delta could potentially be offset through government incentives, low-cost debt financing, and other measures. To conclude, he provided a brief comparison between Asian-made and European-made production tools, evaluating key metrics such as ramp-up duration, local certification costs, and the efficiency of water and chemical use.
Panel discussion
Prof. Peter Fath’s presentation was followed by a panel discussion featuring representatives from RCT Solutions, SEIA, the Department of Energy (DOE), and the Department of Strategy & Education. The panel was moderated by Michael Schmela, Managing Director of TaiyangNews. The topic of the discussion was: "Is the U.S. Set to Become the Next Big Global Solar Manufacturing Hub?"
Prof. Peter Fath from RCT Solutions shared a strong critique of the ongoing global intellectual property (IP) disputes. He argued that the IP-related litigation filed by Chinese companies against European and US players is detrimental to the industry, as it will only serve to slow its progress. He pointed to historical instances where Chinese companies had copied German tools without facing legal action, suggesting that this legal conflict should cease in favor of fostering a more collaborative global attitude toward solar technology.
Dr. Paul Basore, Chief Solar Scientist at the Department of Energy, commented on the wide-ranging policies in the US, noting that the government has a comprehensive "toolbox" of incentives and regulations. He mentioned that while many announced ambitious plans following the passage of the Inflation Reduction Act (IRA), some now realize that achieving their goals is more challenging than anticipated. Dr. Basore emphasized the need to put an end to internal industry conflicts and instead work towards a win-win situation for all stakeholders. He also called on Chinese companies to improve supply chain traceability.
Dr. Radovan Kopecek, Head of the Department of Strategy & Education and a member of the Executive Committee, echoed concerns about the global IP disputes. He shared that India has just completed the technology transfer for TOPCon to one major player, with another transfer expected by the end of the year.
Stacy J. Ettinger, SVP of Supply Chain & Trade at SEIA, highlighted their ongoing efforts to establish traceability standards, which are expected to be finalized in the near future.