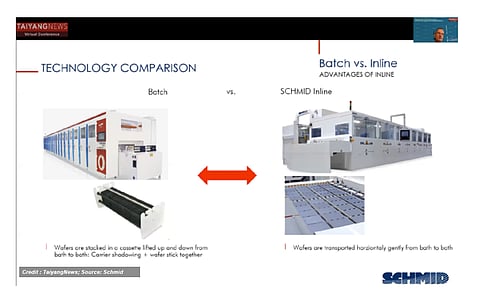
Our previous article on solar cell processing equipment provides an overview of key process steps – surface preparation, emitter formation, passivation, metallization and testing (see The Main Solar Cell Production Equipment Updates). With this article, we begin looking into details about each of the PERC/TOPCon solar cell process steps and start with surface preparation. The silicon slices entering the cell lines come with some inherent flaws such as saw damages originating from the wafering station. The wet benches not only get rid of these damages, but also convert the glossy wafer surface into a matt color in order to reduce reflectivity. This process, called as texturing, is the heart of the surface preparation station. The wet benches are also used to remove the glass (BSG or PSG) and for edge isolation. The tools have an additional function in case of TOPCon where they are also used to remove the wraparound on the emitter side, which is nothing but the undesired deposition of polysilicon on the front side.
Etching is the ultimate goal of the wet-chemical treatment employed at various stages of solar cell processing. However, the degree and intensity of etching, and the type of chemicals used for a particular purpose, vary from one application to the other. In the current survey, we have data for 23 products from 5 companies. These tools are based on different configurations and applications —SDE, texturing, doped glass removal, edge isolation, rear side polishing and polysilicon wraparound etching.
The one that is somewhat special among these is from Schmid. Having been active in the business of supplying production equipment for PV since 2002, the company is a strong advocate of the inline philosophy. All wet-chemical solutions of the company for TOPCon and PERC, including texturing, polishing, poly wrapround etch and glass removal, are based on an inline configuration. In contrast, the texturing systems from all the other companies are predominantly batch tools. According to Christian Buchner, Vice President of the PV business unit at Schmid, unlike batch systems, where wafers are stacked in a cassette that is moved around, wafers move gently on a conveyor from bath-to-bath with Schmid's inline tools (see Christian Buchner's presentation: Innovations in Wet-Chemical Solutions).
The other advantages of the inline modus operandi highlighted by Buchner are avoiding carrier marks, touching the wafers and chances of wafers sticking together; especially with wafers getting larger and thinner, the risk of breakage increases. "The breakages with the inline systems are typically half compared to batch tools," says Buchner. Schmid's tools are primarily designed for single side processing, but they can also support immersion with acidic processes, predominantly with HF. While the company does list its old generation products based on nitric acid chemistry, its latest generation products are free from nitric acid.
Moving to notable developments, TOPCon has now become the point of reference for any product improvement for most of the equipment vendors. The hot topic for RENA in this regard is optimizing the texturing process to attain a reflection below 9% by means of new additives exclusively developed for TOPCon. RENA is also ready with its cluster solutions for junction isolation and polysilicon etch. On the other hand, the company considers inline processing is more attractive over the cluster processing for these applications. Damian Brunner, senior R&D manager solar & battery at RENA, says that while cluster solutions are the way to go when following the practices in China, inline solutions, for example for the poly warp etch, are still beneficial keeping in view the latest PECVD based polysilicon deposition methods and gaining independence from additives-based processes. However, until it is clear which technology turns out to be the best, probably in a couple of years from now, RENA would push both cluster and inline solutions. While not explicitly highlighted, cleaning is increasingly becoming important for TOPCon vis-à-vis PERC, and ozone based cleaning is the state of the art followed by most of the companies. In the next article on cell production equipment we will look into details of texturing.
The article is an excerpt from the TaiyangNews Market Survey on Solar Cell Production Equipment 2023, which can be downloaded for free here.